Kim Deukwon
(김득원)
1
Choi Sangmin
(최상민)
2†
-
Department of Mechanical Engineering, Graduate School KAIST, Daejeon, 34141, Republic
of Korea
(한국과학기술원 기계공학과 대학원)
-
Department of Mechanical Engineering, KAIST, Daejeon, 34141, Republic of Korea
(한국과학기술원 기계공학과)
Copyright © 2016, Society of Air-Conditioning and Refrigeration Engineers of Korea
keywords
Multiple effect evaporator, TVR(Thermal Vapor Recompression), Steam ejector, Steam economy
키워드
다중효용증발기, 열 증기 재압축, 증기이젝터, 증기이용율
기호설명
A:열전달면적 [m2]
a:노즐, 디퓨저 면적 [m2]
C:비열 [kJ/kg-℃], 응축액유량 [kg/s]
d:직경 [mm]
e:튜브두께 [m]
F:용액공급유량 [kg/s]
H:증기엔탈피 [kJ/kg]
h:액체엔탈피 [kJ/kg], 열전달계수 [W/m2-℃]
L:용액유량 [kg/s]
M:마하수
m:질량유량 [kg/s]
V:증기유량 [kg/s]
P:압력 [kPa]
Q:열교환량 [W]
R:기체상수 [kJ/kg-℃]
RF:오염저항 [m2℃/W]
U:총괄열전달계수 [W/m2-℃]
T:온도 [K]
x:농도 [kg solid/kg solution]
그리스 문자
Φ:열유속 [W/m2]
Γ:단위길이당 질량유량 [kg/s-m]
τ:끓는점증가 [℃]
γ:등엔트로피 팽창상수
η:이젝터 효율
λ:열전도도 [W/m-℃]
하첨자
c:디퓨저출구증기
d:디퓨저
e:2차 증기
f:용액공급
i:증발순서
n:노즐
p:구동증기
s:증기
w:튜브벽면
1-3:이젝터 내부위치
1-4:증발기 수
1. 서론
전 세계적으로 에너지 수요는 꾸준히 증가하고 이에 따른 환경오염과 기후변화에 대한 문제는 지속적으로 제기 되고 있으며 여러 산업분야에서 공정의 개선을
통해 문제에 대응하려는 노력들이 이루어지고 있다. 증발공정은 낙농, 제지, 제약 산업 등 다양한 분야에서 용액 또는 고체 물질에 부착된 수분을 증발시키는
공정으로 액체의 증발에 따른 상변화에 많은 양의 에너지공급이 필요하다. 다중효용증발기에서는 열원으로 공급되는 증기에 의해 투입된 용액에서 증발된 증기를
다음 단(effect) 증발기의 열원 증기로 쓰는 방식으로 에너지 효율을 증진시킨다. 이 과정에서 증발성능을 향상시키고 폐증기를 활용하여 에너지 효율을
향상시키는 많은 연구가 진행되었다. Walmsley et al.(1)은 우유의 농축 공정에서 증기 재압축으로 에너지 절감 효과를 확인하였고, Hamed et al.(2)은 해수의 담수화과정에서 담수화 설비에 열 증기 압축을 적용할 경우 일반적인 공정보다 약 2배의 증발성능이 향상됨을 확인하였다.
TVR(Thermal Vapor Recompression)은 열 증기 재압축의 약자로 저압의 증기를 회수하여 압력을 상승시켜주는 방식이며 에너지 절약
효과가 크기 때문에 증발공정에 적용되어 열이용효율을 상승시켜준다. 에너지 절약효과가 큼에도 불구하고 TVR에 대한 체계적인 연구는 부족한 상태이다.
Kim and Choi(3)의 이전 연구는 제한된 입, 출구 조건에서 용액의 공급방향, TVR과 예열기를 구성한 사례별 연구를 통해 증발시스템의 성능을 분석하였고 TVR을 적용한
증발시스템의 증발 성능 향상을 확인하였다. 본 연구에서는 기본적인 장치의 설계와 다중효용증발시스템에서 TVR 적용 위치에 따른 증발기와 이젝터의 성능을
비교하였다. 성능 평가 지표로는 증발과정 중 동일한 조건의 증기를 투입하였을 때 용액에서 증발된 수분의 총량을 표시하는 증기이용율(steam economy)을
계산하였으며, 이젝터의 성능 분석을 위해 이젝터의 유량비(entrainment ratio), 압축비(compression ratio)와 팽창비(expansion
ratio)를 검토하였다.
2. 다중효용증발시스템 설계 및 성능계산
2.1 다중효용증발시스템
다중효용증발시스템에서는 서론에 소개한 것과 같이 증발기가 여러 단으로 연결되어 순차적으로 증발이 일어나며 초기에 투입된 용액은 고농도로 농축된다.
다중효용증발시스템의 증발성능을 향상시키는 대표적인 방법으로 순간 증발(flash evaporation), 증기 재압축(vapor recompression),
증기 분리(vapor bleeding)등이 있다.
순간 증발은 고온, 고압의 액체가 flash tank에서 감압되어 순간적으로 증발이 일어나는 현상으로 액상과 기상으로 분리된다. 이때 발생된 증기는
높은 에너지를 갖게 되며 증발시스템에 투입되어 전체적인 에너지 효율을 상승시킨다.
증기 분리는 증발시스템에서 분리된 증기로 용액의 온도를 상승시키는 것을 의미한다. 용액의 온도를 상승시키는 대표적인 장치는 예열기(preheater)이며
증발기에서 분리된 증기를 에너지원으로 이용하여 용액의 온도를 상승시킨다. 증발기에 투입된 용액의 온도가 상승되면 증발기와의 온도차가 커지므로 용액으로
부터 증발하는 수분의 양은 증가한다.
증기 재압축은 증발과정 중 발생된 저압의 증기를 고압으로 압축하여 고온의 증기를 증발시스템에 재공급하는 것을 의미한다. 투입된 증기유량의 증가와
온도의 상승으로 높은 에너지의 증기가 증발시스템에 투입되며 증발성능은 향상된다. TVR은 증기 재압축의 한 방법이며 TVR을 구성하는 주요장치는 이젝터이다.
이젝터는 Fig. 1과 같이 흡입실(suction chamber), 노즐(nozzle) 및 디퓨저(diffuser)로 이루어져 있고 노즐 부분에서 증기가 고속으로 분사되어
흡입실 내부의 압력을 감소시켜 저압의 2차 증기를 흡입하게 된다. 구동증기와 흡입증기는 혼합되며 디퓨저에서 고속의 혼합증기는 고압으로 전환되어 배출된다.
본 연구에서는 증발 성능을 향상시키는 방법 중 증기 재압축 효과에 초점을 맞추어 TVR의 적용방법에 따른 증발시스템을 구성하였다.
Fig. 1. Schematic diagram of the ejector.
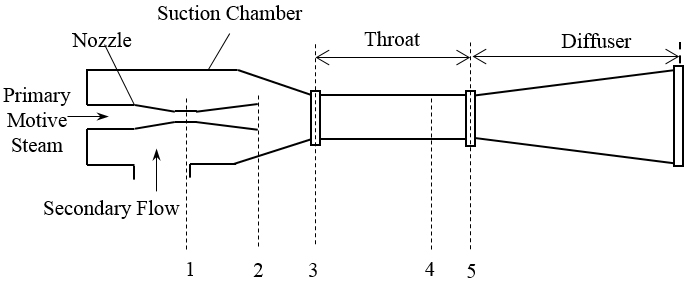
2.2 검토대상: 4단 증발시스템
강하막식 증발기(falling film type evaporator)를 채택한 4단 증발기를 구성하여 TVR의 적용유무와 위치에 따른 증발시스템의
사례별 연구를 진행 하였다. Fig. 2는 강하막식 증발기의 구성도이며 상부에 투입된 용액은 얇은 막의 관을 통과하게 된다. 증발기에 증기가 유입되면 용액과의 열 교환으로 증기는 응축되고
용액은 방출된 응축열을 흡수하여 증발과정을 거쳐 증기와 농축된 용액으로 분리된다. 분리된 증기는 다음 증발기의 에너지원으로 사용되며 농축된 용액은
증발과정을 거쳐 고농도로 농축된다. 이와 같은 연쇄 반응으로 증발이 일어나고 용액의 농도는 상승하게 된다. Fig. 3은 5가지 증발시스템의 구성도이며 모든 증발시스템은 설탕 수용액을 사용하여 용액을 순방향으로 공급하였다. Case 1은 증발시스템에 이젝터를 구성하지
않았으며 증발기 첫 단에 투입된 증기가 전체 공정의 에너지원으로 작동된다. Case 2-5는 이젝터의 장착위치에 따라 증발기에서 저압 상태로 분리된
증기를 재압축하여 증발시스템에 재사용하게 된다.
Fig. 2. Schematic of the falling film evaporator(Source by GEA Group).
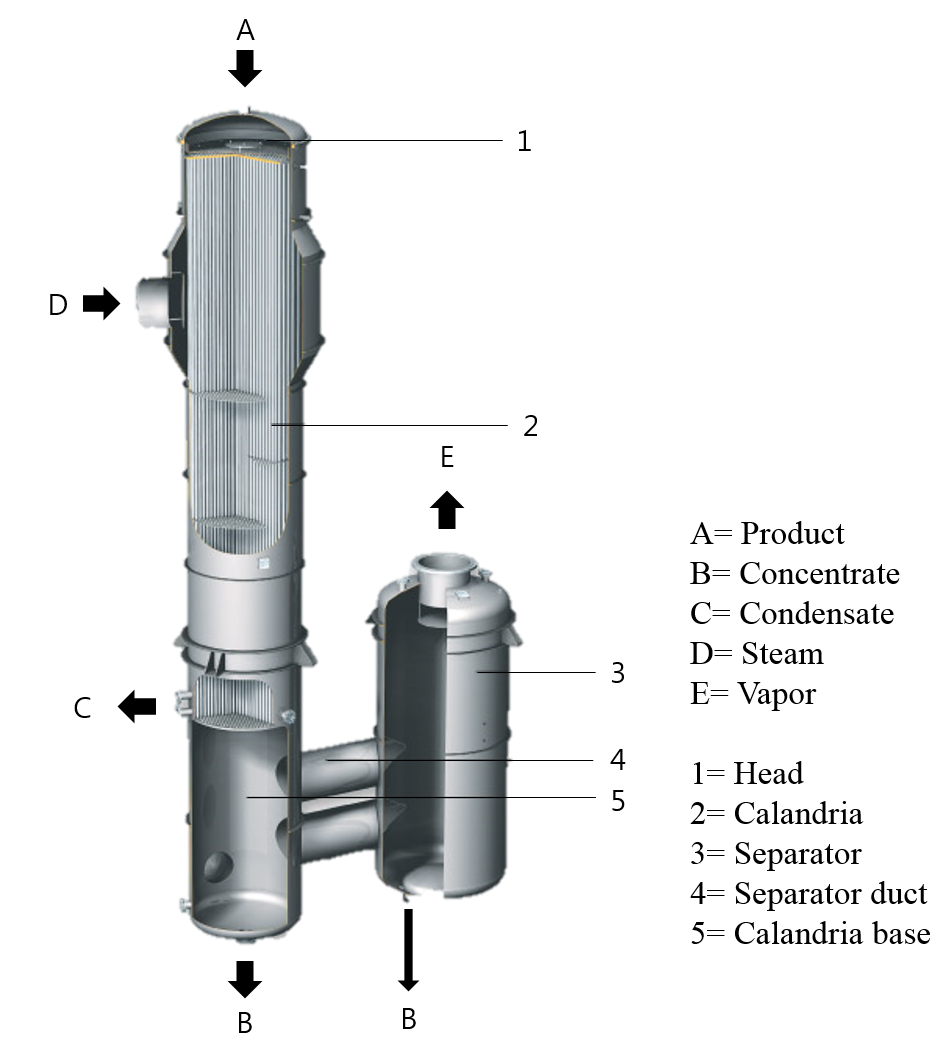
Fig. 3. Process diagram of multiple effect evaporators.
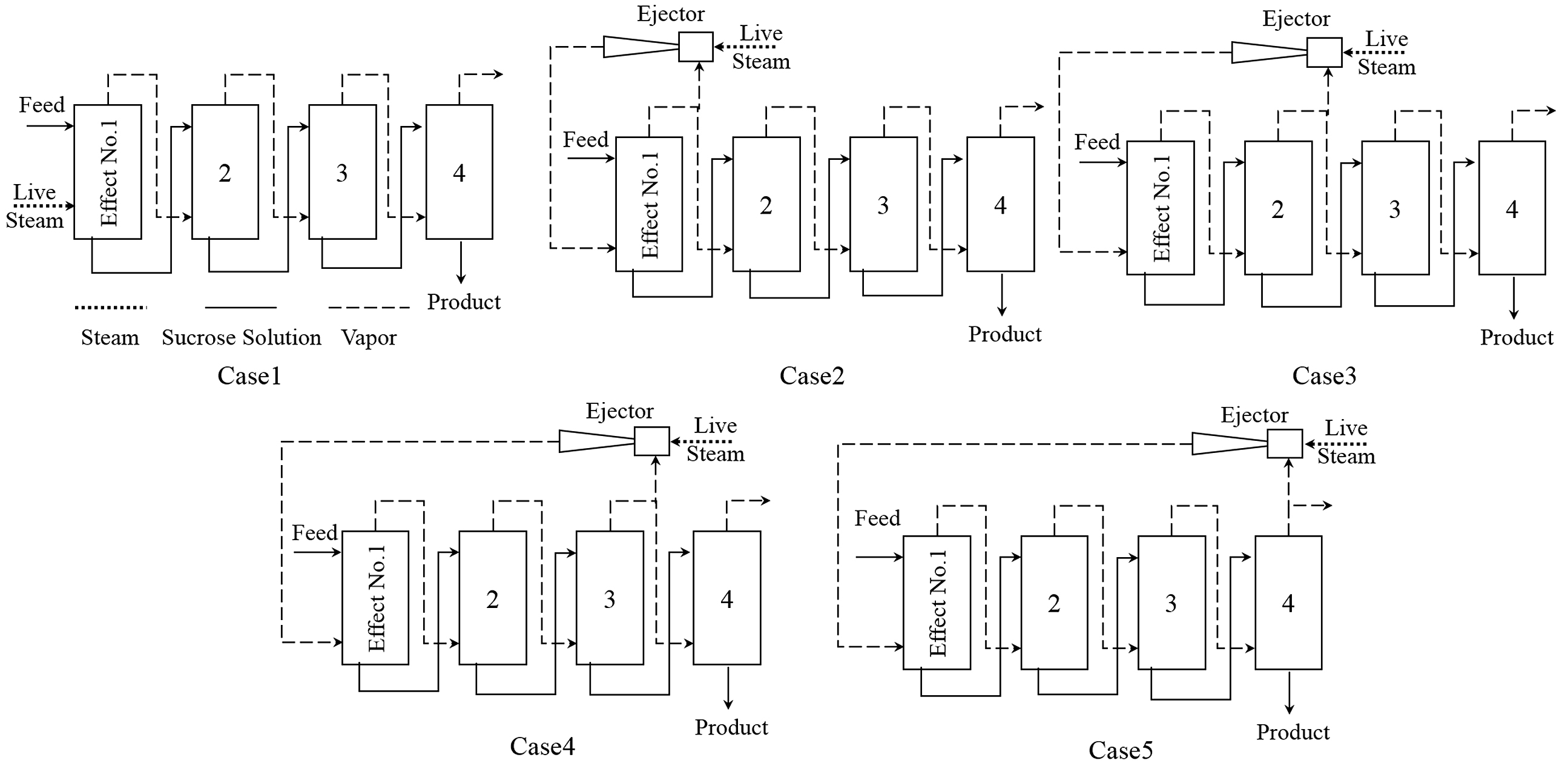
2.3 지배방정식
Fig. 4는 1단 증발시스템의 구성도이며 증발기는 용액의 분리가 일어나는 vapor space와 열교환이 이루어지는 steam chest로 나뉜다. 증발시스템을
구성하는 지배방정식은 다음과 같다.
Fig. 4. Block diagram of a single effect evaporator.
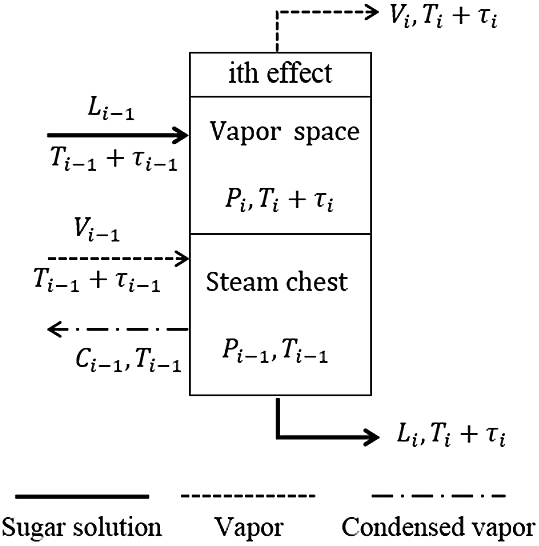
2.3.1 에너지 정산
시스템 외부로의 열손실은 무시한 입, 출구 질량유량에 따른 엔탈피 정산방정식으로 식(1)을 구성하였다.
2.3.2 질량 균형
식(3)은 증발기에 유입된 증기와 용액의 합은 유출되어 나가는 증기와 용액의 합과 동일하게 적용하였고 용액 속에 녹아있는 용질의 양은 일정하게 두어 식(4)를 구성하였다.
2.3.3 열전달
식(5)는 steam chest에서 교환되는 열량의 균형식이며 증기의 응축에너지와 용액과 증기 사이의 온도차를 이용하여 열출입량 정산방정식을 구성하였다.
2.3.4 비등점 상승 및 증기압 내림
식(6)은 용액의 농도에 따른 끓는점 증가를 나타낸 식이다. 수용액의 경우 순수한 용매와는 달리 용액의 표면에 비휘발성 용질입자들이 용매 분자의 증발을 방해하기
때문에 순수한 용매보다 상대적으로 증기압력이 낮아진다. 증기압력이 낮아짐에 따라 동일한 압력에서 끓는점은 상승하게 되며 용액의 포화압력은 끓는점 증가가
고려되지 않은 순수한 용매의 포화압력과 같게 된다. Fig. 5는 물과 수용액의 상변화 그래프이며
는 주어진 압력에서 물의 끓는점이고
는 수용액의 끓는점이다. 수용액의 끓는점,
의 포화압력은 순수한 용매의 끓는점,
에서의 포화압력과 같다.(5)
Fig. 5. Phase diagram of pure solvent and solution.
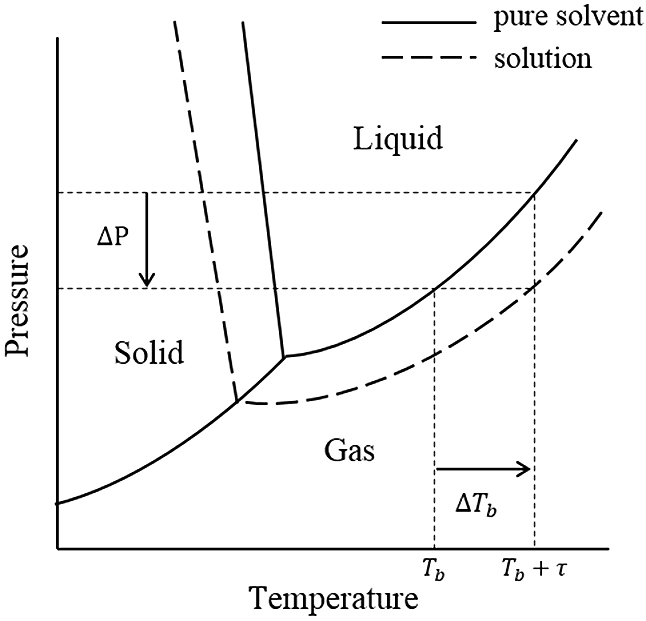
2.3.5 비열
식(7)은 용액의 농도에 따른 비열 변화식이며, 용액이 농축됨에 따라 용액의 농도에 따른 비열의 변화를 증발기를 구성하는 모델에 적용해야 한다.(5)(5)
2.3.6 열전달계수
Adib et al.(6)에 의하면 총괄열전달계수 U는 식(8)과 같으며 튜브 내부의 열저항(1/hi), 튜브 외부의 가열된 증기 측 열저항(1/hv), 튜브벽면 전도 열저항(e/λw), 오염저항(RF)으로 구성되어있고
튜브 내부의 열저항과 오염저항의 경우 식(9)의 관계로 정의하였다. 식(10)은 steam chest 부분에서 증기와 용액사이의 교환된 열량을 나타내며
는 용액과 steam chest의 온도차이를 의미하며 이때의 열전달계수는 식(11)과 같이 steam chest 부분에서의 열용량(
), 열교환기 튜브의 단위 길이당 용액의 질량 유량(
), 용액의 농도(x), 증기의 증발 온도(T)에 따라 결정된다.
2.4 대상 모형 타당성 검증
성능 분석에 사용된 증발기 모델과 이젝터 모델의 타당성 검증을 위해 문헌자료에 나온 모델링 결과와 비교하였다.
2.4.1 다중효용증발시스템
Kaya et al.(7)는 설탕공장의 운전정보를 기준으로 수학적 모델링을 적용하여 용액의 공급방법과 예열기 사용유무에 따른 투입증기와 각 증발기에서 증발된 수분 량을 계산하였다.
본 연구에 사용된 증발기 모델의 검증을 위해 Kaya의 모델링 결과를 사용하였으며 4단 증발시스템에 예열기를 사용하지 않은 설탕 수용액을 순방향으로
공급한 결과 값과 비교하였다. Table 1은 용액과 증기의 투입온도와 각 증발기의 온도분포, 투입되는 용액의 질량유량과 농도를 나타낸 표이다. 동일한 조건에서의 검증을 위해 Case 1의
TVR을 적용하지 않은 4단 증발시스템에 Table 1의 운전조건을 적용하여 결과값을 비교하였다. Table 2는 증발시스템에 투입된 증기량과 각 증발기에서 증발된 수분량에 대한 결과이다. Table 1의 운전조건에서 Kaya의 모델과 본 연구의 성능 분석에 사용된 모델의 비교 결과는 Table 2와 같으며 Kaya의 모델링 값과 계산 값의 오차는 0.2~1.4[%]로 상대적으로 낮은 오차율을 보였다. 오차의 원인은 성능 분석에 사용된 증발기
모델의 열전달계수에 대한 정의와 증발기의 열전달면적을 동일하게 가정하여 계산하였기 때문이다. 비교대상은 실측데이터가 아닌 수학적 모델링을 통한 결과
값이므로 상대오차는 작았으며 동일한 운전조건에서 유사한 결과값을 확인하였다.
Table 1. Input conditions for evaporator system validation
Tf
|
308.15
|
F
|
27.78
|
Ts
|
384.55
|
x4
|
65
|
T1
|
372.78
|
xf
|
15
|
T2
|
363.10
|
|
|
T3
|
354.48
|
|
|
T4
|
342.25
|
|
|
Table 2. Validation results of evaporator system
|
solution
|
calculation
|
error[%]
|
Vs
|
8.19
|
8.31
|
1.4
|
V1
|
5.00
|
5.08
|
1.6
|
V2
|
5.30
|
5.31
|
0.2
|
V3
|
5.47
|
5.44
|
0.6
|
V4
|
5.60
|
5.54
|
1.1
|
2.4.2 증기 이젝터
증기 이젝터 성능 모델의 타당성 검증을 위해 Lee et al.(8)의 모델링 결과값을 이용하였으며 내부 노즐의 지름(d1), 외부 노즐의 지름(d2), 목의 지름(d3)의 비교를 통해 이젝터 모델의 검증을 하였다. Table 3의 초기조건을 증기 이젝터 성능 모델에 적용하여 Table 4의결과를 얻었다. 이젝터의 크기를 계산할 때 El-Dessouky et al.(9)의 모델링에 적용된 동일한 식을 적용하였기 때문에 오차는 작았다. 하지만 d2, d3 에서 약 0.7~0.8[%]의 오차가 발생하였다. 이는 반올림 오차와 온도에 따른 포화 압력에 대한 계산식의 차이 이며 동일한 조건에서 유사한 결과값을
확인하였다.
Table 3. Input conditions for steam ejector validation
Entrainment ratio
|
1.1
|
Primary flow rate[kg/h]
|
16,545
|
Pp, Pe, Pc
|
15, 0.235, 1.2
|
Tp, Te, Tc
|
475.2, 379.1, 396.8
|
ηn, ηd
|
0.85, 0.85
|
Table 4. Validation results of steam ejector
|
solution
|
calculation[kg/h]
|
error[%]
|
d1
|
52.4
|
52.4
|
0.0
|
d2
|
104.3
|
105.1
|
0.8
|
d3
|
242.8
|
244.4
|
0.7
|
2.5 단위공정 설계 및 성능계산
사례별 연구를 진행하기에 앞서 기본적인 공정설비(강하막식 증발기, 증기 이젝터)의 크기를 파악하였으며 이에 따른 다중효용증발시스템과 증기 이젝터의
성능 계산을 하였다.
2.5.1 단위공정 설계
(1) 다중효용증발시스템
증발공정을 구성하는 주요 장치는 강하막식 증발기이다. 증발기는 열교환기로 구성되며 4개의 증발기의 열전달면적은 2,000㎡ 로 동일하게 가정하였다.
공정에 채택된 열교환기의 튜브의 외경, 내경과 길이를 각각 38.1 mm, 34.8 mm, 5 m로 가정하였으며 튜브 피치를 외경의 1.25배의
값으로 계산하였다. 계산결과 증발기의 직경은 2,912 mm가 나왔으며 증발시스템은 길이 5m, 외경 2,912 mm 규모의 증발기를 채택하여 공정성능을
파악하였다.
(2) 증기 이젝터
이젝터의 주요 부의 크기인 내부 노즐 직경(d1), 외부 노즐 직경(d2), 디퓨저 입구 직경(d3)을 계산하였다. 이젝터의 크기는 작동유체의 유량, 압력과 온도에 따라 변화하며 면적 계산은 El-Dessouky et al.(9)의 모델링을 이용하였다. 면적 계산을 위한 식은 부록에 표기하였으며 노즐과 디퓨저의 효율을 1로 가정하였을 경우 계산 결과는 Table 5와 같다. 동일한 조건의 구동증기가 투입 되므로 내부노즐의 직경은 동일한 값으로 계산 되었다. 외부 노즐의 직경은 Case 5가 가장 높았으며 2차
증기(흡입증기)의 압력이 낮을수록 외부 노즐의 크기는 증가하였다. 디퓨저 입구의 직경은 유량비에 비례하고 2차 증기의 압력에 반비례하므로 이젝터 장착
위치에 따른 크기변화의 경향성은 일정하지 않았다.
Table 5. Dimensions of ejector
|
Case 2
|
Case 3
|
Case 4
|
Case 5
|
d1
|
69
|
69
|
69
|
69
|
d2
|
123
|
129
|
137
|
158
|
d3
|
311
|
278
|
278
|
308
|
2.5.2 성능계산
Table 6은 Case 2~5의 증발시스템의 초기 운전조건이다. 424.15 K, 490 kPa의 증기가 2.8 kg/s로 공급되고 333.15 K, 20 kPa,
20.9%의 용액이 22.2 kg/s로 투입되며 용액의 출구온도를 332.23 K로 동일하게 가정하였을 때 증기이용율을 이용하여 증발성능을 파악하였으며
이젝터의 장착위치에 따른 이젝터의 유량비, 압축비, 팽창비를 비교하여 이젝터의 성능을 분석하였다.
증기이용율(Steam economy)
유량비(Entrainment ratio)
압축비(Compression ratio)
팽창비(Expansion ratio)
2.6 모형계산의 가정 및 한계점
2.6.1 다중효용증발시스템 설계 및 성능분석
증발기를 통과하는 모든 증기는 포화상태로 가정하였고 기기간의 열손실 및 압력강하는 고려하지 않았다. 증발기모델은 0차원 모형을 가정하여 단순화하였으며
0차원 모형은 입, 출구 조건만으로 계산되어 반응기 내부의 위치에 따른 열/물질정산과 열전달속도, 체류 시간 등에 대한 고려는 하지 않았다.
2.6.2 이젝터 설계 및 성능분석
이젝터 내부 유동을 등엔트로피 상태로 가정하였으며 주유동부의 구동증기와 회수되는 2차 증기의 속도는 고려하지 않았다. 구동증기와 2차 증기는 흡입실에서
혼합되며 모든 유동은 단열 상태로 가정하여 이젝터의 성능 및 크기를 계산하였다.
3. 다중효용증발시스템 성능분석
3.1 다중효용증발기 온도분포 분석
Fig. 6은 TVR을 적용한 Case 2-5의 증발기의 온도분포도를 나타낸 그래프이다. 용액의 출구온도는 초기조건으로 가정하였으므로 1, 2, 3단의 증발기의
온도만을 고려하여 비교하였다. 이젝터를 증발시스템의 후단에 배치할수록 증발시스템의 전체적인 온도분포도는 상승되었으며 증발기의 후단으로 갈수록 증발기의
온도는 하강하였다. 증발기의 압력은 온도에 따른 포화압력으로 가정하였으므로 증발기 후단으로 갈수록 온도 감소에 따른 증발기의 압력은 감소한다.
Fig. 6. Temperature distribution of multiple effect evaporator system.
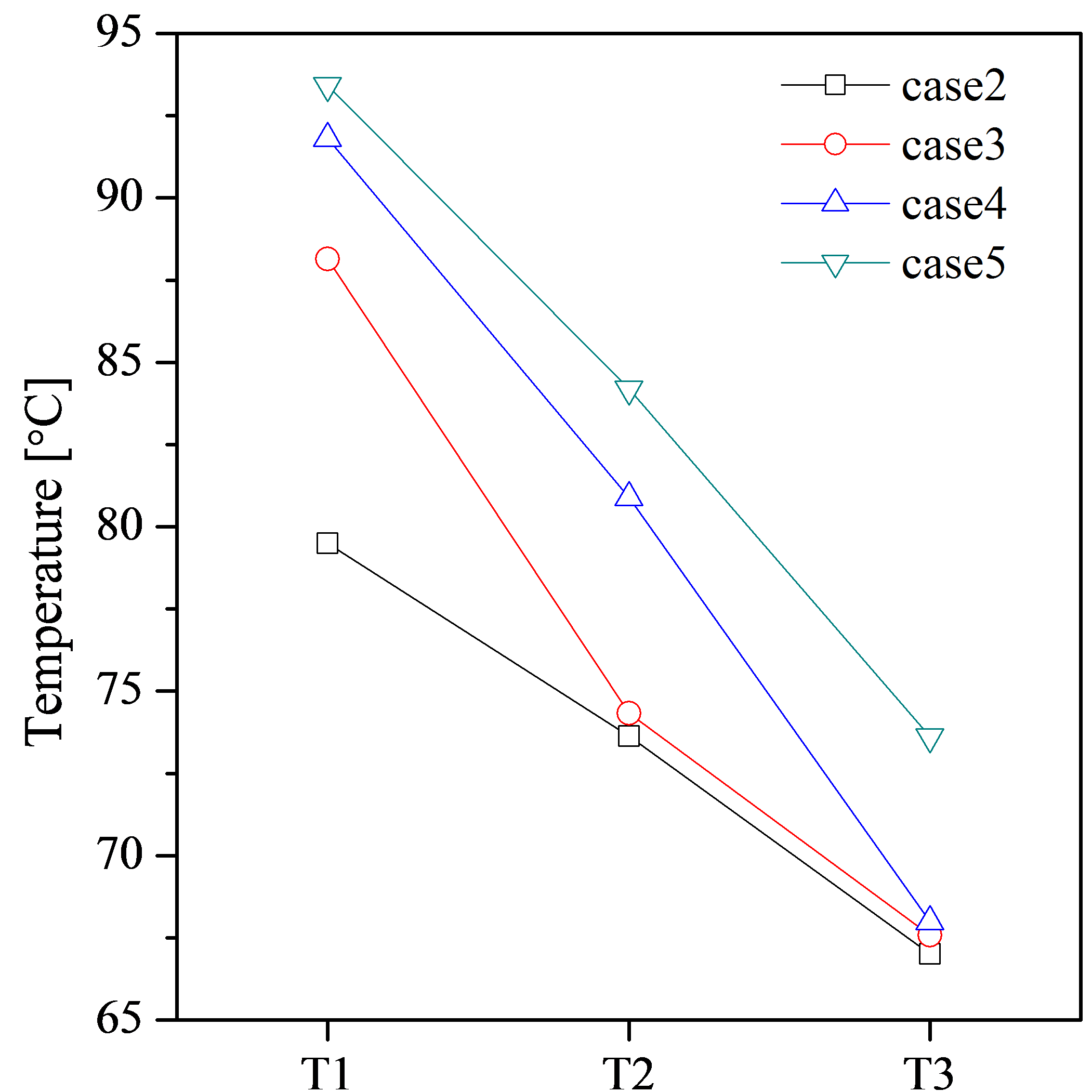
3.2 다중효율증발기 및 TVR 성능분석
Fig. 7은 Case 1-5의 증기이용율을 비교한 그래프이다. TVR을 적용하지 않은 증발시스템인 Case 1보다 TVR을 장착한 Case 2-5의 증발 효율이
더 높았으며 이젝터를 증발기의 후단으로 장착 할수록 증발성능은 향상 되었다. Case 2-5의 증기이용율의 증가폭은 감소하였지만 증기이용율은 증가하는
경향을 보였으며 이젝터를 증발기의 마지막 단에 장착한 Case 5의 증기이용율이 가장 높았다.
Fig. 7. Evaporation performance comparison.
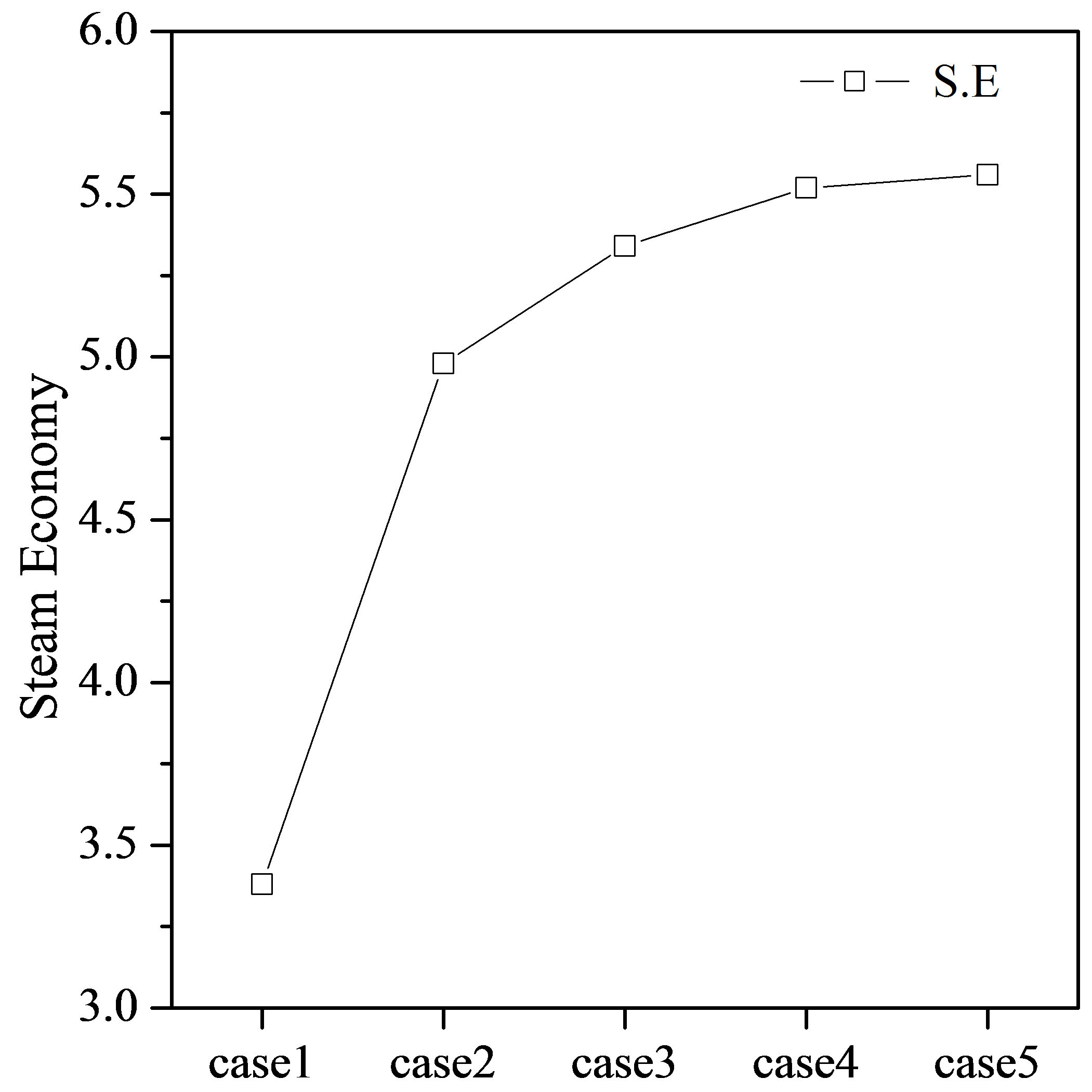
Fig. 8은 TVR을 적용한 Case 2-5의 이젝터 성능을 비교한 그래프이다. 이젝터를 증발기의 후단으로 배치할수록 팽창비(Er)와 압축비(Cr)는 증가하였으며
구동증기의 유량대비 회수되는 증기유량의 감소로 유량비(w)는 감소하였다. Fig. 6의 그래프를 통해 증발기 후단으로 갈수록 증기의 온도는 하강하며
이에 따른 압력은 감소함을 확인하였다. 따라서 이젝터를 증발기의 후단으로 배치할수록 2차 증기의 압력은 감소되며 동일한 조건의 구동압력에 대한 2차
증기의 압력의 감소에 따라 팽창비(Er)는 상승한다. 또한 이젝터에서 2차 증기의 압력대비 배출되는 증기의 압축비(Cr) 또한 상승되므로 이젝터가
증발시스템의 후단부에 배치 될수록 이젝터 내에서 증기의 압축은 더 높은 비율로 진행된다.
Fig. 8. Ejector performance comparison.
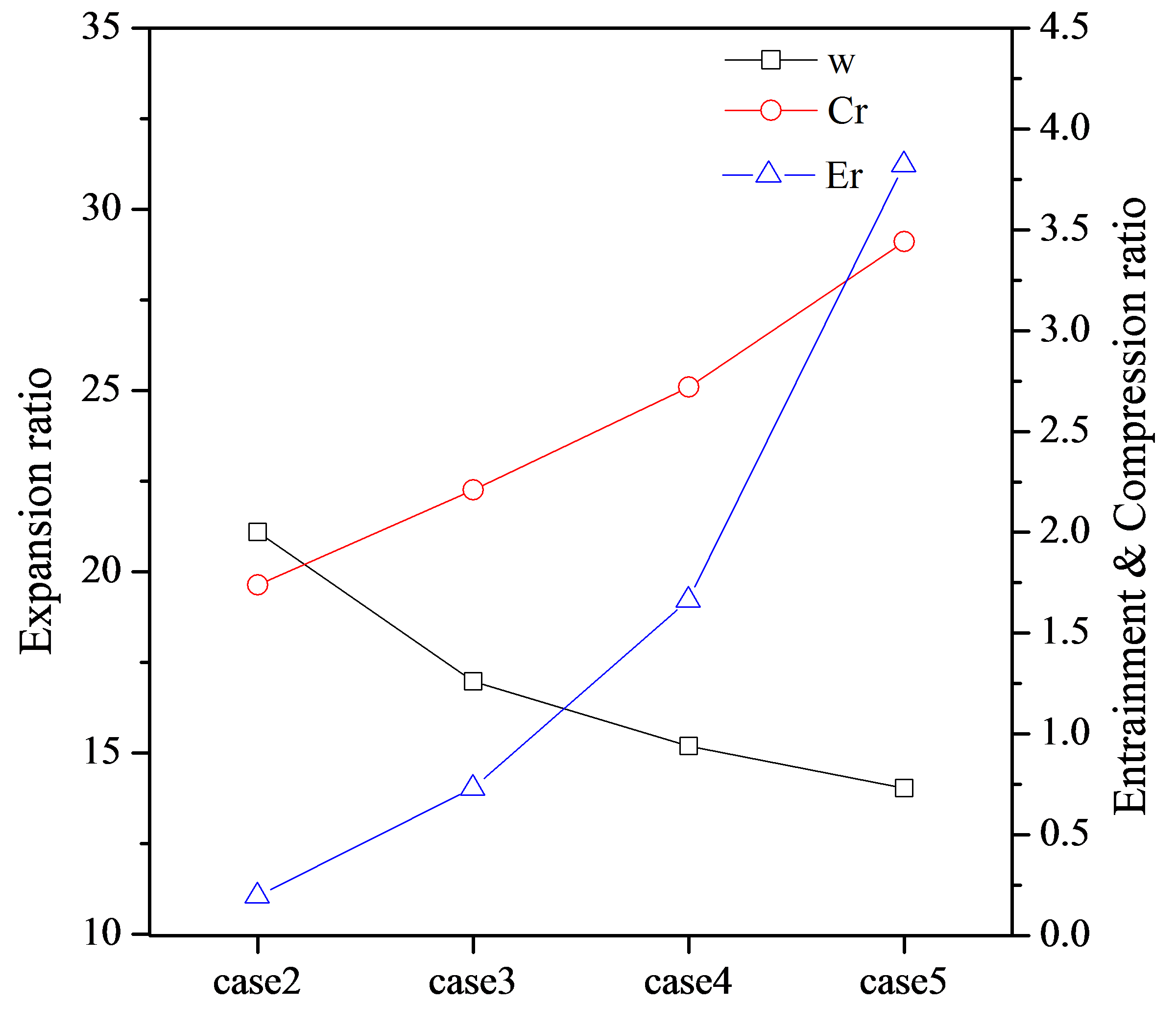
4. 결 론
다중효용증발시스템의 증기이용율과 이젝터의 유량비, 압축비, 팽창비의 비교를 통해 증발기와 이젝터의 성능을 분석하였다. 증발시스템을 구성할 때 이젝터를
증발기 후단으로 배치할수록 증기이용율의 증가로 증발성능은 향상되고 이젝터로 흡입되는 증기의 압력이 낮아짐에 따라 유량비는 감소하며 압축비 및 팽창비는
증가하므로 이젝터 내에서 흡입증기는 더 높은 비율로 압축되어 증발시스템에 공급됨을 확인하였다. 본 연구를 통해 증발시스템에 채택된 증기 이젝터의 허용
가능한 성능에 따라 증기 이젝터의 장착위치에 대한 기본적인 정보를 제공할 수 있다.
후 기
본 연구는 한국과학기술원 가치제조 기계 사업단(BK21플러스)의 지원을 받았으며, 이에 감사드립니다.
References
Walmsley, T. G., Walmsley, M. R. W., Neale, J. R., Atkins, M. J., 2015, Pinch
Analysis of an Industrial Milk Evaporator with Vapour Recompression Technologies,
The Italian Association of Chemical Engineering, Vol. 45, pp. 7-12

Hamed O. A., Zamamiri A. M., Aly S., Lior N., 1995, Thermal Performance and Exergy
Analysis of a Thermal Vapor Compression Desalination System, Energy Convers. Mgmt.,
Vol. 37, No. 4, pp. 379-387

Kim D. W., Choi S. M., 2016, Design and evaluation of multiple effect evaporator systems
for concentrating black liquor, 52nd The Korean Society of Combustion (KOSCO) Symposium,
Buyeo, Korea, pp. 279-281

Kern D. Q., 1950, Process Heat Transfer, McGraw-Hill.

Christie J. G., 2003, Transport Processes and Separation Process Principles 4thed,
Prentice Hall.

Abid T. A., Heyd B., Vasseur J., 2009, Experimental results and modeling of boiling
heat transfer coefficients in falling film evaporator usable for evaporator design,
Chemical Engineering and Processing, Vol. 48, No. 4, pp. 961-968

Kaya D., Sarac H. I., 2007, Mathematical modeling of multiple-effect evaporators and
energy economy, Energy, Vol. 32, No. 8, pp. 1536-1542

Lee C. M., Lim J. Y., Yun R., 2015, Investigation of MVR and TVR in Chemical Processes
by Using Waste Steam, Korean Journal of Air-Conditioning and Refrigeration Engineering,
Vol. 27, No. 4, pp. 201-206

El-Dessouky H., Ettouney H., Alatiqi I., Al-Nuwaibit G., 2002, Evaluation of steam
jet ejectors, Chemical Engineering and Processing, Vol. 41, No. 6, pp. 551-561

Sarma G., Barma S. D., 2010, Energy Management in Multiple-Effect Evaporator System
: A Heat Balance Analysis Approach, Gen. Math. Notes, Vol. 1, No. 2, pp. 84-88

Nayak, M., 2012, Design and simulation of a multiple effect evaporator using vapor
bleeding, A Thesis of Bachelor degree in Chemical engineering, National Institute
of Technology, Rourkela, India.

Holland C. D., 1975, Fundamentals and modeling of separation processes, Prentice Hall.

Geankoplis, C. J., 2003, Transport processes and Separation Process Principles 4thed,
Prentice Hall.
