Yeonho Sim
(심연호)
1
Jisu Kang
(강지수)
1
Siye Byun
(변시예)
1
Young Soo Chang
(장영수)
2
Byung Ha Kang
(강병하)
2†
-
Department of Mechanical Engineering, Graduate School of Kookmin University, Seoul,
02707, Korea
(국민대학교 대학원 기계공학과)
-
College of Engineering, Kookmin University, Seoul, 02707, Korea
(국민대학교 공과대학)
Copyright © 2016, Society of Air-Conditioning and Refrigeration Engineers of Korea
keywords
Low temperature vacuum drying, Poly γ glutamic acid, Desiccant, Sorption capacity, Diffusivity
키워드
저온진공건조, 폴리감마글루탐산, 제습제, 흡습량, 확산계수
기호설명
a:구형 제습제 반지름 [m]
C:수증기 농도 [kg/m3]
D:확산계수 [m2/s]
M:흡습량 [g]
P:압력 [kPa]
R:기체상수 [kJ/kg K]
T:온도 [K]
V:체적 [m3]
하첨자
h.p:열판
ini:초기
s:시료표면
sorp:흡습챔버
∞:포화
1. 서론
건조공정은 식품, 화학, 제약, 화장품 산업에서 많이 사용되고 있으며 방식에 따라 건조시간, 비용, 건조물의 성질에 많은 차이가 발생한다. 가장
많이 사용되고 있는 열풍건조의 경우, 히터로 가열된 열풍이 직접적으로 건조물과 접촉하여 수분을 증발시키는 방식이다. 건조시간이 빠르다는 장점이 있지만,
고온으로 인한 제품의 변성이 일어날 우려가 크고, 증발된 수분에 의해 습도가 높아진 열풍을 배기해야 하므로 에너지 손실이 크다는 단점이 있다.(1)
동결건조는 첨단 건조방법의 하나로 시료를 동결시킨 후, 승화에 의해 건조시키는 방법이다. 승화 및 진공 조건에서 건조가 수행되기 때문에 열에 의한
분해나 변질이 없고 오염물질이 유입될 우려가 없기 때문에 가장 고품질의 건조물을 얻을 수 있는 방법이다. 생물학적인 요소의 손상 없이 건조물을 획득할
수 있기 때문에 고품질의 제품이 요구되는 의약분야, 화학분야, 식품분야에 사용되고 있다.(2) 그러나 고가의 설비, 높은 운전비용, 건조시간이 길기 때문에 생산효율이 낮고 에너지 소비가 높다는 단점이 있어서 고부가가치의 제품이 아닌 경우 적용하기
어렵다.(3) 이와 같은 건조방법의 단점을 극복하기 위한 방법으로 상압에서 건조를 진행하는 저온건조와 진공조건에서 건조를 수행하는 저온진공건조 방법이 있다.
저온 건조의 경우 상압에서 저온의 조건으로 건조를 수행하기 때문에 열풍건조의 단점인 제품의 변성을 줄일 수 있지만, 건조시간이 오래 걸린다는 단점이
있다. 이와 같은 단점을 해결하기 위한 방법으로 많은 분야에서 제습제의 흡착 및 흡습 특성을 이용하여 건조시스템에 적용하는 연구가 수행되고 있다.
Djaeni et al.(4)는 저온건조 시스템에 다단흡착드라이어를 적용하여 기존의 응축기를 사용한 저온건조와 비교하여 에너지 효율에 대한 연구를 수행하였다. Gurtas et
al.(5)은 버섯건조를 위한 저온건조 공정에 제습제를 적용하였고, 건조를 통한 건조품질 및 제습제의 확산계수를 측정하는 연구를 수행하였다. Sosle et
al.(6)는 히트펌프를 이용하여 제습 통합 건조 시스템을 구축하여 실험을 수행하였다. 실험을 통해 히트펌프건조시스템의 농식품 건조에 대한 가능성을 평가하였고
동시에 히트펌프를 이용한 공간 제습 및 온수 이용이 가능한 시스템을 구축하였다.
저온건조의 건조시간 단축 및 향상된 품질의 건조물을 얻기 위한 방법으로 상압의 아닌 진공조건을 적용하는 저온진공건조 방식이 있다. 저온진공건조는
진공 조건에서 일정한 저온의 온도에서 증발을 이용한 건조방법이다. 건조가 이루어지는 건조챔버와 증발된 수증기가 포집되는 콜드트랩 사이의 수증기 압력
차이에 의해 건조하는 방식이다. 저온 진공 건조의 경우 열풍건조의 단점인 높은 온도에 의한 제품 변성을 막고 진공조건에서 공정이 진행되기 때문에 오염물질의
유입을 막을 수 있고 긴 건조시간을 보완할 수 있다.
동결건조와 같이 진공의 조건에서 건조를 수행하지만 동결건조 같이 동결 후 건조하는 방식이 아니므로 동결건조 만큼의 고품질의 건조물을 얻을 수는 없지만,
건조시간과 운전비용을 줄일 수 있다는 장점이 있다.(7) 이와 같은 장점을 극대화시키기 위한 방법으로 제습제를 저온진공건조 시스템에 적용하기 위한 기존 연구를 수행하였다.
본 논문에서는 저온진공건조 시스템에 제습제를 적용하는 연구를 수행하였다. 제습제적용을 위해 저온에서 제습제 성능평가를 수행하였고, 이를 저온진공건조
장치의 콜드트랩 부에 적용하여 제습제 유/무에 따른 저온진공건조의 건조시간에 미치는 영향에 대해 분석하였다.
2. 제습제 성능평가
2.1 흡습량 및 확산계수 모델링
저온진공건조의 콜드트랩에 적용할 제습제 성능평가 실험의 제습제는 저노점 조건에서 우수한 성능을 나타내는 실리카겔(Silica-gel), 활성알루미나(Activated
alumina)와 흡습특성이 우수한 폴리머 제습제(SDP)(8)로 선정하였다. table 1은 실험에 사용된 실리카겔과 활성알루미나의 물성치를 나타내고 있다.
Table 1. Desiccant properties in this study
|
Surface area
|
Total pore volume
|
Packed bulk density
|
Diameter
|
(m2/g)
|
(ml/g)
|
(kg/m3)
|
(mm)
|
Silica-gel
|
810
|
0.45
|
790
|
1~2
|
Activated alumina
|
360
|
0.5
|
769
|
3~4
|
제습제의 성능 특성에 관한 연구로서, Maria et al.(9)는 활성알루미나를 이용하여 흡착 스티렌 건조에 대한 모델링 및 흡착 과정에 대한 실험적 결과를 예측하기 위한 수학적 모델을 개발하였다. Gurgel
et al.(10)은 적외선 검출을 이용한 시료 표면온도를 측정하여 실리카겔에 대한 물의 질량 확산율 및 실리카겔의 유효 열전달율에 대한 연구를 수행하였다. Lee
et al.(8)은 SDP라는 새로운 폴리머 제습제를 제시하였고, SDP의 상대습도에 따른 흡습량 및 확산계수에 대해 실험적 연구 및 모델링을 수행하였다. 이와 같은
기존의 연구를 참고하여 본 연구에 사용된 제습제에 대한 흡습량과 확산계수를 측정하였다. 흡습량은 제습제가 수분을 흡착하는 양을 나타내고, 확산계수는
제습제 내부로 수분이 흡착되는 속도를 나타낸다.
진공조건에서 제습제가 들어있는 일정한 크기의 흡습챔버에 일정량의 수증기를 공급한 후, 흡습이 진행됨에 따른 챔버 내부의 압력변화 데이터를 측정하여
식(1)에 의해 흡습량의 변화를 계산하였다.
충분한 시간이 지난 후, 챔버 내부의 압력변화가 나타나지 않으면, 제습제의 흡습이 완료되고 최대 흡습량에 도달하였다고 간주하였다. 이 때, 최종
수증기압으로 부터 식(1)을 이용하여 최대 흡습량을 측정하였다.
제습제의 흡습량의 변화를 픽의 법칙(Fick’s law)의 수학적 모델을 통한 실험적 해석을 수행하여 확산계를 측정하였다.
폴리머 제습제의 경우 부직포에 코팅된 형태를 사용하였기 때문에 두께(δ)를 가진 평판형 해석모델을 사용하였으며 물질전달 방정식은 식(2)와 같다.
실리카겔과 활성알루미나의 경우 구형 형태의 입자로 가정하고 식(3)의 지배 방정식을 이용하여 해석을 수행하였다. 해석을 위한 제습제의 흡습과정 개략도를 Fig. 1에 나타내었다.
Fig. 1. Schematic diagram of moisture sorption process.
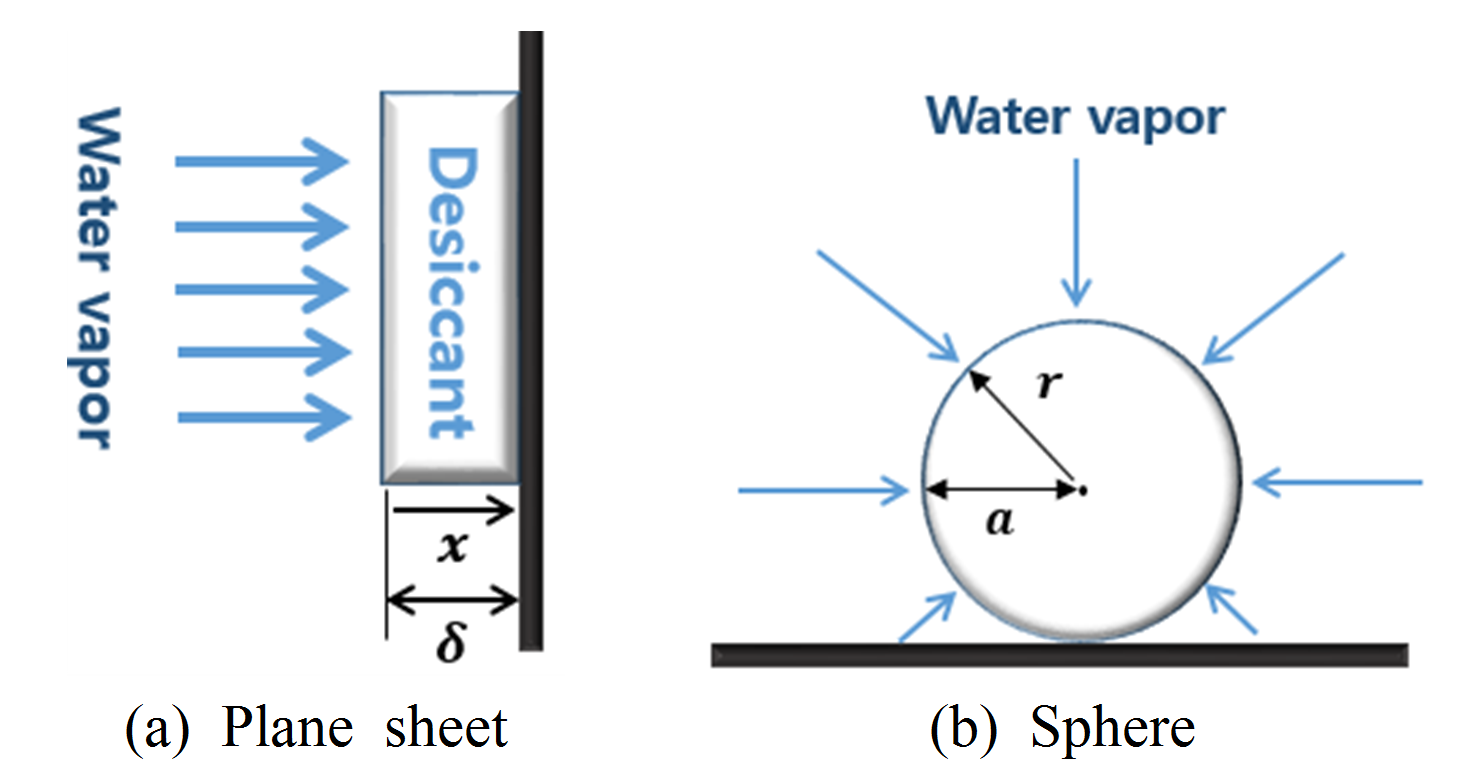
제습제의 초기 농도는 충분한 재생과정을 가정하여 ‘0’으로 설정하였고, 수증기와 제습제가 접촉하는 면의 농도는 일정하게 유지되고 있다고 가정하였다.
따라서 초기조건과 경계조건으로 평판형의 경우 식(4)~식(6)와 같고, 구형의 경우 식(7)~식(9)를 사용하였다.
실험 데이터와 비교 분석을 수행하기 위해 시간에 따른 농도변화에 대한 해석해를, 제습제 내부의 공간 적분을 수행하여 흡습량 변화에 대한 식으로 변환하였다.
평판형의 경우 Lee et al.(8)의 연구결과를 활용하여 식(10)에 나타내었고, 구형의 경우, Carslaw et al.(11)를 참조하여 흡습량에 대한 식으로 변환하여 식(11)에 나타내었다.
실험결과를 이용하여 식(10)과 식(11)의 확산계수를 도출해 내기 위해 고차항들을 생략하고 자연로그형태로 만들어 시간에 대한 선형식으로 표현하면 각각 식(12)와 식(13)과 같다.
식(1)에 의해 실험으로 구한 흡습량의 변화를 식(12), 식(13)에 적용하여, 선형피팅을 통해 확산계수를 도출하였다.
2.2 실험 장치 및 방법
제습제 성능평가 실험 장치의 개략도를 Fig. 2에 나타내었다. 실험장치는 충전챔버(Charging chamber), 흡습챔버(Sorption chamber), 진공펌프(Vacuum pump)로
구성되어 있다. 두 챔버의 온도 조절을 위해 항온조 내에 흡습챔버와 충전챔버를 설치하고 열선을 감았다. 진공조건은 안정적인 고진공 조건을 유지하기
위해 회전펌프(Rotary pump)와 확산펌프(Diffusion pump)를 연결하여 사용하였다. 두 챔버의 온도 변화를 측정하기 위해 온도센서(Range
of -250~350℃, accuracy of ±0.5℃)를 설치하였고, 흡습챔버의 압력변화를 측정하기 위해 압력센서(Range of 5×10-9~750 Torr, accuracy of ±5%)를 설치하였다.
Fig. 2. Schematic diagram of the desiccant performance evaluation experimental equipment.
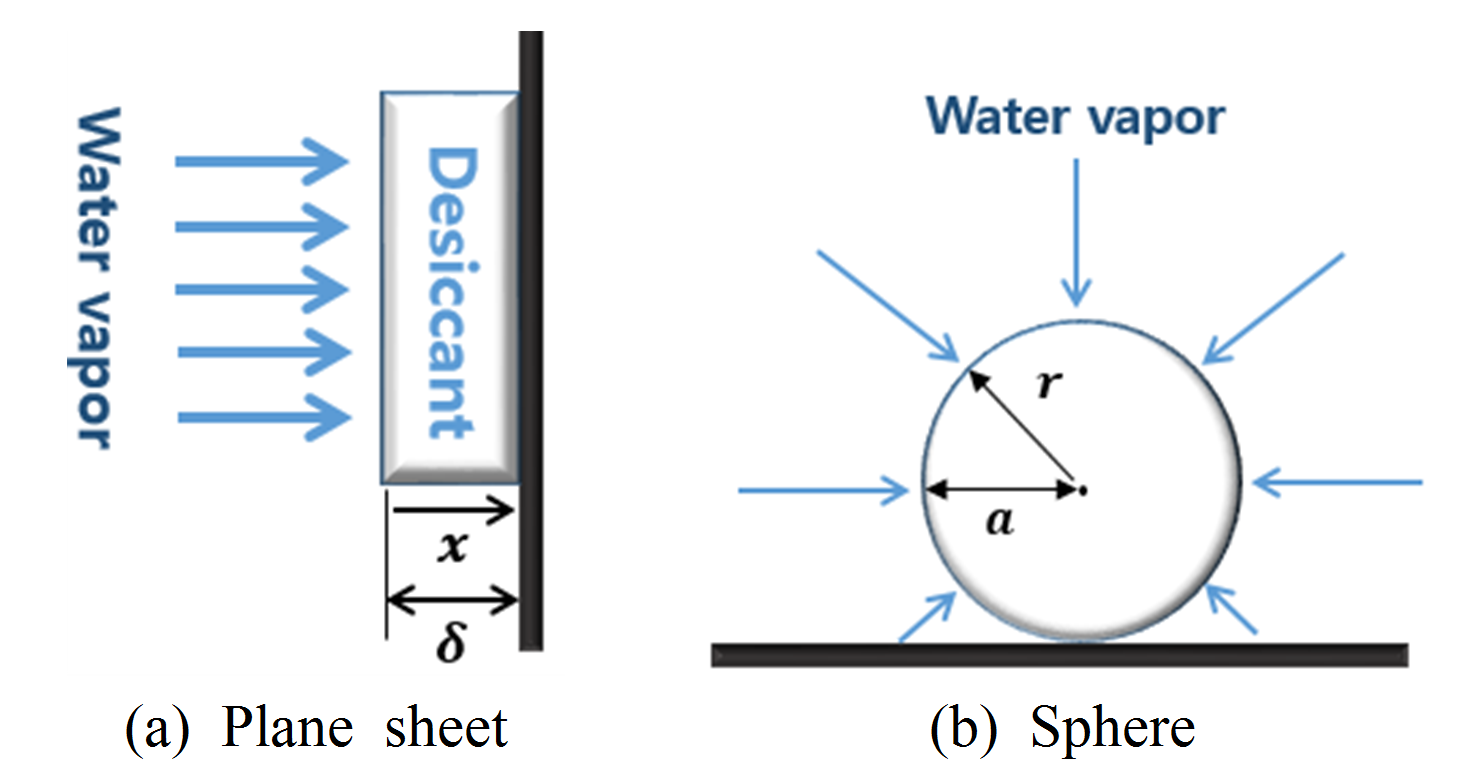
최대 흡습량은 제습제의 온도와 주위의 수증기압에 따라 변하게 된다. 따라서 흡습챔버 내부의 온도와 수증기압(노점온도)을 변화시켜 실험을 수행하였으며,
실험조건은 table 2 와 같다.
Table 2. Experimental conditions
Desiccant temperature(℃)
|
Charging chamber temperature(℃)
|
10
|
-10.5
|
-2.6
|
2.7
|
0
|
-18.0
|
-10.5
|
-6.0
|
-10
|
-27.4
|
-19.8
|
-15.4
|
실험 전 오븐을 이용하여 제습제를 충분히 건조한 후, 흡습챔버에 넣어준다. 그리고 항온조와 열선을 이용하여 실험조건에 해당하는 제습제 온도를 유지한다.
충전챔버의 온도는 흡습챔버의 초기수증기압을 결정하므로, table 2의 노점온도로 설정한다. 진공펌프를 이용하여 초기진공도 1 × 10-3 Torr 이하로 배기한다. 충전챔버 내로 증류수를 주입하고, 안정화 이후 충전챔버의 수증기를 흡습챔버로 공급한 후, 충전챔버와 흡습챔버를 밸브를
이용하여 차단한다. 흡습챔버에서 제습제의 수증기 흡습에 따른 압력변화를 측정한다.
실험에 사용된 실리카겔의 열확산계수는 2.55×10-6 m2/s이고, 실험에서 측정한 확산계수는 3×10-8 m2/s 정도이다. 제습제 내부의 열전달속도가 물질전달속도에 비해 100배 정도 빠르다는 것을 의미하므로, 제습제 내의 온도구배를 무시할 수 있다. 수분의
흡착은 초기에 가장 빠르게 일어나며, 흡착열도 가장 많이 발생하게 된다. 발생한 흡착열은 제습제 하부의 트레이로 전달되게 되는데, 실험 초기 제습제의
온도가 약 1℃ 정도 상승하는 것으로 예측되며, Fig. 4의 결과에서 확인할 수 있는 바와 같이 초기 제습제의 온도 상승에 의한 확산계수의 측정오차는 미미한 것으로 판단된다.
Fig. 4. Effect of dew point temperature on diffusivity for various sorption temperature.
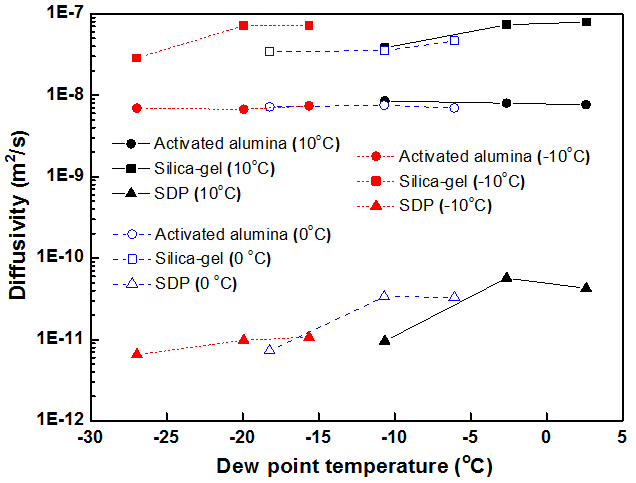
2.3 제습제 성능평가 실험 결과 및 고찰
제습제의 세 가지의 온도조건에 따라 포화수증기압에 해당하는 노점온도에 따른 최대 흡습량을 Fig. 3에 나타내었다. 각 샘플의 흡습용량은 제습제의 흡습량을 건조된 샘플의 양으로 나누어 무차원화하여 나타내었다.
Fig. 3. Effect of dew point temperature on sorption capacity for various sorption temperatures.
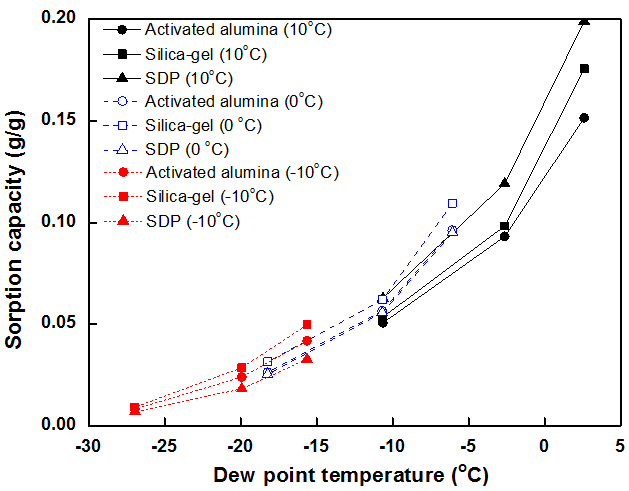
노점온도가 감소함에 따라 최대흡습량이 감소하는 경향을 보였으며, 제습제 온도가 낮아지면 동일한 노점온도 조건에서 최대 흡습량이 증가하였다. 제습제의
10℃ 온도조건일 경우 SDP의 흡습량이 가장 높게 나타나고 실리카겔, 활성알루미나 순으로 흡습량이 감소하였다. 하지만 영하의 온도조건으로 내려감에
따라 실리카겔이 가장 흡습성능이 좋았고, SDP의 흡습량이 점점 감소하는 경향을 나타내었다. 온도조건이 내려감에 따라 실험 제습제의 흡습 성능도 감소함을
보였다. 저온건조에 적용할 온도 범위인 -10℃에서 실리카겔이 성능이 가장 높게 나타났다.
노점온도에 따른 확산계수를 Fig. 4에 나타내었다.
활성알루미나의 경우 노점온도에 따른 변화가 크지 않았고, SDP의 경우 특정 노점온도에서 최대값을 보였다. 이는 SDP에 대한 선행연구(8)와도 일치한다. 실리카겔의 경우 3×10-8 m2/s 정도, 활성알루미나의 경우 6× 10-9 m2/s 정도의 값을 나타낸다. 실험 제습제 중 실리카겔의 확산계수가 가장 높았고, 활성알루미나보다 5배 큰 결과를 보였다. SDP의 경우 실리카겔과
활성알루미나에 비해 확산계수가 매우 작았다.
3. 저온진공건조 실험
3.1 실험장치 및 방법
저온진공건조 실험장치의 개략도를 Fig. 5에 나타내었다. 실험장치는 건조가 일어나는 건조챔버와 수분의 포집이 일어나는 콜드트랩(Cold trap), 진공조건을 만드는 진공펌프로 구성되어있다.
건조챔버의 열판 온도와 콜드트랩 온도를 측정하기 위해 온도센서(Range of -250~350℃, accuracy of ±0.5℃)를 설치하였고,
건조챔버 내의 진공도를 측정하기 위해 압력센서(Range of 5 ×10-9~750 Torr, accuracy of ±5%)를 설치하였다.
Fig. 5. Schematic diagram of the low temperature vacuum dryer.
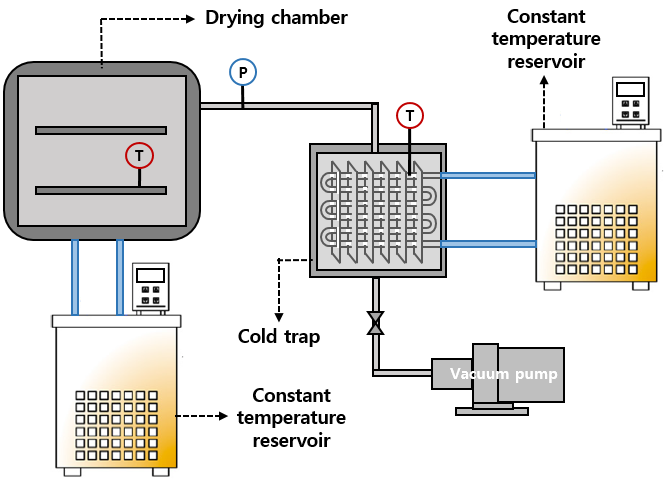
건조챔버 내에는 외부 항온조의 2차 유체를 순환시켜 온도를 제어하는 열판이 있고, 열판 위에 시료가 들어있는 트레이를 올려 전도열을 통해 건조를
수행하였다.
콜드트랩에 사용된 열교환기는 Fig. 6과 같은 형태의 핀튜브 열교환기를 사용하였고, 열교환기를 그대로 사용하는 경우와 제습제를 적용한 열교환기를 사용하는 두 가지 콜드트랩에 대해 실험을
수행하였다. 열교환기의 제원은 table 3에 나타내었다.
Fig. 6. Photograph of heat exchanger applying desiccant.
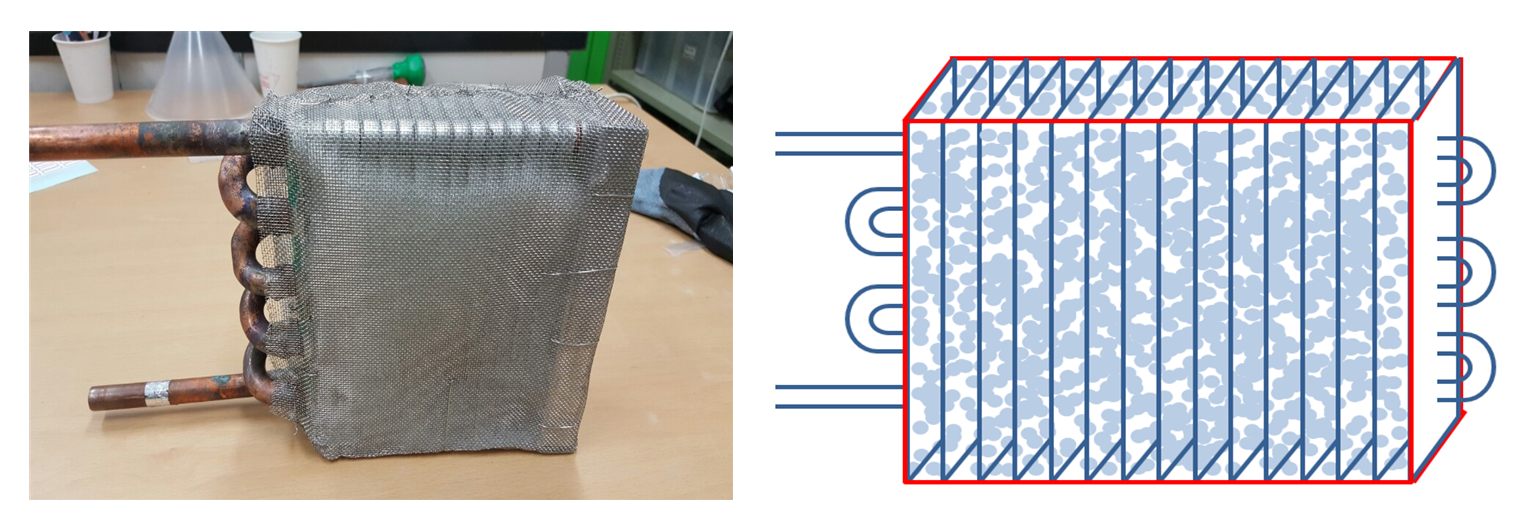
Table 3. Specification of heat exchanger
Parameter
|
Unit
|
Conditions
|
Heat exchanger size
|
mm
|
120×55×160
|
Fin pitch
|
mm
|
6.5
|
Fin material
|
-
|
Aluminum
|
콜드트랩부에 제습제를 적용한 경우의 성능분석을 위해 열교환기의 핀 사이에는 table 1의 실리카겔을 적층하는 형태를 사용하였다. 제습제의 유출을 막기 위해 간격 0.5 mm의 철망으로 열교환기 둘러싼 다음, 직경 1~2 mm의 실리카겔을
열교환기 하부에서부터 핀 사이에 물리적으로 채우는 방식을 사용하였다.
저온진공건조 실험의 시료는 폴리감마글루탐산(PGA)을 사용하였다. 폴리감마글루탐산은 청국장을 만들기 위해 ‘고초균’이라는 미생물을 이용하여 발효
시키는 과정에서 발생하는 물질 중 하나로서, 수용성, 음이온성, 생분해성 및 식용의 아미노산 고분자소재로 고부가가치의 의약품, 화장품, 기능성 식품,
환경용, 공업용 등으로 적용 범위가 매우 다양하다.(12) 실험에 사용된 폴리감마글루탐산의 초기 함수율은 95%이다.
건조챔버와 콜드트랩 온도를 실험조건에 따라 설정 후, 시료를 넣은 트레이를 건조챔버 내의 열판에 올린다. 진공펌프를 이용하여 진공조건을 만들어 건조를
수행하였다. 실험 완료 후, 제습제의 재생 과정을 진공조건에서 콜드트랩에 연결되어있는 항온조를 이용하여 50℃의 온도로 2시간 동안 수행하였다.
제습제의 적용 여부, 열판 온도, 콜드트랩 온도 및 시료의 두께에 따라 실험을 진행하였고, 실험조건은 table 4 에 나타내었다. 제습제 적용 유/무에 따른 콜드트랩 온도를 다르게 하여, 콜드트랩 온도 상승에 따른 제습제의 적용가능성에 대하여 검토하였다.
Table 4. Experimental conditions
Parameter
|
Unit
|
Conditions
|
Cold trap temperature
|
℃
|
-20*/-10**
|
Heating plate temperature
|
℃
|
10/20/30
|
Thickness of sample
|
mm
|
1/3/5
|
* Cold trap temperature without desiccants.
** Cold trap temperature with desiccants.
3.2 건조 과정 분석
건조 진행 과정에 따른 함수율 및 시료의 상부 온도 변화를 Fig. 7에 나타내었다. 건조 초기, 시료 상부 온도는 수분의 증발(승화)에 의해 급격히 온도가 낮아진다. 그 후, 증발(승화)에 의한 잠열과 열판에서 전해지는
전도열이 균형을 이루게 되어 일정한 온도를 유지하게 되며, Fig. 8(a)의 시료의 형상과 같이 아랫면은 액상이고 윗면은 얼어있는 형태를 가진다.
Fig. 7. Transient variation of sample temperature and moisture content at heat plate temperature 30℃ for 3 mm sample thickness.
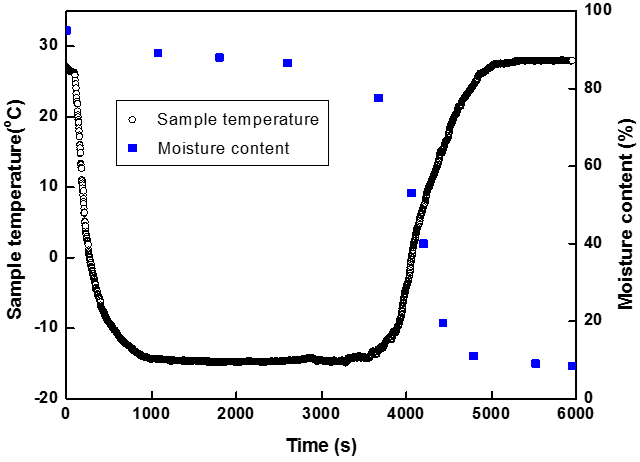
Fig. 8. Effect of moisture content on the sample shape in case of 30℃ heat plate temperature and 3 mm thickness of the sample.
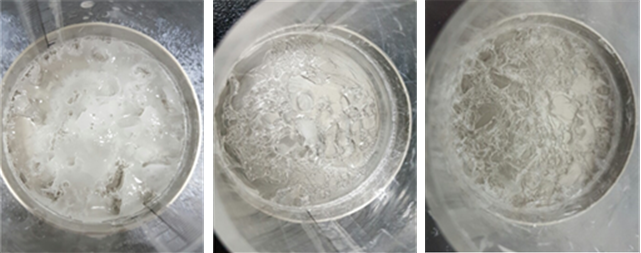
건조 시작 후 약 3,800초 후부터 시료의 온도가 점차적으로 상승하게 된다. 이는 수분의 증발(승화)율의 감소로 여겨지며, Fig. 8(b)와 같이 시료의 형상이 겔의 형태로 변하게 되어 증발율이 감소하는 것으로 보인다. 약 4,800초 후에는 시료 상부의 온도가 열판의 온도에 거의 근접하게
된다. 함수율이 9% 정도에 도달하게 되며 더 이상의 큰 변화를 보이지 않게 되며, Fig. 8(c)와 같이 건조된 시료의 형상을 확인할 수 있다.
건조를 진행함에 따라, 약 4,000초 이후 시료의 상부 온도와 열판 온도의 차는 시료의 전도열전달량과 증발(승화)잠열량에 의해 지수 함수의 형태로
감소하게 된다. 이 때, 지수함수의 지수는 시료의 증발(승화)잠열량의 변화에 의해 건조과정 중 변동하게 된다. 건조 완료 시점에서는 증발잠열량이 미미해짐에
따라 일정한 지수값을 가지게 된다. 지수값의 변화를 확인하기 위해 Fig. 9와 같이 열판온도와 시료 상부 온도 사이의 온도차를 자연로그 형태로 나타내어 기울기의 변화를 관찰할 수 있으며, 기울기의 변화가 일정해지는 지점을
건조완료지점으로 가정하였다. 이는 Fig. 7의 함수율 결과와도 일치하였다.
Fig. 9. Transient variation of gradient of nature log for temperature difference and sample temperature.
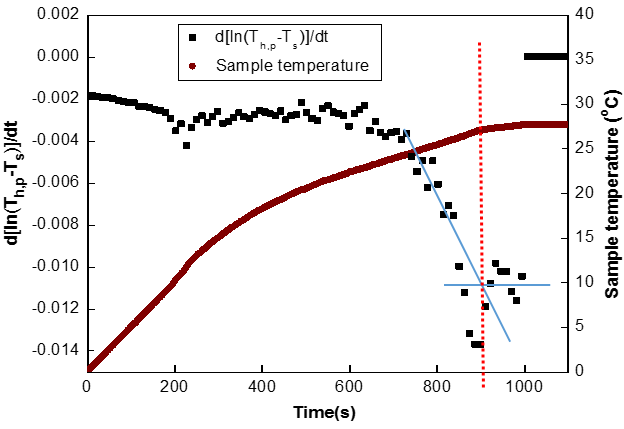
3.3 저온건조실험 결과 및 고찰
콜드트랩의 제습제 적용 유/무에 따라 시료의 두께 및 열판 온도 변화에 따른 건조시간을 Fig. 10과 Fig. 11에 나타내었다. 건조가 시작되면, 시료 상부에서 증발(승화)이 발생하게 되고 증발(승화)잠열로 인해 Fig. 7과 같이 증발(승화)부 온도가 낮아진다. 증발에 필요한 열은 열판에서 증발(승화)부로 전도에 의해 공급된다. 증발된 수분은 콜드트랩과의 수증기압차에
의해 이동하여 포집된다.
Fig. 10. Effect of sample thickness on drying time for variation of heat plate temperature.
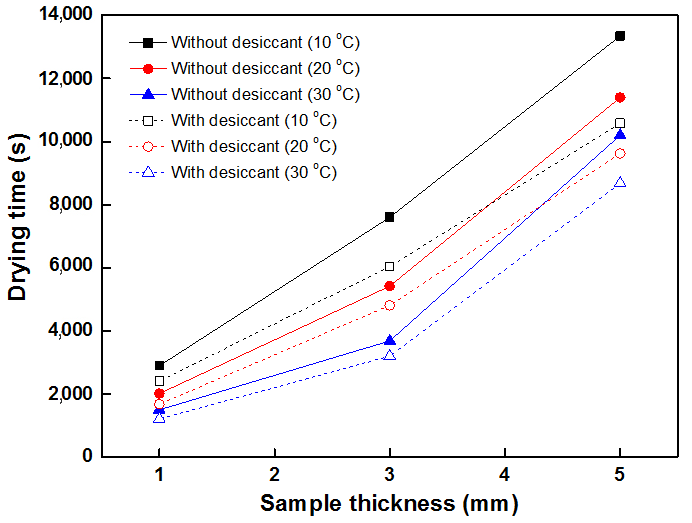
Fig. 11. Effect of heat plate temperature on drying time for variation of sample thickness.
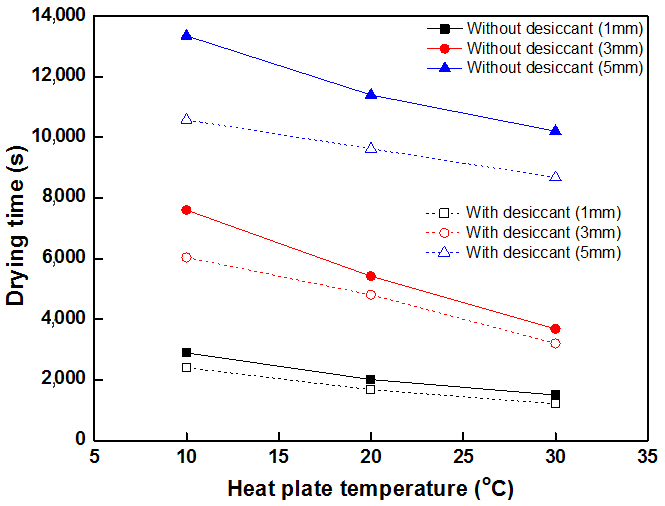
시료량이 증가하면 건조를 위해 필요한 시간도 비례하여 증가할 것으로 예상할 수 있다. 단위 시료량당 건조시간은 시료의 두께가 두꺼워질수록 Fig.
10과 같이 증가함을 보여준다. 제습제를 적용하지 않은 20℃ 조건에서의 시료두께 1 mm에 비해 3 mm의 건조시간은 약 3,000초 증가하였고,
3 mm와 비교하여 5 mm의 경우 약 6,000초 증가하여, 두께 증가에 따라 건조시간이 비선형적으로 증가하게 되는 것을 확인하였다.
시료의 두께가 증가하면, 열판에서 증발(승화)부로의 전도열저항이 증가하게 되므로, 증발(승화)부의 온도가 더 낮아지게 되는 현상이 발생한다. 이에
따라 콜드트랩과 수증기압차의 감소로 증발(승화)속도가 감소하게 되고, 건조시간이 길어지게 된다.
열판의 온도가 증가함에 따라 증발(승화)부의 온도가 상승하게 되고, 콜드트랩과의 수증기압차 증가로 증발(승화)속도가 증가하게 되는 현상이 발생하여
건조시간이 단축된다. 1 mm일 경우, 3 mm와 5 mm에 비해 열판온도의 변화에 따라 건조시간의 단축 효과가 작게 나타나는 것을 Fig. 11을
통해 확인하였다. 이는 초기진공 및 가열에 일정시간이 필요하여, 건조가 진행되는 조건이 만들어지기 위한 시간이 필요하게 되고, 상대적으로 건조시간이
짧은 1 mm의 경우 그 영향이 크게 나타남을 보였다.
콜드트랩부에 제습제를 적용할 경우, 전체적으로 건조시간이 단축되는 것을 볼 수 있다. 제습제에 의해 콜드트랩 내부의 수증기압이 낮아지게 되므로 시료와
콜드트랩과의 수증기압차 증가에 따라 증발(승화)속도가 증가하는 현상이 발생하여 건조시간이 단축된다.
제습제 적용 유/무에 따른 건조시간을 비교해 본 결과, 두께 변화에 따라 1 mm, 3 mm, 5 mm에서 각각 평균 21.3%, 17.8%, 20.7%
정도의 건조시간이 단축됨을 보였다. 그리고 열판온도에 따라 10℃, 20℃, 30℃에서 각각 23.1%, 17.9%, 18.8% 의 건조시간 단축을
확인하였다.
콜드트랩의 온도를 -20℃에서 -10℃로 10℃ 상승시켰음에도 제습제를 적용한 경우 평균 20% 정도의 건조시간이 단축되었고, 최대 24%의 건조시간이
단축되는 결과를 얻었다.
Fig. 12는 콜드트랩부에 제습제의 적용 유무에 따른 최종 함수율을 비교하여 나타내었다. 비교 결과 제습제의 적용 유무에 관계없이 10% 내외의 함수율을 가지는
건조물을 얻을 수 있었다.
Fig. 11. Effect of heat plate temperature on drying time for variation of sample thickness.
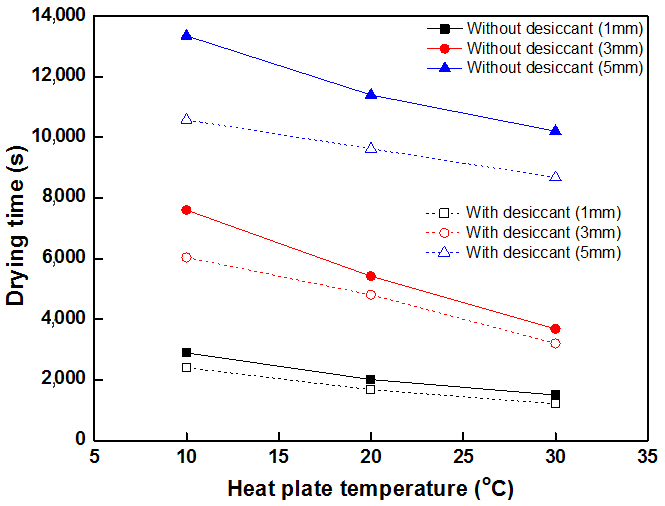
4. 결 론
저온진공건조 공정에 제습제를 적용하기 위해 저온조건에서의 제습제에 대한 성능평가를 수행하였고, 제습제 성능평가를 통해 선정한 제습제를 저온진공건조장치의
콜드트랩부에 적용하여 건조시간과 에너지 소비에 미치는 영향에 대한 연구를 수행하였다.
제습제의 주변 수증기압(노점온도)가 증가하면 최대흡습량이 증가하고, 제습제 온도가 낮을수록 동일한 수증기압(노점온도) 조건에서 최대 흡습량이 증가한다.
제습제의 10℃ 온도 조건에서는 SDP의 최대 흡습량이 가장 컸으나, 온도가 낮아질수록 실리카겔의 최대 흡습량이 커졌다. 실리카겔의 확산계수가 활성알루미나와
SDP에 비해 가장 우수하였다.
시료의 두께가 증가하면 단위 시료량당 건조시간은 길어지며, 열판의 온도 상승에 따라 건조시간은 단축된다. 콜드트랩부에 제습제를 적용할 경우, 콜드트랩의
온도를 -20℃에서 -10℃로 10℃ 상승시켰음에도 불구하고 평균 20% 정도의 건조시간이 단축되었다.
저온진공건조 공정에 제습제를 적용함으로써 콜드트랩의 온도를 상승시키고 건조시간의 단축에 의해 에너지 소비를 줄일 수 있다고 판단된다. 그러나 제습제의
재생과정에 대한 연구와 열펌프의 방열, 폐열을 제습제의 재생에 활용하기 위한 추가적인 연구가 필요할 것이라고 생각한다.
후 기
본 연구는 2015년도 산업통상자원부의 재원으로 한국에너지 기술평가원(KETEP)의 지원을 받아 수행한 연구 과제(20134010200580)이며,
한국산업기술평가관리원(KEIT)의 지원을 받아 수행된 과제입니다(10049085, 바이오 소재의 장기 저장을 위한 저온/동결 건조 원천 기술 개발).
References
Choe S. Y., Moon S. B., 2002, A study on the thermal characteristics of the low temperature
vacuum dryer by material layers, Journal of the Korean Society of Marine Engineering,
Vol. 26, pp. 226-232

Kang J. S., Sim Y. H., Byun S. Y., Chang Y. S., Kang B. H., 2015, An experimental
study on freeze drying process for Poly γ glutamic acid, Korean Journal of Air-Conditioning
and Refrigeration Engineering, Vol. 27, pp. 645-651

Adams G. D. J., Cook I., Ward K. R., 2014, The principle of freeze-drying, Methods
in Molecular Biology, Vol. 1257, pp. 121-143

Djaeni M., Straten G., Bartels P. V., Sanders J. P. M., Boxtel A. J. B., 2009, Energy
Efficiency of Multi-Stage Adsorption Drying for Low-Temperature Drying, Drying Technology,
Vol. 27, pp. 555-564

Gurtas S. F., Evranuz O., 2000, Low temperature mushroom drying with desiccant dehumidifiers,
Drying Technology, Vol. 18, pp. 433-445

Sosle V., Raghavan G. S. V., Kittler R., 2003, Low-Temperature Drying Using a Versatile
Heat Pump Dehumidifier, Drying Technology, Vol. 21, pp. 539-554

King V. E., Liu C. F., Liu Y. J., 2001, Chlorophyll stability in spinach dehydrated
by freeze-drying and controlled low-temperature vacuum dehydration, Food research
International, Vol. 34, pp. 167-175

Lee J. H., Lee D. Y., 2012, Sorption characteristics of a novel polymeric desiccant,
International Journal of Refrigeration, Vol. 35, pp. 1940-1949

Rivero M. J., Ibanez R., Ortiz I., 2002, Mathematical modelling of styrene drying
by adsorption onto activated alumina, Chemical Engineering Science, Vol. 57, pp. 2589-2592

Gurgel J. M., Andrade L. S., Grenier P., Meunier F., 2001, Thermal Diffusivity and
Adsorption Kinetics of Silica-Gel/Water, Adsorption, Vol. 7, pp. 211-219

Carslaw H. S., Jaeger J. C., 2011, Conduction of heat in solids, Oxford Science Publications,
Second edition, pp. 230-254

Sung M. H., Park C., 2009, New bioindustrial development of high molecular weight
of poly-gamma-glutamic acid produced by Bacillus subtilis(chungkookjang), Polymer
Science and Technology, Vol. 20, pp. 440-446
