Nae-Hyun Kim
(김내현)
1†
-
Division of Mechanical System Engineering, Incheon, 20012, Korea
(인천대학교 기계시스템공학부)
Copyright © 2016, Society of Air-Conditioning and Refrigeration Engineers of Korea
keywords
Structured tube, Heat transfer enhancement, Pool boiling, Three-dimensional roughness, R-134a
키워드
성형가공관, 열전달 촉진, 풀 비등, 삼차원 조도, R-134a
기호설명
A:전열 면적 [m2]
e:핀 높이 [m]
fpm:fins per meter
g:핀 사이 간격 [m]
h:열전달계수 [W/m2K]
M:분자량 [g/mole]
Pred:환산 압력
Q:전열량 [W]
q:열유속 [W/m2]
Rp:표면 거칠기 [m]
Tsat:포화 온도 [K]
Tw:벽면 온도 [K]
1. 서론
최근 국민소득의 향상과 더불어 중대형냉동기의 수요는 꾸준히 증가하고 있다.(1) 중대형 냉동기의 증발기는 만액식 쉘-튜브형 열교환기로 관 외측에서 냉매가 비등하며 관내를 흐르는 순환수를 냉각한다. Fig. 1에 중대형 냉동기의 증발기 개략도가 나타나 있다. 냉매로는 R-11이 주로 사용되어 왔으나 오존층 파괴 문제로 신 냉매인 R-134a로 대체되고 있다.
만액식 증발기에서 냉매는 증발기 하부로 약 15%의 건도로 유입하여 순환수와 열 교환을 한 후 포화 증기 상태로 압축기로 보내진다. 증발기 하부에는
분배판이 있어 냉매가 증발기 하부에 균일하게 분포되도록 한다. 냉매와 순환수의 열교환은 전열관을 통하여 이루어진다. 전열관으로는 그간 평활관이 사용되어
왔으나 최근 들어 비등 성능이 우수한 성형가공관이 많이 사용된다. 성형가공관은 추가 가공으로 인하여 평활관에 비하여 다소 비싸나 전열성능을 크게 증가시키므로
증발기를 작게 만들 수 있고 또한 작아진 증발 과열도로 인하여 전체 싸이클 효율을 높일 수 있으므로 평활관에 비하여 충분히 경제성이 있다.(2,3)
Fig. 1. Schematic diagram of the flooded evaporator.
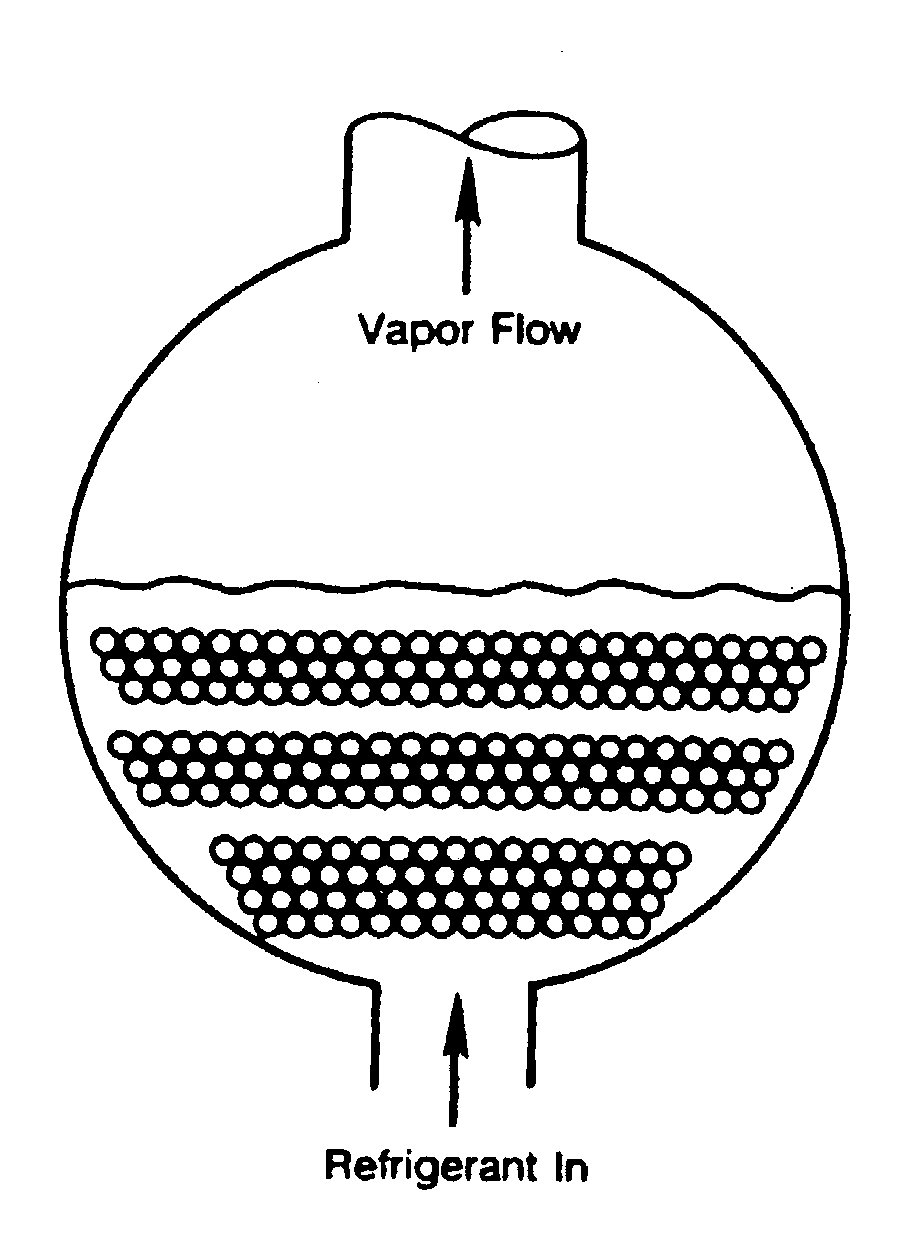
Fig. 2에는 해외에서 개발된 성형가공관의 표면이 나타나있다. 비등표면의 전열성능을 향상시키기 위해서는 기포를 안정되고 광범위하게 발생시키는 것이 필요한데
이를 위하여 비등표면에 인위적으로 미세공동을 형성한다. Fig. 2의 성형가공관들은 평활관을 성형 가공함으로써 비등 표면에 미세 공동을 형성한 관들이다.(3)
Fig. 2. Illustration of six commercially available enhanced boiling surfaces:(a) Low-fin tube (b) Trane bent fin (c) GEWA-TX (d) Thermoexcel-E (e) Turbo-B (f) GEWA-SE.
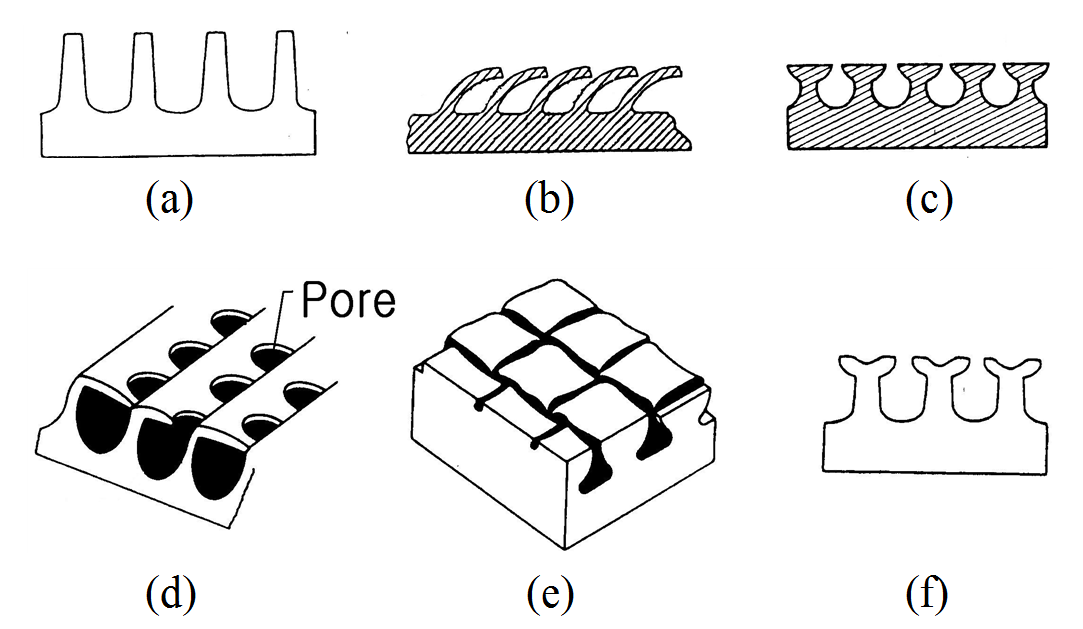
Fig. 2(a)는 낮은 핀관으로 평활관을 전조 가공하여 만든다. Fig. 2(b)는 Trane사의 bent fin 관이다. 핀 밀도 1,300 fpm의 낮은 핀관을 벤딩하여 재돌입(re-entrant) 형상을 만든다. Fig. 2(c)는 Wieland사의 Gewa-TX로 750 fpm의 핀 밀도를 가지고 있다. Fig. 2(d)는 Hitachi 사의 Thermoexel-E로 1,968 fpm의 낮은 핀관을 추가 가공하여 제작된다. Fig. 2(e)는 Wolverine 사의 Turbo-B로 1,650 fpm의 낮은 핀관으로부터 만들어진다. Fig. 2(f)는 Wieland사의 Gewa-SE로 1,024 fpm의 핀 밀도를 가지고 있다. 상기 성형가공관은 조도의 형상에 따라 이차원 조도관과 삼차원 조도관으로
나눌 수 있다. Fig. 2(a), Fig. 2(b), Fig. 2(c), Fig. 2(f)는 이차원 조도관이고 Fig. 2(d)와 Fig. 2(e)는 삼차원 조도관이다. 비등 열전달계수는 삼차원 조도관에서 크게 나타나고 이러한 경향은 낮은 열유속에서 두드러진다.(4,5)
삼차원 조도관의 비등 성능이 이차원 조도관보다 우수한 이유는 기포가 생성되는 하부 터널과 배출되는 유출부 형상의 차이 때문이다. 이차원 조도관에서는
이차원 하부 터널에서 생성된 기포가 이차원 슬릿을 통하여 배출되는데 반하여 삼차원 조도관에서는 삼차원 하부 터널에서 생성된 기포가 삼차원 기공(pore)을
통하여 배출된다. 삼차원 조도관 터널의 전열 면적은 이차원 조도관의 터널보다 크고 따라서 열전달계수는 증가하게 된다. 삼차원 조도관의 비등 성능에
대한 체계적인 연구는 Chien and Webb(6,7)에 의해 수행되었다. 그들은 Fig. 2(d) 형상의 성형가공관에 대하여 기공(pore) 직경, 기공 핏치, 하부 터널 형상이 비등 열전달에 미치는 영향을 R-11과 R-123을 사용하여 실험적으로
검토하였다. 비등 열전달계수는 이들 변수에 따라 현저히 다르게 나타났는데 열유속 범위에 따라 최적 형상(기공 직경, 기공 핏치)이 존재하였다. 낮은
열유속에서는 기공의 개도(기공 면적의 총합)가 작을수록 열전달계수가 크게 나타난 반면 높은 열유속에서는 기공의 개도가 클수록 열전달계수가 크게 나타났다.
낮은 열유속에서 기공의 개도가 너무 크면 하부 터널이 액체로 잠기게 되어 열전달계수가 감소하고 반대로 높은 열유속에서 기공의 개도가 너무 작으면 하부
터널로 액체의 공급이 원활하지 않아 열전달계수가 감소한다. Nakayama et al.(8,9)도 Thermoexel-E 형상의 비등 표면에서 동일한 경향을 보고한 바 있다. 이러한 열전달계수의 역전 현상은 이차원 조도관에서는 발생하지 않는데
예를 들어 Ayub and Bergles(10)는 물과 R-113을 이용한 실험에서 최적 형상 관의 열전달계수가 전 열유속에 걸쳐 다른 관들의 값보다 큼을 보고하였다. 이는 이차원 조도관의 경우
높은 열유속에서도 액체가 하부 터널로 무리 없이 공급되기 때문이다. 따라서 높은 열유속에서는 삼차원 조도관의 열전달계수와 이차원 조도관의 열전달계수가
근접하게 된다.(4,5)
삼차원 조도관에 대한 냉매의 비등 열전달에 대한 연구는 다음과 같다. Webb and Pais(4)는 5종류의 냉매 (R-11, R-12, R-22,
R-123, R-134a)를 사용하여 4종류의 성형가공관(낮은 핀관, Gewa-TW, Gewa-SE, Turbo-B)의 풀비등 성능을 실험하였다.
삼차원 조도관(Turbo-B)의 열전달계수는 이차원 조도관(Gewa-TX, 낮은 핀관)의 열전달계수보다 높게 나타났다. 또한 고압 냉매(R-12,
R22, R-134a)의 열전달계수는 저압냉매(R-11, R-123)의 값보다 크게 나타났다. Wang et al.(11)은 748 fpm의 낮은 핀관과 삼차원 조도관인 Gewa-B(Turbo-B와 유사한 형상, 1968 fpm)에 대하여 5종류(R-22, R-123,
R-134a, R- 410A, R-407C)의 냉매를 사용하여 풀비등 실험을 수행하였다. Gewa-B의 열전달계수는 낮은 핀관의 값보다 크게 나타났다.
혼합냉매인 R-407의 열전달계수는 R-22의 값보다는 낮고 R-410A의 값과 유사하게 나타났다. Kim and Choi(12)는 Fig. 2(d) 형상의 삼차원 조도관에 대하여 기공의 크기(0.2 mm, 0.23 mm, 0.27 mm)의 영향을 R-123과 R-134a를 사용하여 검토하였다.
최적 기공의 크기는 냉매에 따라 다르게 나타났는데 고압 냉매인 R-134a의 경우는 0.27 mm에서 저압 냉매인 R-123의 경우는 0.23 mm에서
최적값이 얻어졌다. Jung et al.(13)은 낮은 핀관(1024 fpm), Turbo-B, Thermoexel-E에 대하여 4종류의 냉매(R-22, R-134a, R-125, R-32)를
사용하여 풀비등 실험을 수행하였다. 열전달계수는 Thermoexel-E에서 가장 크게 나타났고 Turbo-B, 낮은 핀관 순이었다. 또한 열전달계수는
증기압이 가장 높은 R-32에서 가장 크게 나타났다. Yang and Fan(14)은 Turbo-B와 Gewa-TX에 대하여 R-134a와 R-404A를 사용하여 풀비등 실험을 수행하였다. Turbo-B의 열전달계수가 Gewa-
TX에 비하여 크고 R-404A의 열전달계수는 R-134a의 값 보다 크게 나타났다. Ribatski and Thome(15)는 Gewa-B와 Turbo-BII(Turbo-B의 개선품)의 R-134a 풀비등 성능을 비교하였는데 두 관의 성능은 대체로 유사하게 나타났다. Gorgy
and Eckels,(16) Chen(17)은 Turbo-BII의 R-134a, R-123 풀비등에 대한 추가 자료를 제시하였다.
Rooyen and Thome(18)는 Gewa-B5(Gewa-B의 개선품)와 Turbo-B5(Turbo-B의 개선품)에 대해 신 냉매인 R- 236fa와 R-1234ze(E) 그리고
R-134a를 사용하여 풀비등 실험을 수행하였다. R-1234ze(E)의 열전달계수는 R- 134a의 값과 유사하였으나 R-236fa의 열전달계수는
R- 134a보다 낮게 나타났다. Lee et al.(19)은 Turbo-B와 Thermoexel-E에 대해 신 냉매인 R-1234yf의 풀 비등 실험을 수행하고 R-134a와 비교하였다. Thermoexel-E의
열전달계수가 Turbo-B의 값보다 다소 높게 나타났다. 한편 R-1234yf의 열전달계수는 R-134a와 유사하였다. Tarrad and Burnside,(20) Mertz et al.,(21) Chen et al.(22)은 성형가공관에서 탄화수소 냉매의 풀비등 촉진에 대해 연구하였다.
성형가공관의 풀 비등 열전달계수에는 핀 밀도, 기공 직경, 기공 핏치등 여러 인자가 영향을 미친다. 상기 문헌 조사 결과 대부분의 연구는 상용 성형가공관에
대해 수행되었고 상기 인자들이 비등 열전달에 영향에 대해서는 아직 자료가 부족함을 알 수 있다. 본 연구에서는 핀 밀도, 핀 높이, 핀 사이 간격이
다른 5종류의 Fig. 2(e) 형상의 삼차원 조도관에 대해 R-134a 풀비등 실험을 수행하였다. 또한 그 결과를 기존 상용 성형가공관의 값과 비교하였다.
2. 성형가공관
Fig. 3에 본 연구의 삼차원 조도 성형가공관의 확대 및 단면 사진을 나타내었다. table 1에는 성형가공관의 제원이 나타나 있다. 성형가공관은 낮은 핀관의 상부를 축 방향으로 커팅한 후 롤러로 눌러 제조된다. 롤러로 누르는 강도에 따라 미세
기공의 크기와 핀 높이가 달라진다. 본 연구에서 검토된 5종류의 상형가공관은 핀 밀도 1075 fpm에서 2047 fpm, 핀 높이 0.58 mm에서
0.84 mm범위를 가지고 있다.
Fig. 3. Structured enhanced tubes of the present study.
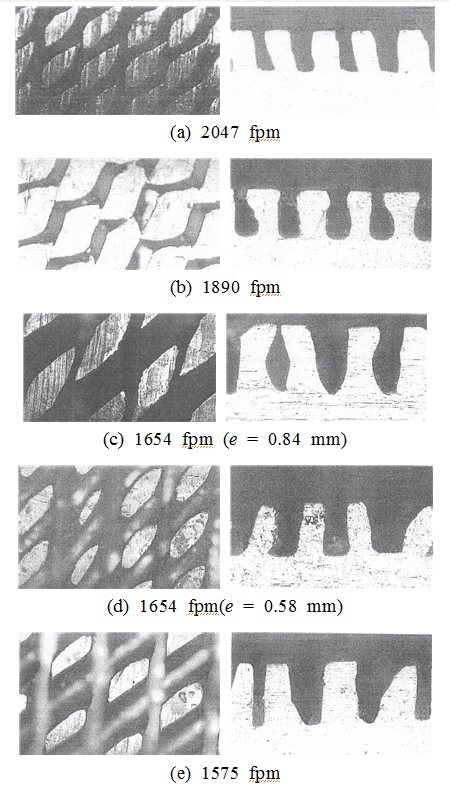
Table 1. Geometric details of the enhanced tubes
Tube
|
fpm
|
Fin height e (mm)
|
Fin gap width g (mm)
|
(a)
|
2047
|
0.59
|
0.21
|
(b)
|
1890
|
0.64
|
0.17
|
(c)
|
1654
|
0.84
|
0.37
|
(d)
|
1654
|
0.58
|
0.34
|
(e)
|
1575
|
0.68
|
0.36
|
3. 실험장치 및 방법
3.1 실험장치
Fig. 4에 실험장치의 개략도를 나타내었다. 시험부는 직경 150 mm, 길이 350 mm의 동관으로 제작되어 일단에는 시험전열관이 장착되고 다른 단에는 관측창을
설치하여 비등현상을 관측하고 수위를 계측할 수 있도록 하였다. 시험부에서 증발한 증기는 상부에 위치한 응축기에서 응축된 후 시험부 하부로 되돌아온다.
응축기는 쉘-튜브형 열교환기로 관 내측에는 3 RT급 항온수조로부터 공급되는 브라인이 흐르며 관 외측의 냉매증기를 응축시킨다. 실험은 터보냉동기용
증발기의 작동온도인 포화온도 4.4℃에서 수행되었다.
Fig. 4. Schematic drawing of the test apparatus.
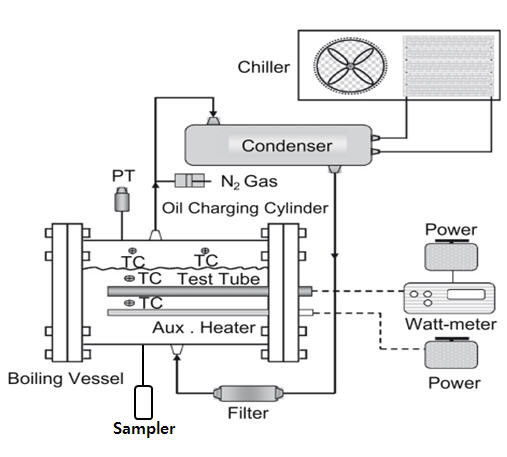
시험 전열관의 상세도가 Fig. 5에 보여진다. 전열관의 비등성능을 알기 위해서는 관벽 온도를 측정하여야 한다. 관벽온도는 일반적으로 관벽에 열전대를 심고 이로부터 측정된 온도를 외삽하여
구한다. 하지만 실제 성형가공관의 경우는 관벽 두께가 얇고 관 내측에 조도가 형성되어 있기 때문에 열전대를 장착할 수 없다. 본 연구에서는 전열관
내측을 드릴링하여 평활 표면으로 만들고 환형 동봉을 전열관 내측에 끼워 맞춤하여 열전대를 설치하였다. 환형 동봉 외측에는 은납을 코팅하고, 끼워 맞춤
후 은납을 녹여 두 관의 접촉을 강화하였다. 시험 후 전열관을 커팅하여 접촉 상태를 확인한 결과 만족할 만 하였다. 시험 전열관의 내측에는 외경 13.45
mm의 히터를 장착하였다. 히터는 발열부가 시험 전열관과 길이와 일치하도록 특별 제작하였다. 히터 삽입시 전열관과 히터 사이에는 thermal epoxy를
발라 열전달이 원활히 이루어지도록 하였다. 또한 시험 전열관의 앞 뒤는 테프론 마개와 링으로 측부 열손실을 최소화하였다. 열전대 구멍은 시험부 상부로부터
1.3 mm 떨어진 지점에 직경 1.0 mm, 깊이 85 mm로 상하좌우 네 곳에 가공되었다. 구멍에 열전대를 삽입할 때는 열전대를 thermal
epoxy에 충분히 묻힌 후 삽입하여 열전대와 구멍 사이에 빈 공간이 없도록 하였다. 냉매 액의 온도와 증기온도는 각각 두 곳씩 네 곳에서 측정하였다.
액의 온도는 전열관 상하 각각 20 mm 떨어진 곳에서, 증기온도는 시험부 상부에서 측정되었는데 시험 중 이 네 온도는 0.2℃ 이내에서 일치하였다.
또한 압력 트랜스듀서로 측정된 압력으로부터 환산된 포화온도와 비교하였을 때 이들은 0.3℃ 이내에서 일치하였다. 온도 측정은 직경 0.13 mm의
가는 Cu-Co 열전대로 이루어졌다.
Fig. 5. Detailed sketch of the test tube.
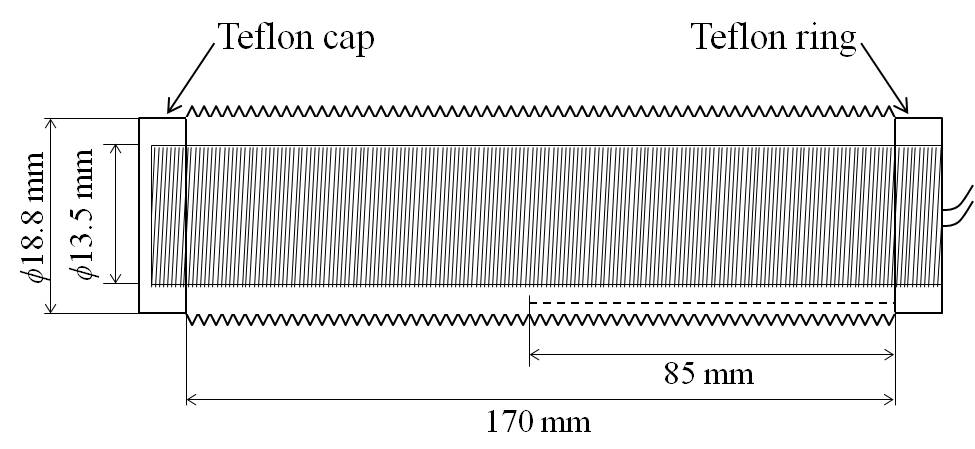
3.2 실험방법
비등 현상은 전열 표면의 상태에 매우 민감하게 반응하므로 매 실험시 표면의 상태를 일정하게 유지하는 것이 중요하다. 본 연구에서는 Bergles
and Chyu(23)가 제안한 방법을 따랐다. 우선 시험 전열관을 최대 열유속(약 50 kW/m2)에서 한 시간 가량을 비등시켜 전열관과 액 중의 잔류가스를 제거한 후 열유속을 천천히 0 kW/m2까지 감소시킨다. 다음 30분간 냉동기를 가동시켜 포화온도를 4.4℃로 유지시킨다. 그 후 시험 전열관의 열유속을 천천히 증가시켜 최대 열유속까지
증가시킨다. 최대 열유속에서 정상상태가 되면 벽면 온도와 포화액, 포화증기온도 그리고 포화압력을 측정한다. 이 후 열유속을 감소시켜가며 온도와 압력을
측정한다. 열유속을 변화시킨 후 정상상태까지는 대략 5분 정도 소요되었다. 시험 중 액의 수위는 전열관 상부 5 cm를 유지하도록 하였다. 시험 전열관은
시험 전 아세톤으로 깨끗이 닦은 후 실험에 임하였다. 본 실험에서 시험 전열관의 관 벽 온도는 관 내벽에 심은 4곳의 열전대로부터 측정된 온도를 외삽
하여 구하였다. 관 벽 온도를 정확하게 알기 위해서는 가능한 한 많은 곳에서 온도를 측정하면 좋지만, 이 경우 열전대 구멍을 너무 많이 가공하면 관의
열전도에 영향을 미치므로 일반적으로 서너 군데에서 측정한다. 관 벽 온도 측정 시 한 가지 유의해야 할 사항은 관의 길이 방향으로의 온도 변화이다.
관 양단에서는 측부 열손실에 따라 관 벽 온도가 다소 내려갈 수 있다. 이를 확인하기 위하여 열전대 위치를 길이 방향으로 변화시키며 온도 변화를 측정하였는데
열전대의 위치가 열전달계수에 미치는 영향은 6% 이내로 무시할 만 하였다. 따라서 본 연구에서는 열전대를 관의 중심부에 위치하고 온도를 측정하였다.
본 실험에서 열전달계수는 다음 식으로 정의된다.
여기서 Tw는 관 벽 온도를 평균 낸 값이고 Tsat은 포화액과 증기의 온도를 평균 낸 값이다. 열전달 면적 A는 전열관의 최외각직경 D로 정의되는 공칭면적(A = πDL)을 사용하였다. 실험의 오차해석을
Kline and Mclintock(24)의 방법에 따라 수행하였다. 열전달계수의 오차는 열유속 40 kW/m2에서 ±3.2%, 10 kW/m2에서 ±7.4%가 되었다.
4. 실험결과 및 고찰
4.1 평활관
실험의 신뢰도를 확인하고 성형가공관과의 비교를 위하여 평활관에 대한 실험을 수행하였다. 평활관의 경우 표면을 가는 사포(입도 1,000)로 갈아
일정한 표면 거칠기가 되도록 하였다. 일반적으로 구리관의 표면은 검붉은 색을 띄고 있는데 이는 표면이 공기 중의 산소와 반응하여 산화막을 형성하기
때문이다. 이 표면을 사포로 갈아내면 반짝이는 구리 표면이 되는데, 이 경우 비등성능은 산화막이 형성된 후의 비등성능과 다를 수 있다.(25) 본 연구에서는 산화막의 영향을 살펴보기 위하여 사포질한 평활관에 대하여 반복 실험을 수행하였는데 시간이 갈수록 비등성능이 감소하다 수 일 후에야
일정한 값을 유지하는 것을 확인하였다. 본 연구에서는 비등표면을 충분히 산화시킨 후 실험에 임하였다.
Fig. 6에 포화온도 4.4℃에서 평활관의 비등성능이 나타나있다. 또한 실험자료를 Cooper(26)의 상관식과 비교하였다. 이 그림은 Cooper 상관식이 실험결과를 적절히 예측하는 것을 보여준다. Cooper의 상관식은 다음과 같다.
Fig. 6. Smooth tube heat transfer coefficients compared with those by Cooper(25)correlation.
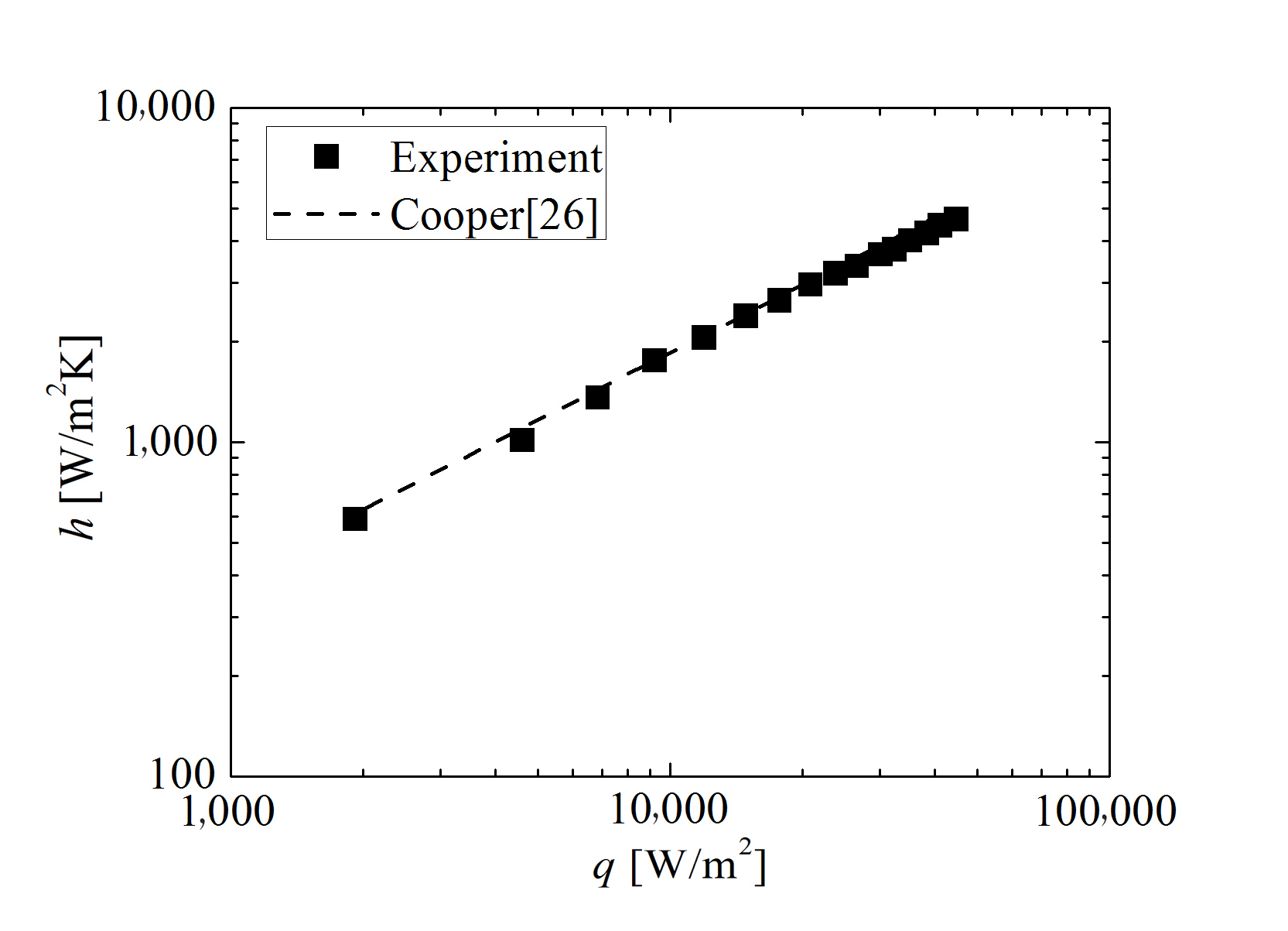
여기서 m = 0.12 - 0.2 log10Rρ이며 Rρ = 0.3 μm를 사용하였다.
4.2 성형가공관
Fig. 7에 성형가공관의 열전달계수를 나타내었다. 실험은 포화온도 4.4℃에서 수행되었다. 이 그림은 2,047 fpm 전열관의 열전달계수가 가장 큼을 보여준다.
그 이유는 핀 밀도와 미세 공동의 형상 때문으로 판단된다. 2047 fpm 전열관의 핀 밀도는 5종의 전열관 중 가장 크다. 핀 밀도가 증가하면 이에
비례하여 미세 기공의 개수도 증가하게 된다. 또한 Fig. 3(a)는 2,047 fpm 전열관에 핀 사이 간격 0.21 mm인 미세 기공이 잘 형성되어 있음을 보여준다. 두 번째로 큰 열전달계수는 1,890 fpm
전열관에서 얻어졌다. 이 관의 핀 밀도는 5종의 전열관 중 두 번째로 크다. Fig. 7은 1,890 fpm 전열관의 열전달계수 증가율이 높은 열유속에서 현저히 감소함을 보여준다. 이는 미세 기공의 크기가 작은 경우에 나타나는 현상이다.(5,6) 성형가공관에서 증기는 미세 기공 하부의 터널에서 액막의 증발에 의해 형성되고 이 증기는 미세 공동을 통해 기포 형태로 배출된다.(8,9) 미세 기공의 크기가 너무 작으면 증기의 배출이 원활치 않아 터널에 드라이 아웃이 생겨 열전달계수가 감소한다. 반대로 미세 기공의 크기가 너무 크면
터널에 액체의 공급이 너무 많아 열전달계수가 감소된다.(6,7) 따라서 최적의 미세 기공 크기가 존재하게 된다. table 1에 나타나 있듯이 1,890 fpm 전열관의 핀 사이 간격은 0.17 mm로 5종의 전열관 중 가장 작다. Kim and Choi(12)는 삼차원 조도를 가진 성형가공관에 대한 일련의 시험을 통하여 최적 핀 사이 간격은 냉매의 종류에 따라 다르고 R-134a의 경우 0.1 mm임을
보고하였다. 이 값은 본 연구 성형가공관의 핀 사이 간격(0.17 mm~0.37 mm) 보다 작다.
Fig. 7. Heat transfer coefficients of the structured enhanced tubes.
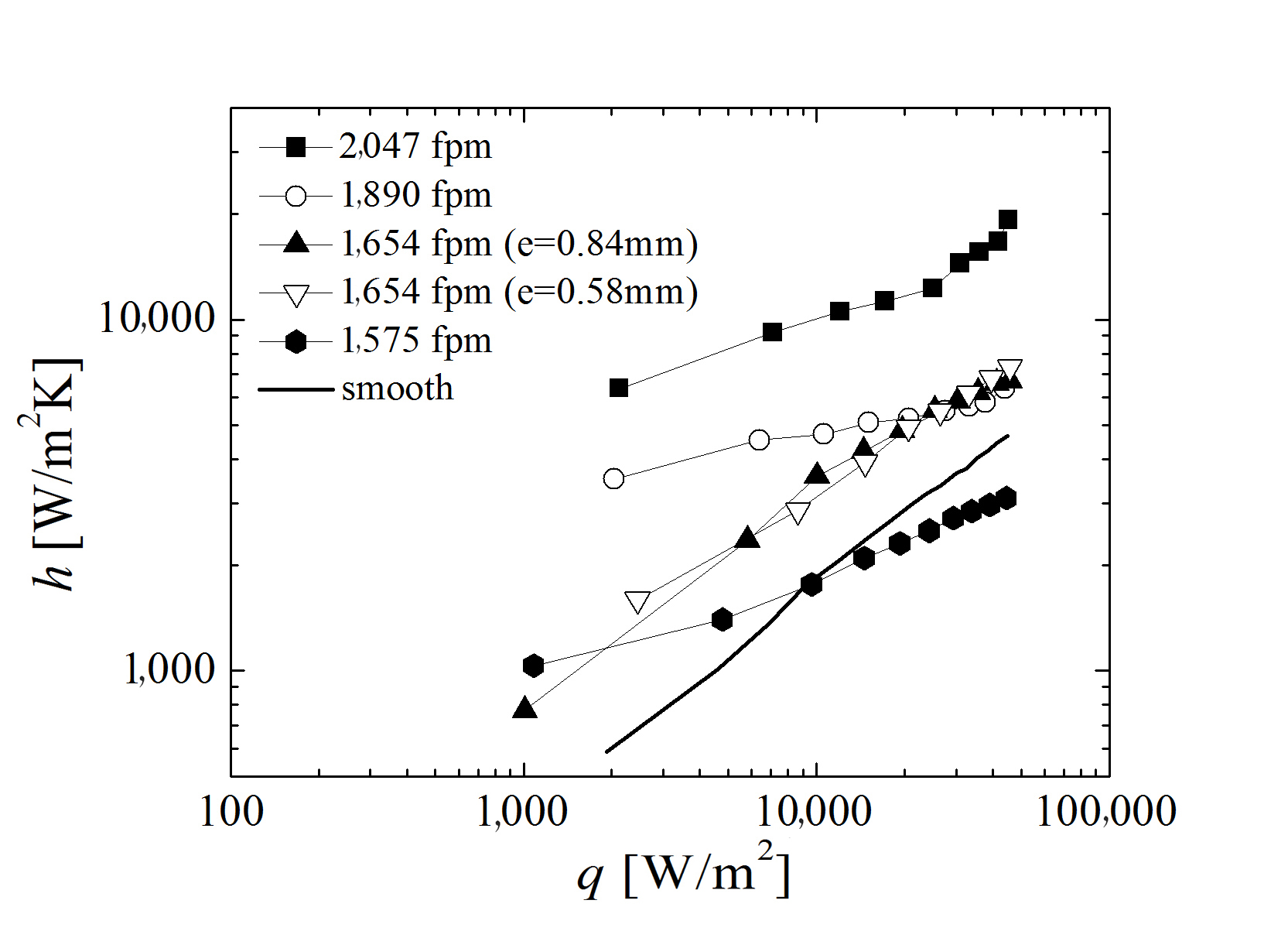
1575 fpm 전열관의 열전달계수는 5종류의 전열관 중 가장 낮게 나타났다. 이는 1,575 fpm 전열관의 핀 밀도가 가장 작고 미세공동의 크기도
0.36 mm로 상대적으로 커 기포 형성이 원활하지 않기 때문이다. 특히 높은 열유속에서는 평활관보다도 열전달계수가 작게 나타났다. 이는 높은 열유속에서
기포 이탈이 원활하지 않기 때문으로 유추되는데 그 원인은 명확치 않다. 1654 fpm 전열관 두 종류에서 핀 사이 간격은 0.37 mm와 0.34
mm로 유사하고 핀 높이는 0.58 mm와 0.84 mm로 서로 다르다. Fig. 7은 두 전열관의 열전달계수가 유사함을 보여준다. 이로부터 핀 높이가 삼차원 조도관의 풀비등 성능에 미치는 영향은 미미함을 유추할 수 있다. 열유속
10 kW/m2에서 2,047 fpm 전열관의 열전달계수는 평활관보다 5.5배 크고 1,890 fpm 전열관은 2.6배, 1,654 fpm 두 종류
전열관은 2.0배와 1.7배, 1,575 fpm 전열관의 열전달계수는 평활관의 값과 유사하다.
Fig. 8에 본 연구의 최적 성형가공관의 열전달계수와 기존 상용 성형가공관의 열전달계수를 비교하였다. 이 그림은 본 성형가공관의 열전달계수가 Thermoexel-E,
Gewa-B보다는 작고 Turbo-B, Gewa-SE와 유사함을 보여준다. Thermoexel-E와 GEWA-B의 핀 밀도는 1,968 fpm이고
Turbo-B는 1,650 fpm, GEWA-SE는 1,024 fpm이다. 본 연구의 성형가공관은 핀 밀도가 2047 fpm로 Thermoexel-E,
GEWA-B보다 다소 큼에도 불구하고 열전달계수는 작다. 이는 본 연구 성형가공관의 핀 사이 간격이 최적화되지 않았기 때문으로 판단된다. 본 연구
성형 가공관의 핀 사이 간격은 0.21 mm로 Kim and Choi(12)가 제시한 1.0 mm보다는 상당히 크다.
Fig. 8. Heat Transfer coefficients of the 2047 fpm tube compared with those of commercial enhanced tubes.
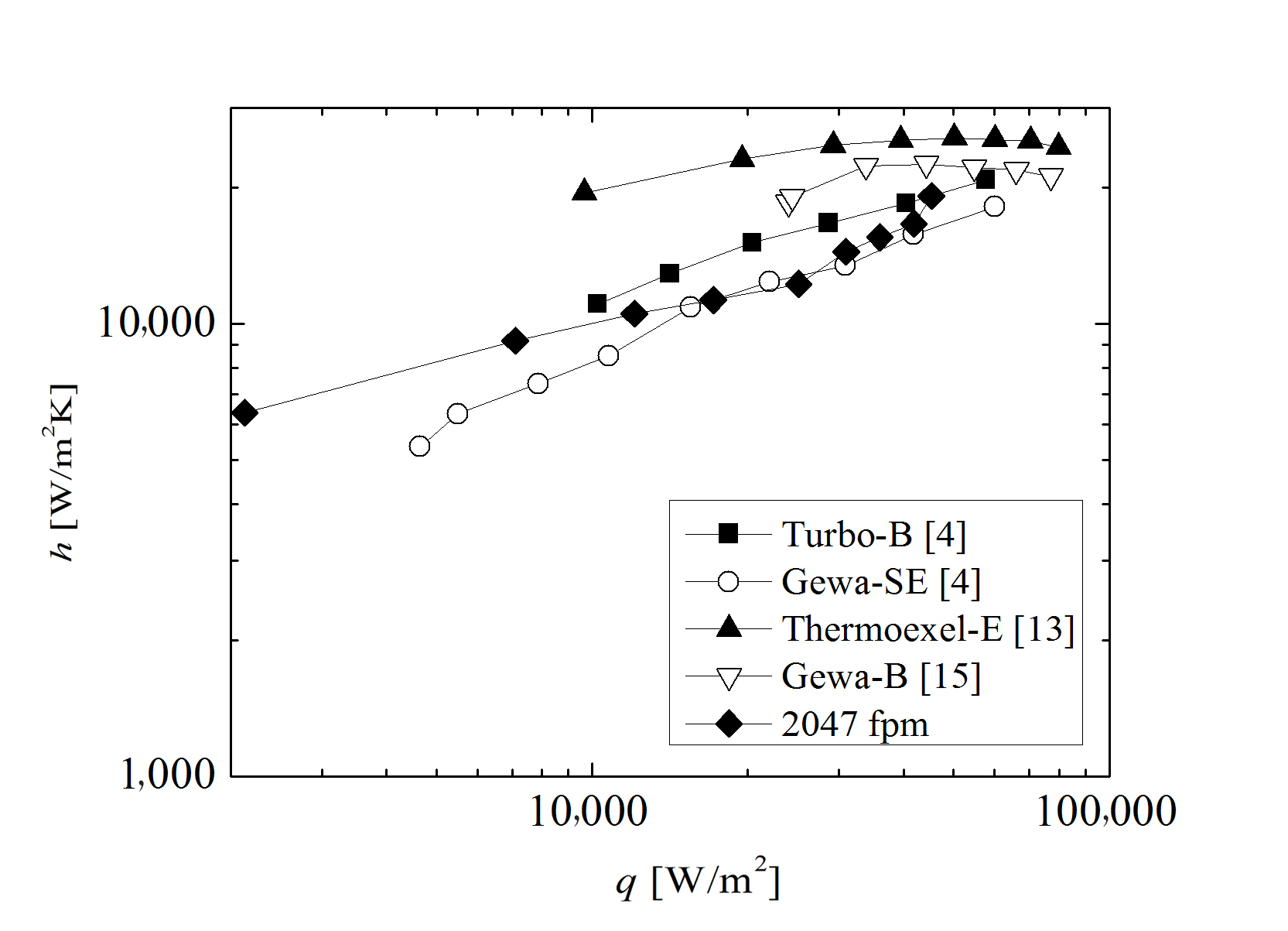
5. 결 론
본 연구에서는 핀 밀도, 핀 높이, 핀 사이 간격이 다른 5종류의 삼차원 조도관에 대해 R-134a 풀비등 실험을 수행하였다. 주된 내용은 다음과
같다.
(1) 열전달계수는 핀 밀도가 증가할수록 증가하였다. 이는 핀 밀도의 증가에 따라 미세 기공의 개수도 증가하기 때문이다.
(2) 본 연구의 범위에서 핀 높이가 열전달계수에 미치는 영향은 크지 않다.
(3) 최적 성형가공관(2,047 fpm)의 열전달계수는 기존 상용 성형가공관의 값보다 작게 나타났다. 이는 본 연구 성형가공관의 핀 사이 간격이
최적화되지 않았기 때문으로 판단된다.