Woojoong Kim
(김우중)
1
Yongwoo Yang
(양용우)
1
Younghun Kim
(김영훈)
1
Sungseek Park
(박성식)
2
Namjin Kim
(김남진)
1†
-
Department of Nuclear and Energy Engineering, Jeju National University, Jeju, 63243,
Korea
(제주대학교 에너지공학과)
-
Jeju Institute of Quality, Korean Foundation for Quality, Jeju 63309, Korea
(한국품질재단 제주품질연구원)
Copyright © 2016, Society of Air-Conditioning and Refrigeration Engineers of Korea
keywords
Carbon nanotube, Nanofluid, Flow boiling heat transfer, Critical heat flux, Heat transfer coefficient
키워드
탄소나노튜브, 나노유체, 유동 비등 열전달, 임계 열유속, 열전달 계수
1. 서론
비등 열전달은 각종 발전 시스템, 열교환기, 냉방 및 냉동 시스템과 같이 다양한 산업에서 이용되며 매우 중요시 되고 있다. 비등 열전달 시스템에서
임계 열유속은 중요한 인자로서, 열전달 시스템의 최대 한계 또는 시스템 안전성을 나타내기도 한다. 비등 열전달 시스템에서 임계 열유속 발생 시, 급격한
온도 상승으로 인하여 열전달 시스템에 물리적인 손상을 일으킬 수 있다. 따라서, 시스템의 성능을 극대화하고 안전성을 높이기 위하여 임계 열유속 향상이
필수적이다. 이와 관련하여 비등 열전달 시스템의 작동유체를 기본유체보다 열적 특성이 높은 나노유체를 사용할 경우 임계 열유속이 증가한다고 보고되었다.(1)
(2)
Lee and Mudawar(3)는 산화알루미늄(Al2O3) 나노유체를 사용하여 마이크로채널 냉각 운전에서 단일 상의 층류에서는 임계 열유속이 상승하였으며, 이상의 유동일 경우에 나노입자가 수로 끝에서 뭉치는
현상이 있음을 보고하였다. Peng et al.(4)은 R-113 내에 산화구리(CuO) 나노입자를 분산시켜 나노유체를 제조하였으며, 구리관 내의 유동 비등에서 비등 열전달 계수가 30%까지 향상되었음을
보고하였다. Kim et al.(5)은 산화알루미늄(Al2O3), 산화아연(ZnO), 다이아몬드 나노유체를 제조하여 사용하였다. 나노유체의 질량 유속과 나노입자 농도가 증가할수록 임계 열유속이 최대 53%까지
향상되었으며, 낮은 열유속에서 비등 열전달 계수가 소량 증가했음을 보고하였다. Ahn et al.(6)은 산화알루미늄(Al2O3) 나노유체를 사용하여 풀 비등과 유동 비등에서 임계 열유속을 측정하였으며, 히터 표면에 나노입자의 증착으로 인하여 임계 열유속이 향상되었음을 보고하였다.
이와 같이 나노유체는 우수한 열적특성을 가지고 있지만, 실제 열전달 시스템에 적용 시 나노입자들이 열전달 표면에 침착되는 나노 파울링(Fouling)
현상이 발생할 수 있다. 이는 나노유체 적용 시 최대 문제점으로 알려져 있으며, 이와 같은 나노 파울링이 열전달 시스템의 열효율과 안전성에 미치는
영향에 대한 연구가 미미한 실정이다.
따라서 본 연구에서는, 비등 열전달 시스템에 나노유체를 적용 시 나노유체의 침착현상이 시스템 열전달 성능 및 임계 열유속 현상에 미치는 영향을 파악하기
위해, 인공 나노 파울링 상태를 만들어 나노유체 0.5~1.5 m/s의 유동 조건에서 파울링에 따른 임계 열유속 및 비등 열전달 계수에 미치는 영향을
비교분석하였다.
2. 실험장치 및 방법
2.1 탄소나노튜브 나노유체
본 연구에서는 Park et al.(7)과 같이 다중벽 탄소나노튜브(Multi-Wall Carbon Nanotube CM-100, MWCNT, Hanwha-nanotech Co.)를 화학적
개질에 의한 분산법을 이용하여, 산화처리된 다중벽 탄소나노튜브(Oxidized MWCNT, OMWCNT)를 제조하였다. 본 연구에서 사용한 나노유체는
산화처리된 다중벽 탄소나노튜브를 증류수와 0.001 vol%의 농도로 제조하였으며, 나노유체의 분산안정성 확보를 위해 기계적 분산법 중 하나인 초음파
분산을 이용하여 나노유체를 제조하였다. 초음파 분산은 500 W급 초음파 분산기(VC-505, Young- Jin Co.)를 사용하였으며, 나노유체에
2시간 동안 초음파 분산하여 나노유체를 제조하였다. 본 연구에서 사용한 본래의 다중벽 탄소나노튜브에 대한 물성치는 Table 1 과 같이 나타내었다.
Table 1 Properties of multi-wall carbon nanotube CM-100
Properties
|
MWCNT
|
Diameter(nm)
|
10~15
|
Length(μm)
|
~200
|
Purity(wt.%)
|
95
|
Bulk Density(g/㎤)
|
0.05
|
True density(g/㎤)
|
1.8
|
Thermal Conductivity(W/m·K)
|
3,000
|
Surface Area(㎡/g)
|
225
|
2.2 유동 비등 열전달 실험장치
본 연구에서 사용된 유동 비등 열전달 실험장치의 개략도는 Fig. 1과 같이 나타내었다. 반응용기는 알루미늄 합금의 재질을 사용하였고, 유동 비등과 임계 열유속의 발생과정을 관찰할 수 있도록 폴리카보네이트(PC)창을
설치하였다. 반응용기 상단에는 반응용기 내부에서 증발된 증기를 냉각시키기 위하여 2개의 환류냉각기를 설치하였으며, 저온순환항온수조(RW-3025G,
Jeio-tech)와 연결하여 냉각수를 순환시켜 증기를 냉각하였다. 또한, 반응용기 내부 작동유체의 온도와 압력을 측정하기 위하여 2개의 K-type
온도센서(Tctechnology Co.)와 1개의 압력센서(PSCD0002BCPG-HSA, Sensys Co.)를 반응용기 상단에 설치하였다. 임계
열유속이 발생하게되면 반응용기 내부의 급격한 온도 상승으로 인하여 실험장치가 파손될 수 있기 때문에 온도센서에 온도조절기(NX9, Hanyoung
nux)를 연결하여 임계 열유속 발생 시 히터 공급 전력을 차단하도록 하였다. 효과적으로 유속을 발생시키고 제어하기 위하여 질량유량계(F025S113CCAZEZZZZ,
Micro Motion Inc.)와 마그네틱 펌프(20JMTF-11CB, JoongWon SMET Co.)를 설치하였으며, 펌프는 인버터(SV008iG5A-2,
LSIS Co.)를 이용하여 제어하였다. 유동 비등 실험 시 측정 데이터 저장과 모니터링을 위하여 데이터로거(34970a, Agilent)와 컴퓨터를
설치하였으며, 측정 데이터 수집은 데이터 측정 프로그램인 Labview를 자체적으로 제작하여 사용하였다.
Fig. 1 Schematic diagram of flow boiling CHF experimental apparatus.
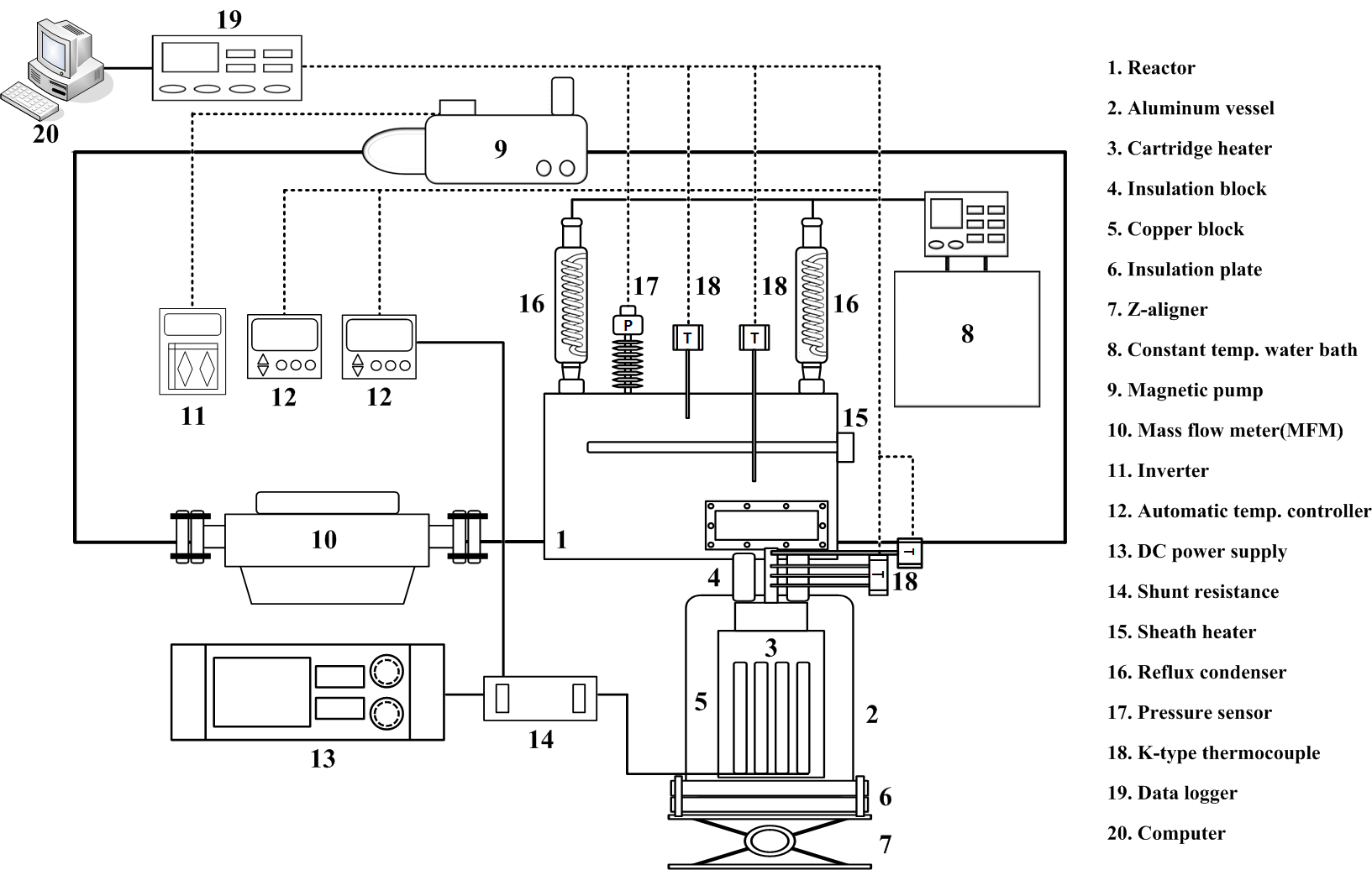
Fig. 2는 본 실험에 사용된 유동 비등 열전달 실험 시편을 개략도로 나타내었다. 유동 비등 열전달 실험 시편은 지르코늄(Φ10×5 mm)과 히터의 열이 다른
곳으로 전달되지 않도록 단열재인 PEEK(Φ70×5 mm), 직경 1 mm의 K-type 온도센서로 구성되어 있다. 실험 시편에 열을 공급하는 히터는
무산소동(99.9%) 구리로 제작하였으며 구리 히터 내부에는 500 W급의 카트리지 히터 8개를 구성하고 2,000 W급 직류전원공급기와 연결하여
최대 4,000 W의 열량을 발생할 수 있도록 하였다. 또한 열손실을 줄이기 위하여 1,200℃까지 사용 가능한 세라믹 단열재를 알루미늄 용기와 히터
사이에 삽입하였다. 구리 히터 상단에는 직경 1 mm의 K-type 온도센서를 7 mm간격으로 삽입하여, 실험 시편으로 공급되는 열유속을 측정할 수
있도록 구성하였다.
Fig. 2 Schematic diagram of flow boiling CHF experimental specimen.
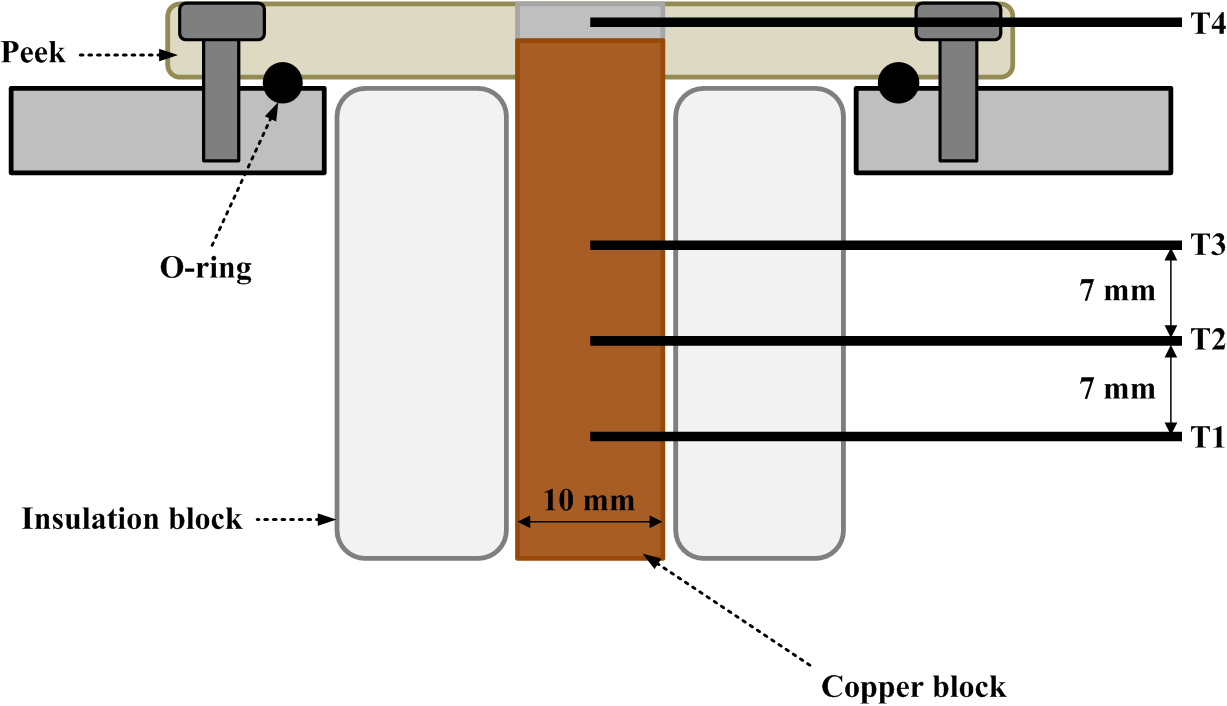
또한 열전달 표면의 인공 파울링 상태를 구성하기 위하여 Park et al.(8)의 분사증착 코팅 시간을 참고하였다. 이 연구에서는 풀 비등 열전달에서 산화처리된 다중벽 탄소나노튜브의 분사증착 코팅 시간에 따라 임계 열유속은 증가하였으나,
열전달 계수는 코팅시간이 180초에서 가장 높았으며 180초를 중점으로 열전달 계수 증가율이 양(+)에서 음(-)으로 떨어짐을 보고하였다. 따라서
본 연구에서는 산화처리된 다중벽 탄소나노튜브의 분사증착 코팅 시간을 180초로 정하여 실험 시편 표면에 분사증착 코팅을 수행하였다. 제조된 나노유체를
실험 시편에 분사증착 후 건조를 반복하여 총 180초 동안 분사증착 코팅 상태의 실험 시편을 제조하였다. 분사코팅은 압축 공기를 사용해 일정하게 분사시키는
0.3 mm 노즐의 중력식 에어분사기(HP-CP, Iwata Co.)를 시편과 일정한 높이에서 분사하였으며, 나노유체 분사 후에는 100℃를 유지하는
건조기(WOF-155, Wiseven)에서 건조시켜 나노입자를 실험 시편 표면에 증착시켰다.
2.3 유동 비등 열전달 실험 방법
본 연구에서 유동 비등 실험방법은 먼저 반응용기에 유체를 충분히 채우고 증발되는 증기가 외부로 빠져나가지 않도록 완전 밀폐형으로 조립한다. 그리고
마그네틱 펌프와 질량유량계를 이용하여 순환되는 유체의 속도가 실험속도가 되도록 조절한 뒤 반응용기 내부의 유체를 실험온도로 상승시킨다. 유체의 온도가
실험온도로 상승된 것을 확인한 뒤, 2개의 2,000 W급 직류전원공급기를 이용하여 히터에 전력을 공급하고 열유속을 발생시킨다. 이 때 반응용기 내부의
압력은 1 atm, 유체의 온도는 100℃로 일정하게 유지하였으며, 임계 열유속까지 실험을 수행하고 측정된 데이터를 수집하였다. 임계 열유속이 발생하여
실험이 종료된 후에는 반응용기를 분리하여 깨끗이 세척하였으며, 유동 비등 열전달 실험 시편은 2,000번 사포를 이용하여 시편 표면을 항상 균일하게
유지하였다.
본 연구에서 임계 열유속은 푸리에의 법칙(Fourier’s law)으로 잘 알려진 1차원 정상상태 열전도방정식(1)을 이용하여 계산하였다.
여기서
은 각각 열유속(kW/㎡), 열전도율(W/m·K), 구리 히터에 삽입된 온도센서에서 측정된 온도(℃),
와
사이의 거리(m)이다.
또한 열전달 표면의 과열도를 계산하기 위하여 다음과 같은 식(2)를 이용하여 열전달 실험 시편의 벽면온도를 구하고 과열도를 계산하였다.
여기서,
는 각각 지르코늄의 표면온도(℃), 유체의 포화온도(℃), 지르코늄에 삽입된 온도센서에서 측정된 온도(℃), 지르코늄 표면과 온도센서 사이의 거리(m)이다.
또한, 비등 열전달 계수는 대류 열전달 방정식(3)을 이용하여 계산하였다. 유동 비등 열전달 실험 시편 표면에서의 열전달 계수는 식(4)를 통하여 계산하였다.
2.4 유동 비등 임계 열유속 측정실험의 불확실성 해석
본 연구에서는 Kline and McClintock(9)의 오차 전파 방법을 사용하여 본 실험에서 발생하는 불확실성에 대한 해석을 수행하였다. 본 연구에서 사용한 열유속과 과열도에 대한 식(5), 식(6)을 보면, 열유속에 대한 인자는 구리 히터에 삽입된 온도센서 T2와 T3에서 측정된 온도차와 온도센서 사이의 거리임을 알 수 있으며, 과열도에 대한 인자는 실험 시편인 지르코늄에 삽입되어 있는 온도센서 T4와 유체의 포화온도 Tsat의 온도차, 열유속, 온도센서 T4와 지르코늄 표면까지의 거리임을 알 수 있다. 또한 식(7)은 비등 열전달 계수에 대한 인자이며, 식(5)와 식(6)의 열유속, 과열도임을 알 수 있다. 따라서 열유속, 과열도, 비등 열전달 계수는 다음 인자들의 함수로 표현된다.
식(5)
식(6)
식(7)에서 나타난 인자들을 이용하여 열유속과 열전달 계수에 대한 불확실성 계산식은 다음과 같다.
여기서,
는 각각 임계 열유속, 비등 열전달 계수, T2, T3의 온도센서에서 측정온도차, 온도센서 사이의 거리, 과열도, T4와 유체의 포화온도 Tsat의 온도차, 온도센서 T4와 지르코늄 표면까지의 거리에 대한 불확실성을 나타낸다. 위 식으로부터 계산된 열유속과 과열도의 불확실성은 열유속 100 kW/㎡에서 각각 10.63%,
15.04%이며, 열유속 1,100 kW/㎡에서는 각각 2.44%, 2.45%임을 알 수 있었다.
3. 실험 결과
3.1 유동 비등 임계 열유속 측정실험의 신뢰성 평가
본 연구의 실험장치 및 방법의 신뢰성과 재현성을 확인하기 위하여 순수 물을 이용한 임계 열유속 실험을 수행하였다. 순수 단일유체 풀 비등 실험의
임계 열유속 예측 상관식 중 Zuber(10)가 제시한 임계 열유속 상관식(11)을 가장 많이 이용하고 있다. 따라서, 본 연구에서도 Zuber가 제시한 임계 열유속 상관식을 이용하였으며, 풀 비등에서의 순수 물에서 측정된 임계
열유속 실험 데이터와 비교하였다.
여기서,
는 각각 증발잠열(kJ/kg), 기체밀도(kg/㎥), 액체밀도(kg/㎥), 표면장력(N/m), 중력가속도(m/s2)이다.
또한, 유동 비등 실험의 경우에는 균일한 평면히터의 평행흐름에서 유동 비등 임계 열유속 예측식은 Katto and Kurata(11)의 식(12)를 이용하였으며, 0.5 m/s ~1.5 m/s까지의 순수 물에서 측정된 유동 비등 임계 열유속 실험 데이터와 비교하였다.
여기서, G,l 은 각각 질량유속(kg/s·㎡), 히터길이(m)이다.
Fig. 3은 순수 물의 임계 열유속 실험결과와 Zuber의 상관식, Katto and Kurata의 예측식을 비교하여 나타낸 그래프이다. 본 실험에서 측정한
순수 물의 풀 비등 임계 열유속은 각각 1,050 kW/㎡, 1,130 kW/㎡, 1,160 kW/㎡이며, Zuber의 예측식으로 계산한 임계 열유속은
1,106.28 kW/㎡으로 거의 일치함을 확인할 수 있다. 무한 수평 상향 평면에서의 Zuber의 예측식은 본 실험에서 사용된 평면 실험 시편에서의
임계 열유속 값을 매우 정확하게 예측한 것으로 판단된다. 측정된 3번의 실험결과는 Zuber의 예측식과 5.08% 이내로 일치하였다. 또한 본 실험에서
측정된 0.5, 1, 1.5 m/s에서의 유동 비등 임계 열유속이 각각 1,216 kW/㎡, 1,553 kW/㎡, 1,982 kW/㎡로 Katto
and Kurata의 예측식과 약 8.5 %이내의 오차로 일치함을 확인하였다. 따라서 본 연구에서 사용된 실험장치의 높은 신뢰성을 확인할 수 있었다.
Fig. 3 CHF comparison of pure water.
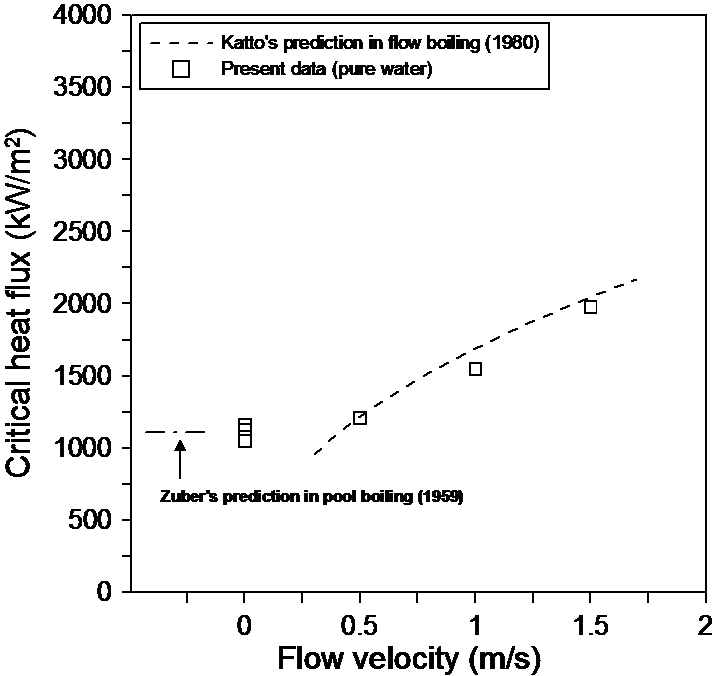
3.2 인공 파울링 여부에 따른 나노유체의 임계 열유속
Fig. 4는 0.001 vol%의 산화처리된 다중벽 탄소나노튜브 나노유체에서 유속에 따른 임계 열유속 비등 곡선을 나타낸 그래프이다. 그림을 보면 알 수 있듯이
유속이 증가할수록 산화처리된 다중벽 탄소나노튜브 나노유체의 임계 열유속이 증가하고 있음을 확인할 수 있다. 산화처리된 다중벽 탄소나노튜브 나노유체의
유속 0.5 m/s, 1 m/s, 1.5 m/s에서 측정된 임계 열유속은 0 m/s보다 각각 7.65%, 32.00%, 62.64% 증가됨을 확인하였으며,
비등 열전달 표면과 유체의 포화온도의 차이인 과열도 역시 이와 비례하여 증가함을 알 수 있었다.
Fig. 4 CHF of oxidized multi-wall carbon nanotube nanofluids.
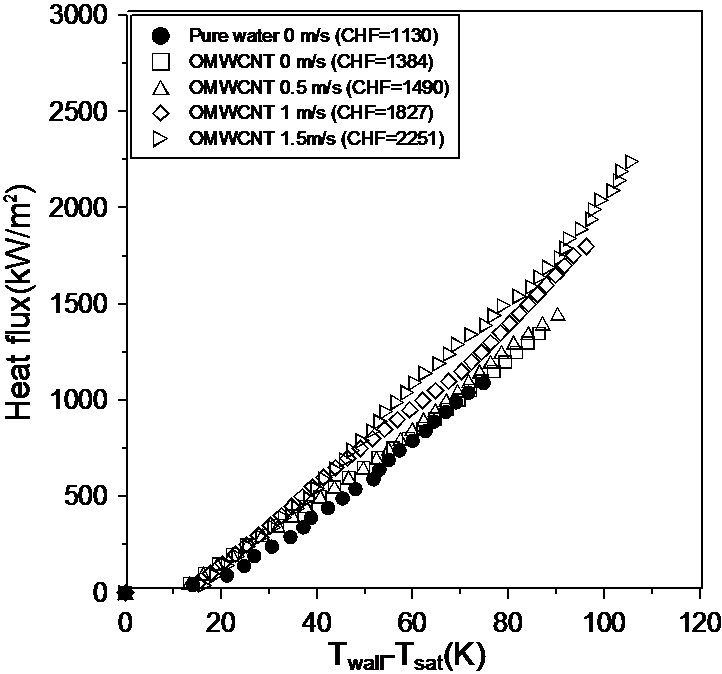
Fig. 5는 산화처리된 다중벽 탄소나노튜브 나노입자 코팅 상태에서 0.001 vol%의 산화처리된 다중벽 탄소나노튜브 나노유체의 유속에 따른 임계 열유속 비등
곡선을 나타낸 그래프이다. 그림을 보면 알 수 있듯이 코팅상태에서 유속이 증가할수록 산화처리된 다중벽 탄소나노튜브 나노유체의 임계 열유속이 크게 증가하고
있음을 확인할 수 있다. 산화처리된 다중벽 탄소나노튜브 나노입자 코팅 상태에서의 유속 0.5 m/s, 1 m/s, 1.5 m/s에서 측정된 임계 열유속은
0 m/s보다 각각 12.06%, 39.51%, 56.78% 증가함을 확인하였다. 나노입자 침착 상태에서 유속에 따른 임계 열유속은 나노입자를 침착하지
않았을 때보다 크게 증가됨을 알 수 있었다. Ahn et al.(6)은 Al2O3 나노유체를 사용한 유동 비등 임계 열유속이 크게 증가함을 보고하였으며, 본 연구에서도 나노유체를 사용할 경우 임계 열유속이 향상되어 비슷한 경향을
나타냄을 확인하였다. 또한 나노입자 침착과 유속이 증가할수록 비등 열전달 표면과 유체의 포화온도의 차이인 과열도가 상당히 크게 증가함을 알 수 있었으며,
비등 열전달 시스템에서의 과열도의 증가는 시스템의 온도 상승으로 인하여 물리적 손상을 야기할 수 있는 문제점이 될 수 있을 것으로 판단된다.
Fig. 5 CHF of artificial nano fouling in oxidized multi-wall carbon nanotube nanofluids.
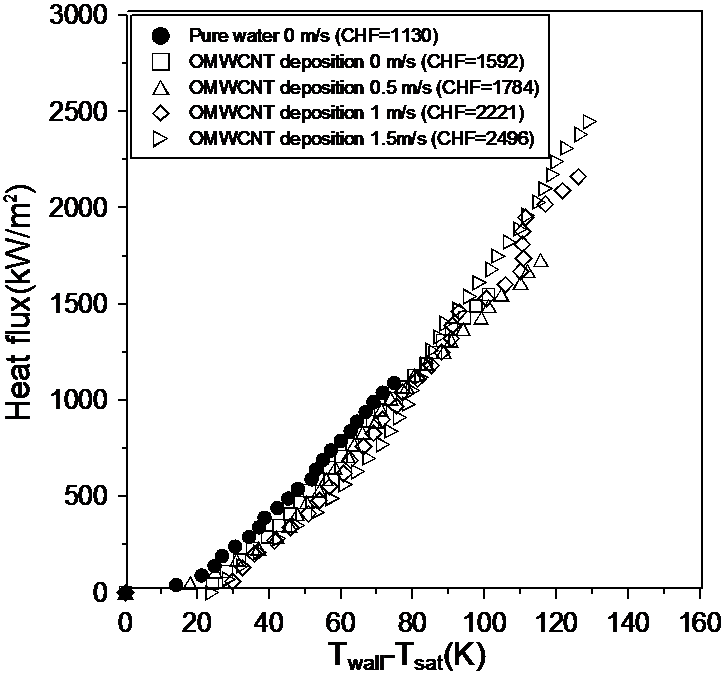
Fig. 6은 유동 비등 열전달 실험 이후 주사전자현미경(SEM)으로 실험 시편 표면을 측정한 사진이며, 나노입자 코팅상태에서 나노유체의 유속이 증가할수록 실험
시편 표면에 탄소나노튜브 나노입자가 파울링 현상과 유사하게 증착됨을 확인할 수 있다.
Fig. 6 SEM micrographs of nano fouling in nanofluid.
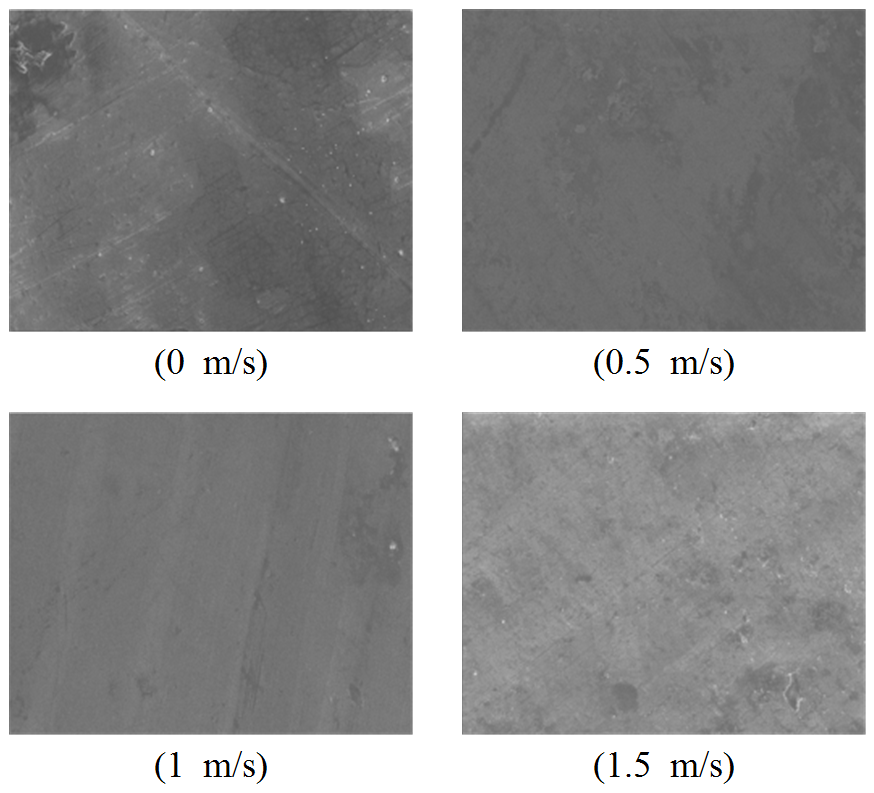
Fig. 7은 순수 물의 풀 비등 임계 열유속을 기준으로 순수 물과 산화처리된 다중벽 탄소나노튜브 나노입자 코팅의 여부에 따른 나노유체의 유속에 따른 임계 열유속
증가율을 나타낸 그래프이다. 그림을 보면 알 수 있듯이 순수 물보다 나노유체상태와 산화처리된 다중벽 탄소나노튜브 나노입자 코팅 상태에서의 유속에 따른
임계 열유속이 매우 높게 나타남을 확인할 수 있다. 특히, 순수 물의 경우 유속 0.5 m/s, 1 m/s, 1.5 m/s에서 측정된 임계 열유속
증가율은 각각 7.61%, 37.43%, 75.39%였으나, 산화처리된 다중벽 탄소나노튜브 나노유체의 유속 0 m/s, 0.5 m/s, 1 m/s,
1.5 m/s에서 측정된 임계 열유속 증가율은 각각 22.48%, 31.85%, 61.68%, 99.2%이며, 산화처리된 다중벽 탄소나노튜브 나노입자
코팅 상태에서의 유속 0 m/s, 0.5 m/s, 1 m/s, 1.5 m/s에서 측정된 임계 열유속 증가율은 각각 40.88%, 57.87%, 96.54%,
120.88%임을 확인하였다. 또한 앞서 설명한 바와 같이 임계 열유속이 증가함에 따라 과열도도 상당히 상승하여 열전달 시스템의 물리적 손상을 야기할
수 있음을 확인하였다.
Fig. 7 CHF enhancement ratio comparison of nanofluid and nano fouling.
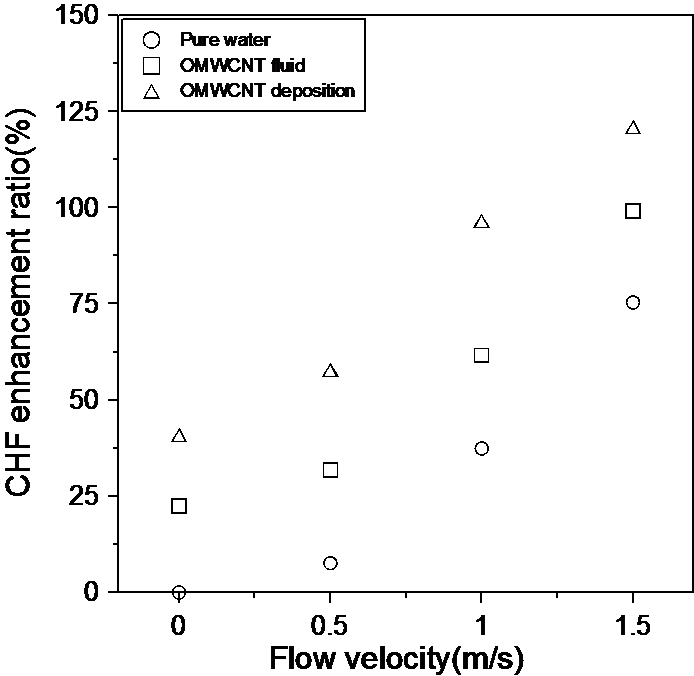
3.3 인공 파울링 상태의 비등 열전달 계수
Fig. 8은 순수 물에서의 유속에 따른 비등 열전달 계수를 나타낸 그래프이다. 그림을 보면 알 수 있듯이 순수 물에서의 유속이 증가할수록 열전달 계수가 증가함을
알 수 있으며, 측정된 열전달 계수는 0.5 m/s, 1 m/s, 1.5 m/s에서 0 m/s보다 각각 3.58%, 11.34%, 29.22% 증가함을
확인하였다.
Fig. 8 Boiling heat transfer coefficient of pure water.
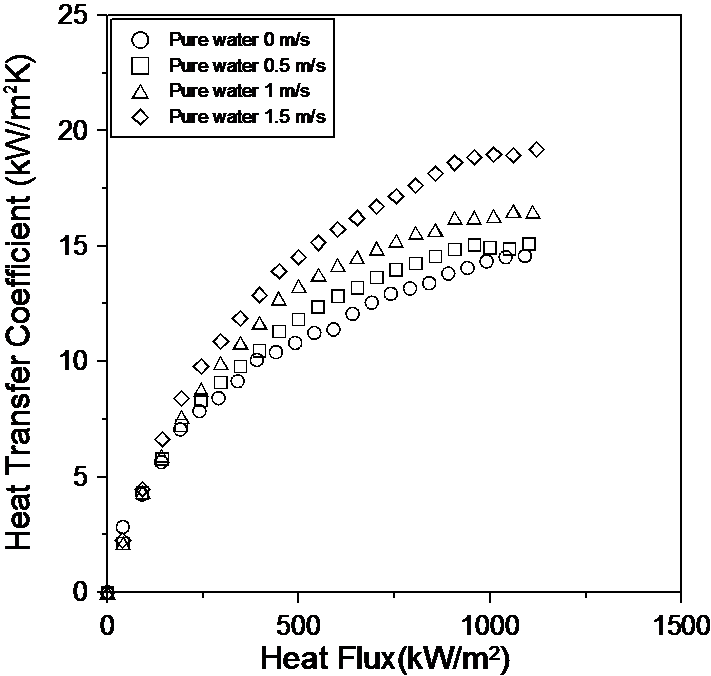
Fig. 9는 순수 물 0 m/s의 비등 열전달 계수와 순수 물의 비등 열전달 계수까지의 0.001 vol%의 산화처리된 다중벽 탄소나노튜브 나노유체에서의 유속에
따른 비등 열전달 계수를 나타낸 그래프이다. 그림을 보면 알 수 있듯이 측정된 열전달 계수는 0 m/s, 0.5 m/s, 1 m/s, 1.5 m/s에서
순수 물의 0 m/s보다 각각 6.28%, 8.43%, 17.21%, 24.29% 증가하였다.
Fig. 9 Boiling heat transfer coefficient comparison of pure water and OMWCNT nanofluids.
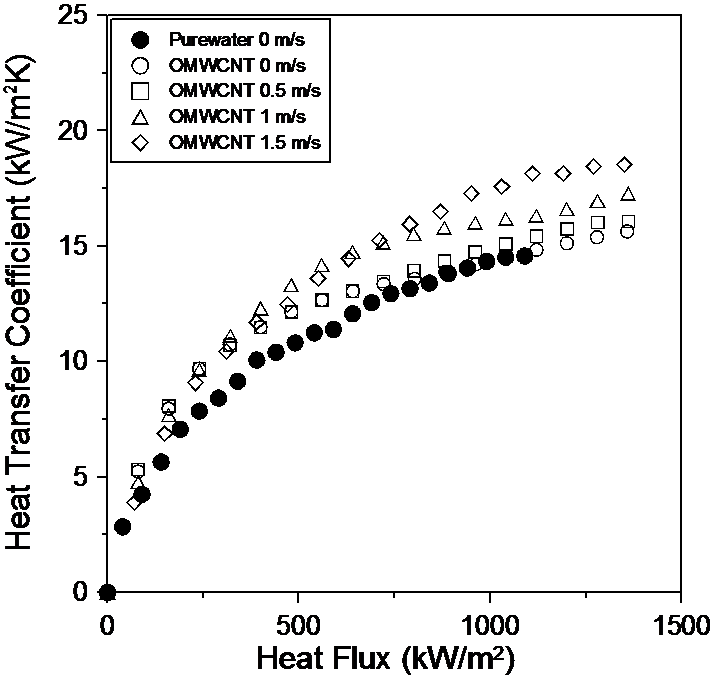
Fig. 10은 순수 물 0 m/s의 비등 열전달 계수와 순수 물의 비등 열전달 계수까지의 산화처리된 다중벽 탄소나노튜브 나노입자 코팅 상태에서 0.001 vol%의
산화처리된 다중벽 탄소나노튜브 나노유체의 유속에 따른 대류 열전달 계수를 나타낸 그래프이다. 그림을 보면 알 수 있듯이 측정된 열전달 계수는 같은
열유속의 0 m/s, 0.5 m/s, 1 m/s, 1.5 m/s에서 순수 물의 0 m/s보다 각각 -5.06%, -5.20%, -7.56%, -7.96%
감소하였다. 비등 열전달 계수 감소에는 여러 원인이 있을 것으로 사료된다. Henderson et al.(12)은 SiO2/R-134a 나노유체를 유동 조건에서 사용하였을 때 비등 열전달 계수가 감소하였으며, 나노유체가 안정된 분산이 되기 힘들기 때문에 감소한다고 보고하였다.
이는 나노입자의 분산이 일정하지 않으면, Sarafraz et al.(13)에서와 같이 중력에 의한 나노입자 침착이 파울링의 원인이 되며, 비등 열전달 계수가 감소하는 것으로 판단된다. 다른 이유로서 비등 열전달 계수가 감소하는
이유는 나노입자가 증착된 열전달 표면과 나노유체 사이의 열전달이 일정하게 일어나지 않기 때문인 것으로 판단된다. 또한 실험 시편 표면에서의 활성 핵
기공의 감소로 인한 기포 생성을 감소시켜 비등 열전달 계수가 감소한 것으로도 판단된다. Park et al.(14)은 나노 유체의 입자가 히터 표면의 표면침착으로 활성 핵 기공의 감소로 비등 열전달을 촉진시키는 기포의 생성을 감소시켜 비등 열전달 계수가 감소하였다고
보고하였다. 나노유체를 통하여 실험 시편 표면의 나노입자 표면침착으로 활성 핵 기공의 감소와 유체의 유동으로 인해 표면의 기포 생성을 방해하기 때문에
비등 열전달 계수가 감소한 것으로 판단되지만, 이러한 현상의 원인을 파악하기 위하여 추후 연구가 필요할 것으로 사료된다.
Fig. 10 Boiling heat transfer coefficient comparison of pure water and nano fouling in nanofluids.
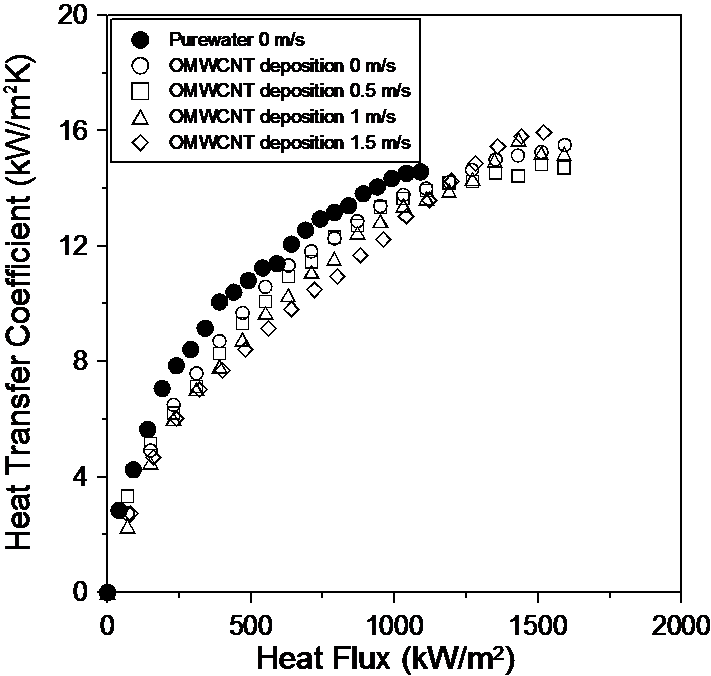
4. 결 론
본 연구에서는 유동 비등 열전달에서의 산화처리된 다중벽 탄소나노튜브 나노유체에서 인공 파울링의 여부에 따른 임계 열유속과 증가율, 비등 열전달 계수와
증가율을 비교분석한 결과 다음과 같은 결론을 얻었다.
(1) 산화처리된 다중벽 탄소나노튜브 나노유체에서 인공 나노 파울링의 여부에 따른 유동 비등 열전달 임계 열유속 실험을 수행한 결과, 유속이 증가함에
따라 임계 열유속과 과열도가 증가하였다. 또한 인공 나노 파울링이 순수 물에서의 임계 열유속과 과열도는 상당히 증가함을 나타내었다.
(2) 순수 물에서의 임계 열유속 증가율을 비교하면, 산화처리된 다중벽 탄소나노튜브 나노유체의 임계 열유속은 유속에 따라 최대 99.2%, 인공
파울링 상태에서 산화처리된 다중벽 탄소나노튜브 나노유체 임계 열유속은 유속에 따라 최대 120.88% 증가함을 확인하였다. 임계 열유속이 증가함에
따라 과열도도 상당히 증가하여 열전달 시스템의 물리적 손상을 일으킬 수 있음을 확인하였다.
(3) 산화처리된 다중벽 탄소나노튜브 나노유체에서의 비등 열전달 계수는 순수 물의 비등 열전달 계수보다 최대 24.70%로 증가하였다. 나노유체에서
인공 파울링의 경우의 비등 열전달 계수는 순수 물의 비등 열전달 계수에 비하여 최대 -7.96%로 감소함을 확인하였다. 이는 나노유체에서 분산된 나노입자가
중력에 의한 열전달 표면의 나노입자 침착으로 파울링의 형성, 또는 나노입자가 증착된 열전달 표면과 나노유체 사이의 열전달이 일정하지 않는 불규칙성으로
비등 열전달 계수가 감소한 것으로 판단된다. 또한 활성 핵 기공 감소 효과와 유체 유동에 의한 기포 생성 방해로 비등 열전달 계수가 감소한 것으로
판단되지만, 이러한 현상에 대해 추후 연구가 필요할 것으로 사료된다.
후 기
이 논문은 2015학년도 제주대학교 교원성과지원사업에 의하여 연구되었음.
References
Das S. K., Choi S. U., Yu W., Pradeep T., 2008, Nanofluids:science and technology,
John Wiley and Sons.

Barber J., Brutin D., Tadrist L., 2011, A review on boiling heat transfer enhancement
with nanofluids, Nanoscale Research Letters, Vol. 6, pp. 280

Lee J., Mudawar I., 2007, Assessment of the effectiveness of nanofluids for single-phase
and two- phase heat transfer in micro-channels, International Journal of Heat and
Mass Transfer, Vol. 50, No. 3/4, pp. 452-463

Peng H., Ding G., Jiang W., Hu H., Gao Y., 2009, Heat transfer characteristics of
refrigerant-based nanofluid flow boiling inside a horizontal smooth tube, International
Journal of Refrigeration, Vol. 32, No. 6, pp. 1259-1270

Kim S. J., McKrell T., Buongiorno J., Hu L. W., 2010, Subcooled flow boiling heat
transfer of dilute alumina, zinc oxide, and diamond nanofluids at atmospheric pressure,
Nuclear Engineering and Design, Vol. 240, No. 5, pp. 1186-1194

Ahn H. S., Kim H. D., Jo H. J., Kang S. H., Chang W. P., Kim M. H., 2010, Experimental
study of critical heat flux enhancement during forced convective flow boiling of nanofluid
on a short heated surface, International Journal of Multiphase Flow, Vol. 36, No.
5, pp. 375-384

Park S. S., Kim Y. H., Jeon Y. H., Hyunx M. T., Kim N. J., 2015, Effects of spray-deposited
oxidized multi-wall carbon nanotubes and graphene on pool-boiling critical heat flux
enhancement, Journal of Industrial and Engineering Chemistry, Vol. 24, pp. 276-283

Park S. S., Kim W. J., Kim J. Y., Jeon Y. H., Kim N. J., 2015, A study on the influence
of boiling heat transfer of nanofluid with particle length and mixing ratio of carbon
nanotube, Korean Journal of Air-Conditioning and Refrigeration Engineering, Vol. 27,
No. 1, pp. 1-7

Kline S. J., McClintock F. A., 1953, Describing uncertainties in single-sample experiment,
Mechanical Engineer, Vol. 75, pp. 3-8

Zuber N., 1958, On stability of boiling heat transfer, ASME transactions, Vol. 80,
pp. 711-714

Katto Y., Kurata C., 1980, Critical heat flux of saturated convective boiling on uniformly
heated plates in a parallel flow, International Journal of Multiplhase Flow, Vol.
6, No. 6, pp. 575-582

Henderson K., Park Y, G., Liu L., Jacobi A. M., 2009, Flow-boiling heat transfer of
R-134a-based nanofluids in a horizontal tube, International Journal of Heat and Mass
Transfer, Vol. 53, No. 5/6, pp. 944-951

Sarafraz M. M., Hormozi F., Peyghambarzadeh S. M., 2015, Role of nanofluid fouling
on thermal performance of a thermosyphon:Are nanofluids reliable working fluid?, Applied
Thermal Engineering, Vol. 82, pp. 214-224

Park S. S., Kim Y. H., Jeon Y. H., Hyun M. T., Kim N. J., 2014, Effects of spray-deposited
oxidized multi-wall carbon nanotubes and graphene on pool-boiling critical heat flux
enhancement, Journal of Industrial and Engineering Chemistry
