Lee Sangmu
(이상무)
1
Park Byung-Duck
(박병덕)
2†
-
Shizuoka Works, Mitsubishi Electric Corp., Shizuoka, 422-8528, Japan
(미쯔비시전기(주) 시즈오까제작소)
-
Department of Automotive Engineering, Kyungpook National University, Sangju, 41566,
Korea
(경북대학교 자동차공학부)
Copyright © 2016, Society of Air-Conditioning and Refrigeration Engineers of Korea
keywords
Heat exchanger, Two-port tube of small inner diameter, Tube expanding, Heat transfer coefficient, Pressure drop
키워드
열교환기, 연결세경관, 확관, 열전달계수, 압력강하
기호설명
cpa:공기정압비열 [kJ/kgK]
h:비엔탈피 [kJ/kg]
:질량유량 [kg/s]
Q:열교환량 [W]
T:온도 [K]
V:속도 [m/s]
아래첨자
a:공기
cond:응축기
evap:증발기
in:입구
out:출구
r:냉매
1. 서론
공조기에서 가장 중요한 과제중의 하나는 에너지효율의 향상이라 할 수 있겠다. 공조기의 효율향상을 위하여 열교환기의 효율향상과 소형화를 꽤하고 있으며
전열촉진을 위한 노력과 더불어 전열관의 세경화를 위한 연구가 활발하게 수행되고 있다.(1)
(2)
(3)
(4) 전열관이 세경화 되면 휜피치의 단축으로 단위체적당 전열면적의 향상과 휜효율 향상을 얻을 수 있어 열교환기의 컴팩트화가 가능하고 원가절감의 효과를
최대화 할 수 있다.
Lee and Park(5)은 두 개의 내경이 존재하는 전열관을 의미하는 연결세경관(two-port tube)을 사용하여 휜관형 열교환기의 성능에 가장 큰 영향을 미치는 공기측의
전열성능과 압력강하 특성을 계산과 실험을 통하여 그 우수함과 사용가능성을 보고하였다. 하지만 연결세경관을 공조용 열교환기로 제작하고 상용화를 위해서는
기계에 의한 확관이 필요하고 이때 휜구멍(fin collar)과 전열관과의 접촉에 따른 접촉열저항이 존재하여 이에 따른 열교환기의 전열특성 고찰이
필요하다.(6)
(7)
(8)
(9)
본 연구에서는 동일한 체적에서 종래의 원관에 비해 관내의 전열면적이 확대된 동제의 연결세경관을 적용한 열교환기의 기계확관 적용가능성을 확인하기 위해
두 개의 내경이 존재하는 전열관의 내경에 확관볼(expanding bullet)을 동시에 삽입하여 전열관을 확대하는 과정의 구조해석을 통해 전열관과
휜구멍의 접착성과 휜의 변형을 검토하였다. 그리고 실험을 통해 기존의 내면가공관과 연결세경관을 이용한 열교환기의 냉매측 압력강하 특성과 열교환기의
열통과율 특성을 비교 분석하였다.
2. 수치해석
휜관형 열교환기의 기계 확관은 전열관을 알루미늄제 휜구멍에 삽입하고 전열관내에 확관볼을 넣어 전열관을 확관시키는 공정이 이루어지고 휜과 전열관을 밀착시켜
열교환기가 제작한다.
Fig. 1에 연결세경관의 단면도를 나타내었고, Fig. 2에 휜, 연결세경관, 확관볼로 구성된 계산영역을 나타내었다. 연결세경관은 대칭면을 이용하여 Fig. 1과 같이 원주방향으로 90°의 영역을 모델화하였다.
이 때문에 알루미늄 휜은 원반형태의 모양으로 모델화되었다.
Fig. 1. Cross sectional view of two-port tube.
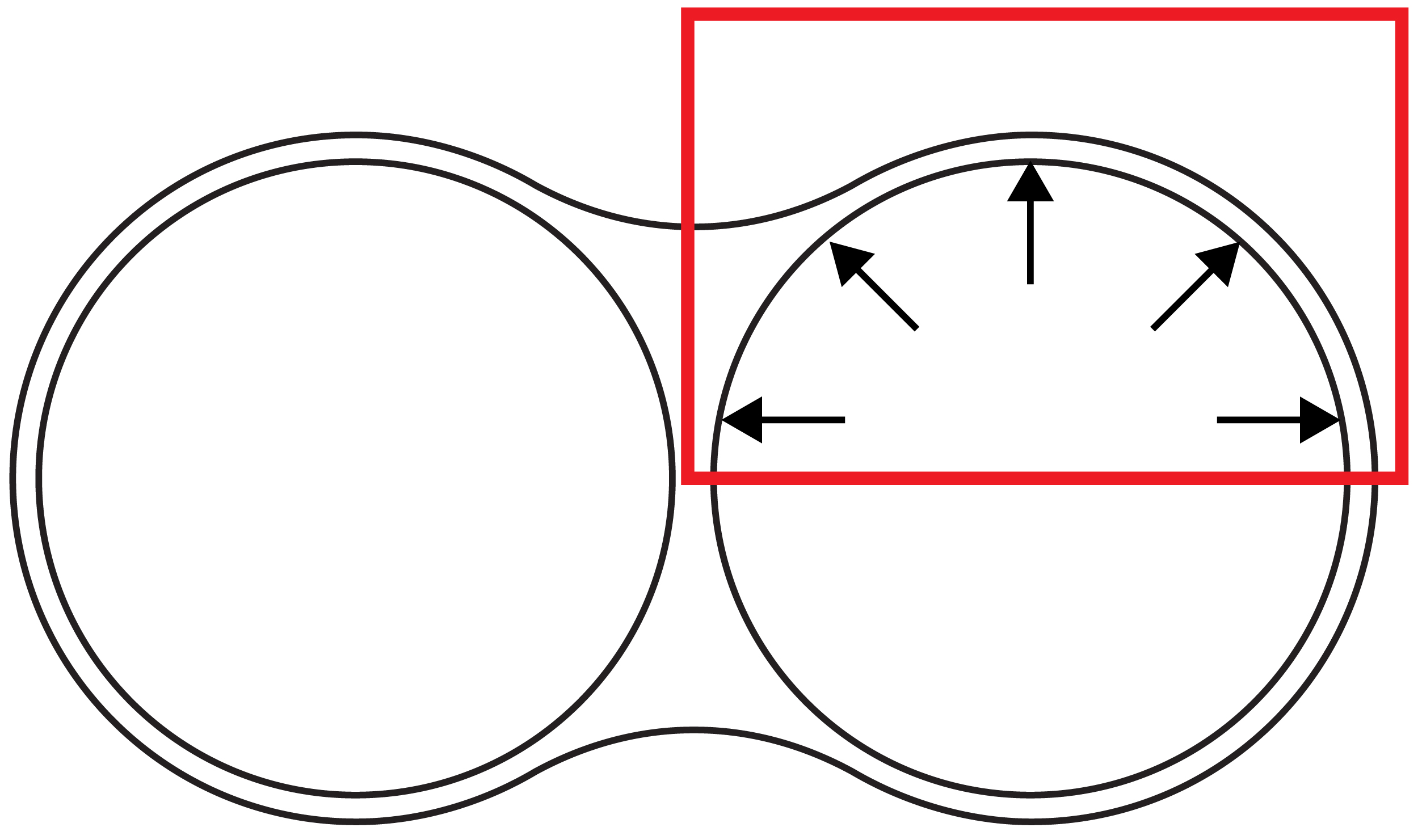
Fig. 2. Schematic diagram of calculation model.
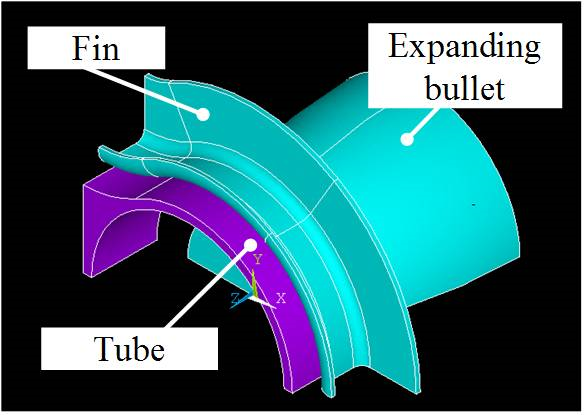
수치해석은 범용의 구조해석 프로그램 ANSYS를 이용하여 3차원 비선형계산을 수행하였다. 계산모델의 경계조건으로서 연결세경관이 확관시에 길이 방향으로
수축되지 않도록 구속되어있는 것을 고려하여 전열관의 전후단 길이방향으로는 변위가 없도록 구속조건을 주었다. 또 휜과 연결세경관의 마찰계수는 없는 것으로
하고 확관에 의해서 형성된 경사면을 따라서 휜이 하류측으로 이동하는 것을 구속하였다. 연결세경관과 휜의 원주단면방향은 대칭으로 하고 주기경계조건(periodic
boundary condition)을 주었다. 또 휜 사이의 접촉을 고려하여 길이방향의 휜의 변형은 구속하였다.
Table 1에 재료의 물성치를 나타내었다. 연결세경관은 동관, 휜은 알루미늄으로서 항복조건은 모두 von Mises형의 등방성 항복함수, 경화측 조건은 등방경화를
가정하였다. 변형저항은 Suzuki et al.(10)의 풀림 처리한 순수 알루미늄 및 순동의 데이터로부터 근사식을 작성하여 사용하였다.
Table 1. Material properties
Structure
|
Tube
|
Fin
|
Material
|
Copper
|
Aluminium
|
Young’s Modulus [MPa]
|
110,000
|
70,000
|
Poisson’s ratio
|
0.3
|
0.3
|
Table 2는 계산에 사용된 연결세경관, 휜, 확관볼의 사양이다. 연결세경관은 외경 5 mm의 평활관으로 구성되어있다.
Table 1. Configurations of two-port tube
Tube
|
Outer diameter [mm]
|
5.0
|
Wall thickness [mm]
|
0.2
|
Fin
|
Hole diameter [mm]
|
5.2
|
Fin thickness [mm]
|
0.095
|
Bullet
|
Outer diameter [mm]
|
4.76~4.91
|
2.1 계산결과
Fig. 3(a)~Fig. 3(f)는 연결세경관의 외면의 단면도로 확관볼의 직경이 4.76, 4.79, 4.82, 4.85, 4.88, 4.91 mm의 결과이다. 단면도에 나타낸 것과
같이 확관볼의 직경이 클수록 연결세경관의 중심부의 두께가 얇게 되고, 원주측이 균일하게 확대되어 휜구멍의 안쪽과 접촉한다. 확관볼의 직경이 클수록
연결세경관의 중심부의 x측의 전열관 두께가 0.2 mm에서 각각 0.13, 0.12, 0.10, 0.09, 0.07, 0.06 mm로 얇아지고, 연결세경관의
중심부의 y측의 최대변형양은 각각 0.23, 0.29, 0.35, 0.42, 0.50, 0.58 mm로 확대되어 휜구멍의 안쪽과 접촉한다.
Fig. 3. Cross section of tube after expansion.
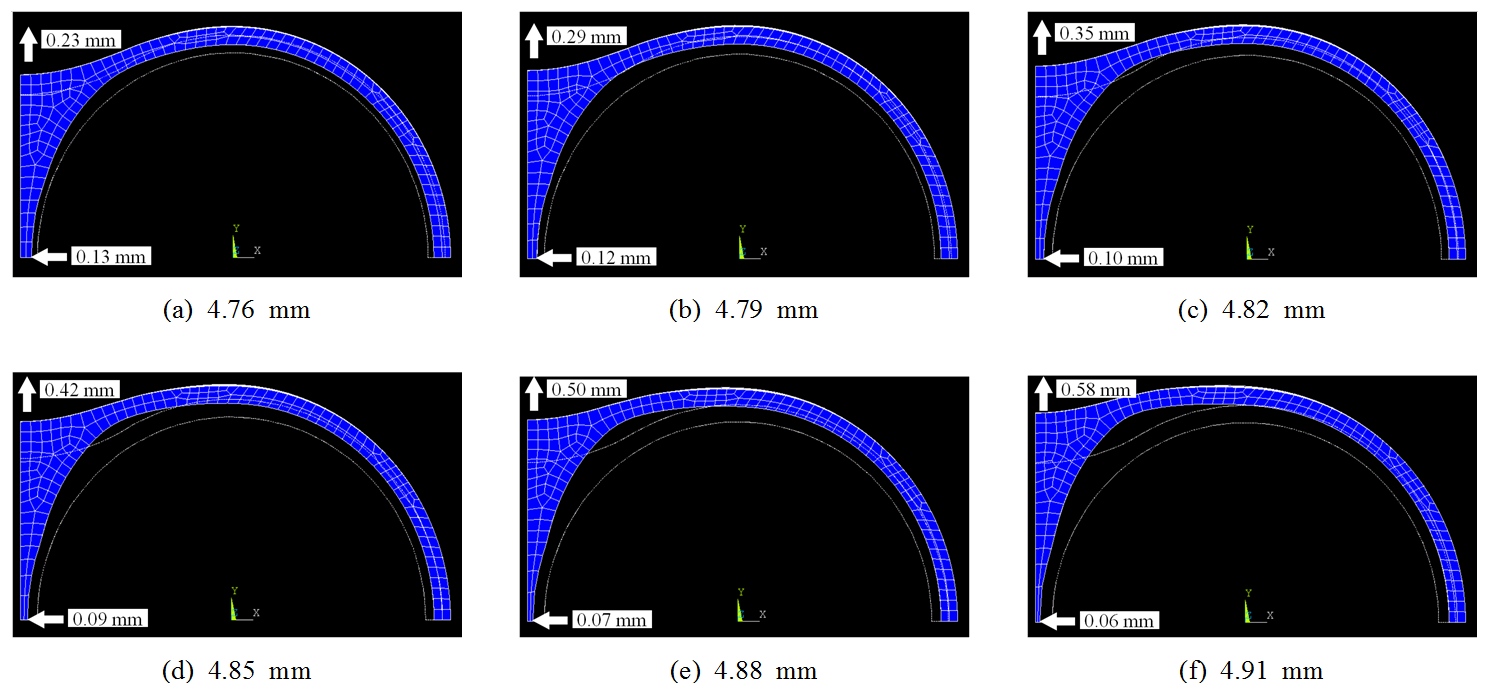
Fig. 4(a)~Fig. 4(c)는 확관볼의 직경에 따른 휜의 변형을 나타내었다. 확관볼의 직경이 클수록 휜의 변형량이 1.05, 1.24, 1.71 mm로 크게 되어 통기저항이
악화될 수 있을 가능성이 있다. 따라서 확관볼의 직경은 전열관과 휜구멍의 접착성과 휜의 변형을 고려하여 4.85 mm로 선정하여 시험용 열교환기를
제작하였다.
Fig. 4. Cross section of fin after expansion.
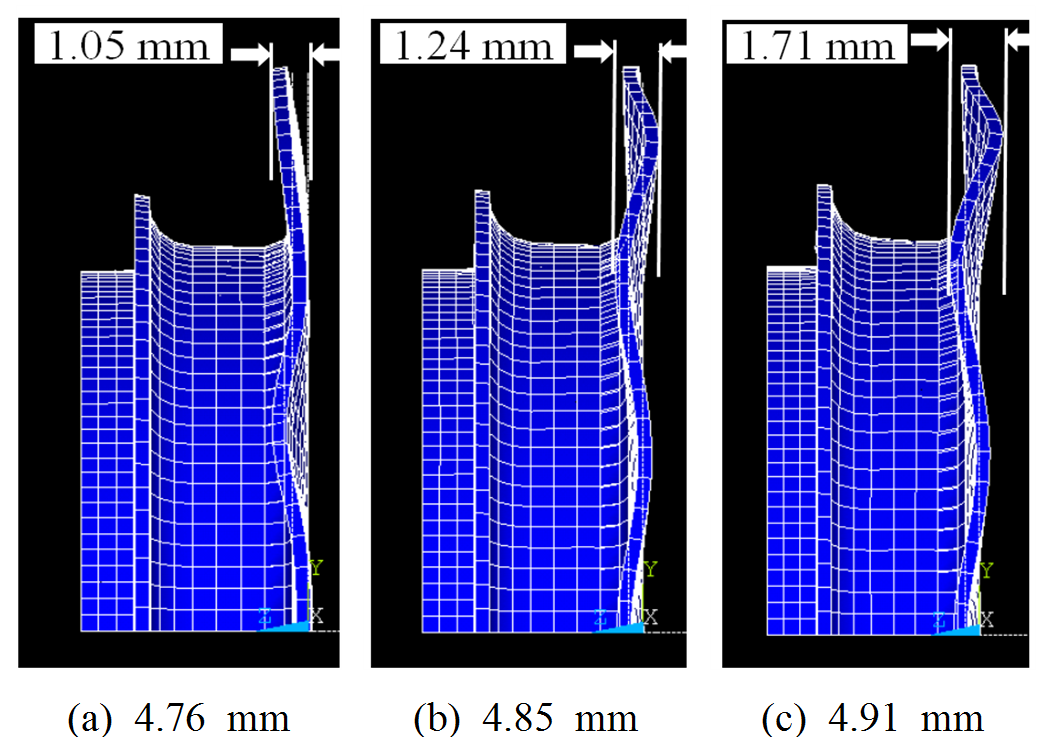
3. 실 험
3.1 실험장치 및 실험방법
성능시험에 사용된 열교환기의 사양은 Table 3과 같다. 열교환기는 공조기에서 일반적으로 사용되는 휜관형 열교환기로 알루미늄휜과 동관으로 구성되어있다. 기존의 열교환기는 직경 7 mm의 내면가공관으로,
연결세경관 열교환기는 직경 5 mm의 평활관인 연결세경관으로 동일체적의 시험용 열교환기를 제작하였다.
Table 3. Specification of tested heat exchanger
|
Conventional
|
New
|
Size[mm]
|
300×245×25.4
|
Number of tubes
(row×transverse)
|
2×12
|
2×20
|
Number of circuits
|
1
|
1, 2
|
Tube
|
Type
|
Inner grooved
|
Smooth, two-port
|
Diameter[mm]
|
7.0
|
5.0
|
Wall thickness [mm]
|
0.23
|
0.20
|
Fin
|
Pitch[mm]
|
1.2
|
1.2
|
Thickness[mm]
|
0.095
|
0.095
|
Type
|
Resin coated slit
|
연결세경관 열교환기는 기존의 열교환기에 비하여 단피치가 작아서 단수가 증가하였다. 또한 냉매관로의 영향을 조사하기 위하여 세경관 열교환기는 1회로와
2회로를 각각 제작하였으며 공기와 냉매의 유동방향은 일반적인 휜관형 열교환기와 같이 응축실험에서는 대향류, 증발실험에서는 평행류가 되도록 회로를 구성하였다.
Fig. 5는 기존의 열교환기의 회로와 연결세경관 열교환기의 회로를 나타내었다.
Fig. 5. Path pattern of heat exchanger.
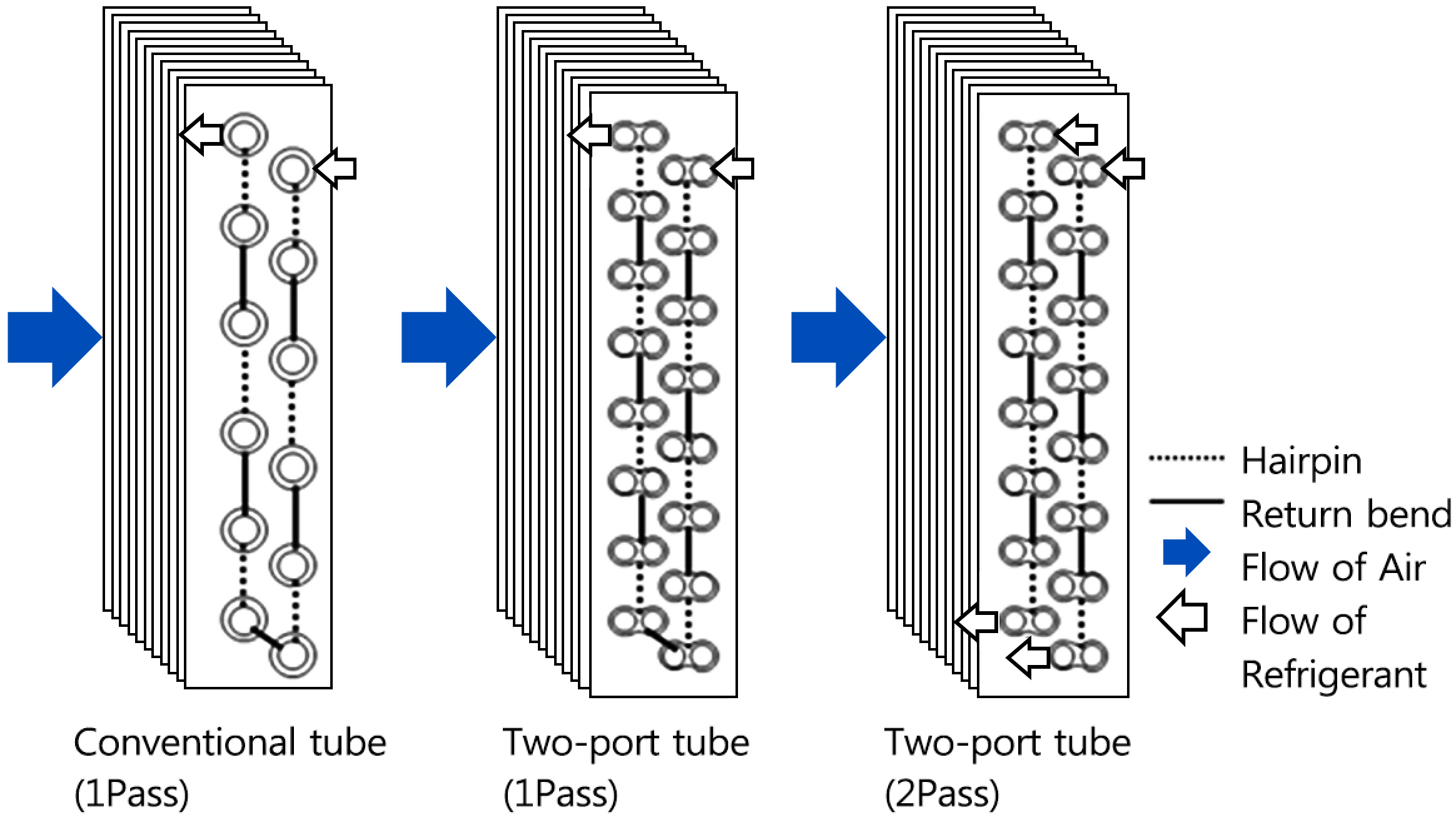
Fig. 6에 공기열교환기용 성능측정 장치의 개요를 나타내었다. 장치는 항온항습기능이 있는 흡입형 풍동과 냉동사이클로 구성되어있다. 시험용 열교환기는 풍동의
공기흡입구와 출구사이에 설치되어 있다. 열교환기의 상류측과 하류측에 각각 공기채집기(air sampler)가 배치되어있고 공기채집기에서 채집된 공기의
건구온도와 습구온도를 측정하였다. 또 공기채집기의 하류측에는 팬(Sirroco fan)이 설치되어 공기배출구로 공기를 배출하였다. 또 열교환기와 공기채집기의
사이에 는 시험용 열교환기를 통과한 공기를 정류하기 위한 정류판(rectifier)이 설치되어있다.
Fig. 6. Test apparatus for heat exchanger.
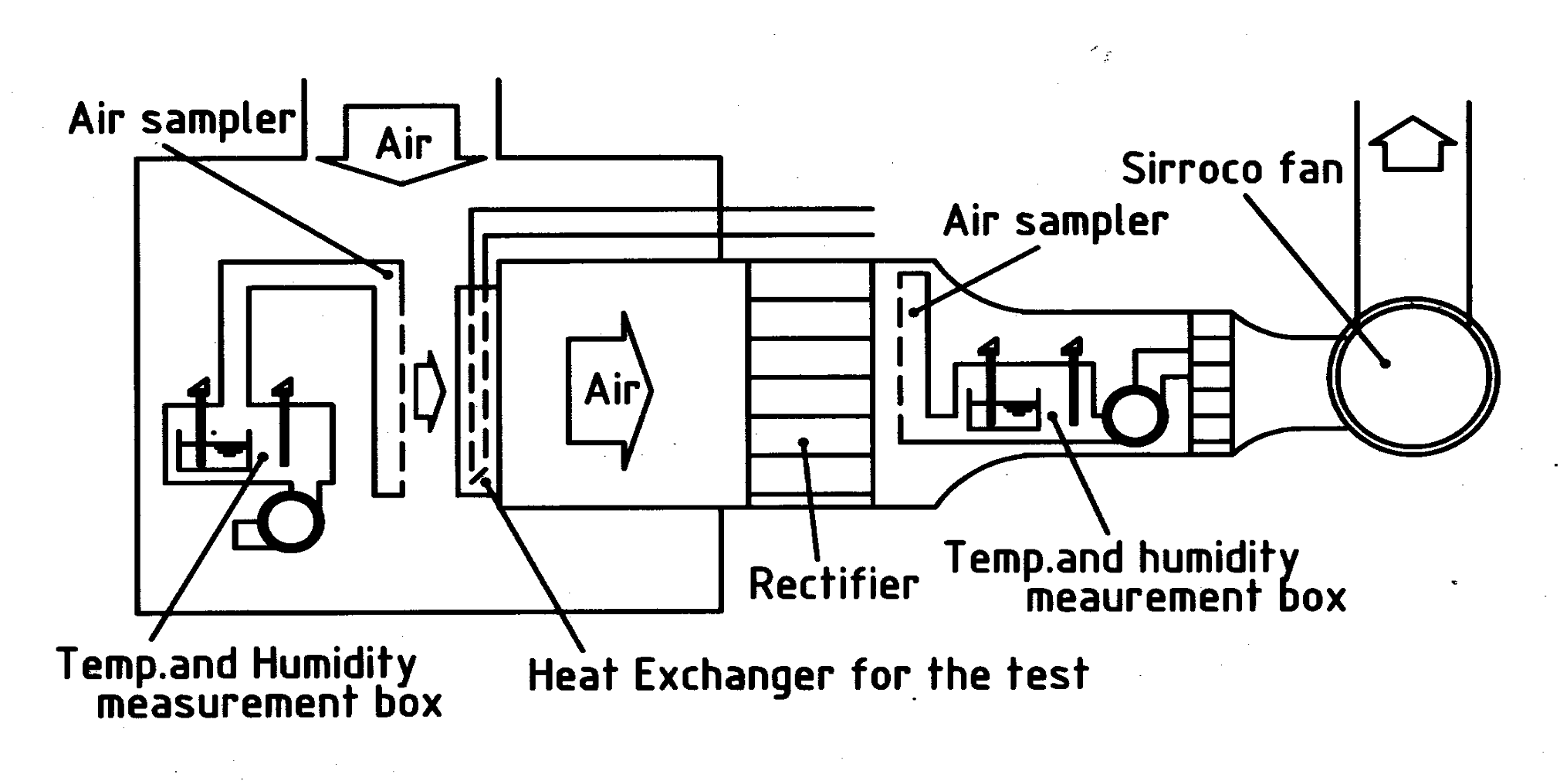
시험용 열교환기에로의 냉매 공급장치는 압축기, 오일분리기, 응축기, 팽창밸브, 증발기, 수액기, 유량계로 구성되어있다. 냉각회로의 유량과 온도를 통해
냉매의 압력을 조절하고 히터를 통해 냉매의 온도를 조절하여 냉매배관을 통하여 풍동 내에 설치된 시험용 열교환기의 내부로 냉매를 공급하였다. 열교환기의
입구 및 출구에는 냉매의 온도 및 압력을 측정하기 위한 온도계와 압력계가 설치되어있다.
냉매의 압력측정에는 압력계(측정오차 ±10 kPa)를, 냉매유량은 Coriolis식 질량유량계(정도 ±0.2%), 각부의 온도측정에는 시스형 백금저항체(Pt100,
Class A, 정도 ±0.02 K)를 이용하였다. 공기의 체적유량은 노즐전후의 정압차의 측정치(정밀차압계, 정도 ±0.1 kPa)로부터 계산 하였다.
시험용 열교환기의 공기와 냉매(R410a)의 시험조건은 Table 4와 같다. 시험은 주어진 공기유속에서, 냉매온도, 과냉도(응축), 과열도(증발)가 되도록 팽창밸브를 통해 냉매유량을 조정하며 수행하였다.
Table 4. Test conditions of heat exchanger performance
|
Condenser
|
Evaporator
|
Air side
|
Dry/Wet bulb[℃]
|
20/15
|
27/19
|
Air velocity[m/s]
|
0.8, 1.2, 1.6
|
1.5, 2.0, 2.5
|
Refrigerant
side
|
Temperature[℃]
|
45
|
7.5
|
Inlet temp.[℃]
|
70
|
-
|
Inlet quality
|
-
|
0.2
|
Outlet SC[℃]
|
5
|
-
|
Outlet SH[℃]
|
-
|
5
|
냉매측의 열교환량은 식(1)과 같이 냉매의 출입구 엔탈피 차와 냉매유량(
)으로부터 산출하였다.
공기측의 열교환량은 응축기의 경우는 식(2)와 같이 열교환기의 입구공기와 출구공기의 건구 온도차로 계산하였고, 증발기의 경우는 식(3)와 같이 입구공기와 출구공기의 엔탈피차로 산출하였다.
여기서
는 응축기,
는 증발기 공기의 질량유량이다.
식(1)과 식(2)와 식(3)으로 계산한 냉매측 열교환량과 공기측 열교환량과의 열수지는 ±5%의 오차 내에서 일치하였다. 여기서 R410a의 물성치는 REFPROP를 이용하여
계산하였다.
각종 계측에 포함된 오차가 열교환량에 미치는 부정확도는 식(4)와 같이 공기의 풍량, 공기의 정압비열, 공기의 입구와 출구온도, 공기의 비체적으로 계산하였고 열교환량의 정확도는 0.6%이었다.(11)
여기서
은 공기의 풍량,
는 공기의 비체적이다.
3.2 실험결과
Fig. 7은 연결세경관과 기존의 내면가공관을 이용한 열교환기의 냉매측 압력강하 특성이다. 압력강하 특성은 연결세경관과 기존의 원관을 사용한 열교환기의 단수의
차이에 의해 회로당 관의 길이가 달라짐으로 단위길이당 압력강하로 비교하였다.
Fig. 7. Refrigerant pressure drop of tested heat exchanger.
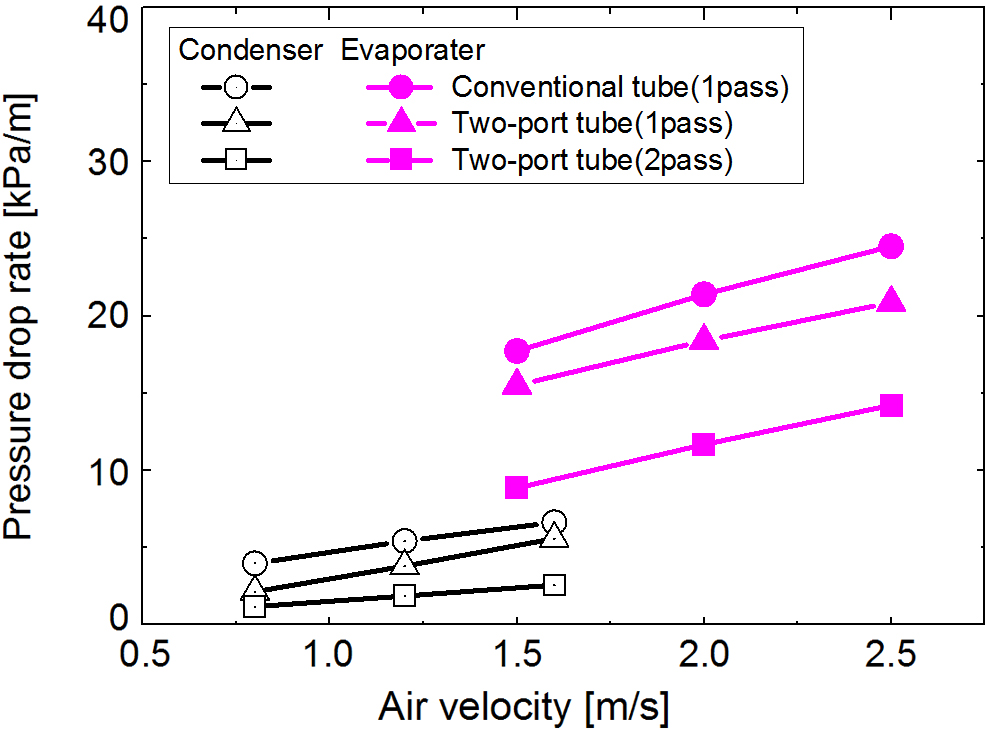
공기유속이 증가함에 따라 응축기, 증발기의 압력강하가 증가하는 것을 알 수 있다. 이는 응축기, 증발기 출구의 과냉도와 과열도가 일정함으로 공기의
유속이 증가함에 따라 냉매 유량도 증가하기 때문이다. 연결세경관을 사용한 열교환기가 기존의 열교환기에 비하여 응축기, 증발기로 사용된 경우 단위길이당
압력강하는 감소하는 것을 알 수 있다. 특히 1회로의 경우 연결세경관을 사용한 열교환기와 기존의 열교환기는 유로 단면적이 동일하고 냉매유량도 거의
동일함에도 불구하고 단위길이당 압력강하는 감소하는 것을 알 수 있다. 이는 연결세경관은 평활관을 사용하고 기존의 원관은 내면가공관을 사용하기 때문이다.
Fig. 8은 연결세경관과 기존의 내면가공관을 이용한 열교환기의 열통과율 특성이다.
Fig. 8. Overall heat transfer coefficient of tested heat exchanger.
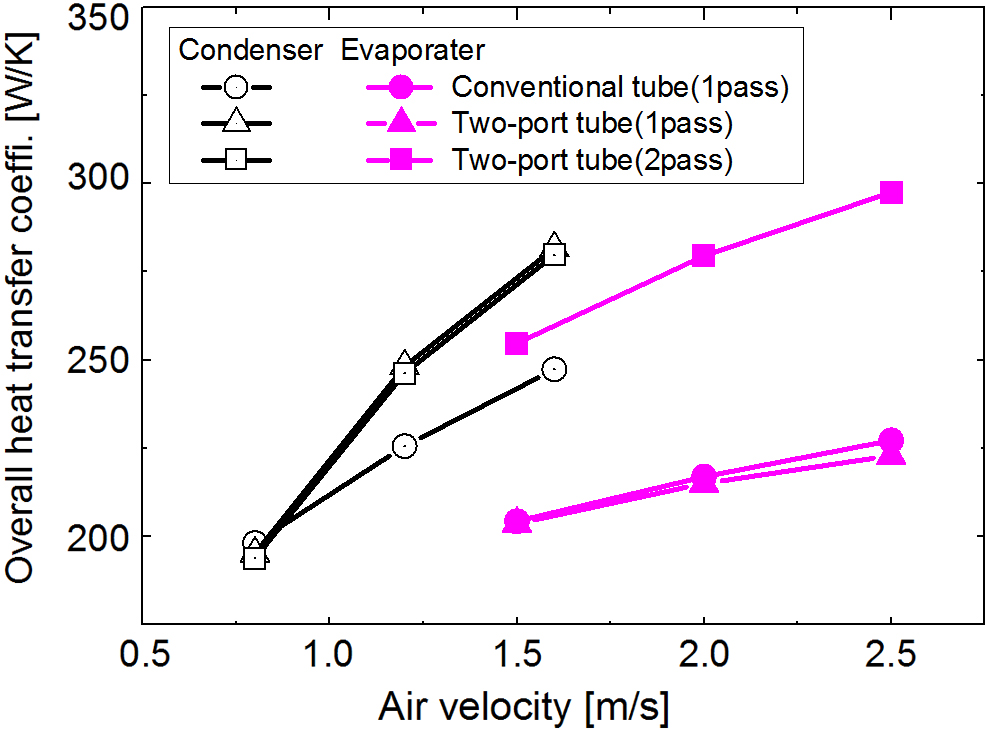
공기유속이 증가함에 따라 응축기, 증발기의 열통과율이 증가하는 것을 알 수 있다. 연결세경관을 응축기로 사용할 경우 기존의 내면가공관에 비하여 공기유속이
느린 경우 열통과율은 거의 유사하지만 공기의 유속이 빨라질수록 회로 수에 관계없이 열통과율은 증가하였다. 또한 연결세경관의 회로 수에 관계없이 열통과율의
크기는 거의 동일하였다. 연결세경관을 증발기로 사용할 경우 1회로인 경우 공기의 유속이 증가함에 따라 기존의 내면가공관과 열통과율이 거의 동일 혹은
감소하였으나 2회로로 한 경우 크게 증가하는 것을 알 수가 있다. 이는 2회로인 경우 연결세경관의 압력강하가 크게 감소한 만큼 열통과율의 증가에 기여한
것으로 사료된다.
Fig. 9와 Fig. 10은 응축시험(
= 1.6 m/s)과 증발시험(
= 1.5 m/s)에서 기존의 내면가공관 열교환기에 대한 세경열교환기의 냉매유량의 비와 열통과율의 증가율을 나타내었다. 여기서 공기의 유속은 응축기와
증발기에서 주로 사용되는 값을 비교하였다.
Fig. 9. Refrigerant flowrate ratio.
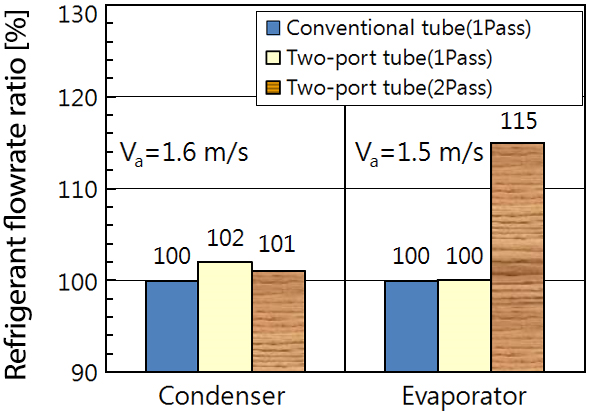
Fig. 10. Heat exchanger performance ratio.
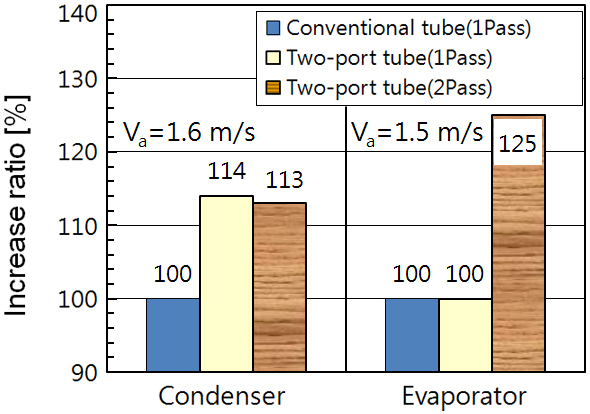
Fig. 9와 같이 기존의 열교환기와 비교하여 냉매유량은 크게 변화가 없고 증발기에서 2회로인 경우도 유로면적은 두 배가 되었지만 유량은 15% 증가한 것을
알 수가 있다
Fig. 10과 같이 응축 전열성능은 기존의 열교환기와 비교하여 연결세경관 열교환기가 1회로인 경우 14% 성능이 향상되었고, 2회로인 경우 성능이 13% 증가하였다.
이는 거의 동일한 냉매유량에서 2회로인 경우가 1회로인 경우보다 냉매유속이 작아서 열전달율의 저하에 따른 것이다. 하지만 유속의 변화와 비교하여 성능차가
1%로 작은 것은 연결세경관은 평활관으로 유속이 열전달의 향상에 크게 기여를 못하고 있기 때문이다.
Fig. 10과 같이 증발 전열성능은 기존의 열교환기와 비교하여 연결세경관 열교환기는 1회로인 경우 동등한 성능을 나타내었고, 2회로인 경우에는 성능이 25%
증가하였다. 이는 1회로인 연결세경관 열교환기가 2회로보다 압력강하가 대단히 증가하여 연결세경관 열교환기의 성능향상에 크게 영향을 미쳤기 때문이다.
4. 결 론
동일 체적에서 열교환성능 향상을 목적으로 동제의 연결세경관을 이용한 열교환기의 제작을 기계확관방식으로 수행하였고 증발과 응축 전열특성을 검토하였다.
(1) 연결세경관 열교환기를 1회로로 한 경우 연결세경관을 사용한 증발과 응축 열교환기의 단위길이당 압력강하는 내면가공관을 사용한 기존의 열교환기보다
감소하였다. 이는 연결세경관은 평활관을 사용하고 기존의 원관은 내면가공관을 사용하기 때문이다.
(2) 연결세경관 열교환기를 2회로로 한 경우 내면가공관을 사용한 기존의 열교환기보다 응축전열성능은 13% 향상하였고 증발전열성능은 25% 향상하였다.
이는 공기측의 열전달계수의 상승과 관내전열면적의 증가로 전열성능향상에 기여한 것으로 사료된다.
(3) 연결세경관 열교환기를 1회로로 한 경우 내면가공관을 사용한 기존의 열교환기보다 응축전열성능은 14% 향상하였으나 증발전열성능의 향상은 냉매
압력강하의 증가로 관찰할 수가 없었다.
(4) 연결세경관을 이용한 휜관형 열교환기가 공조기용 열교환기로서 기존의 내면가공관을 사용한 열교환기보다 우수한 열교환기 성능을 얻을 수 있었다.